申请日2017.01.19
公开(公告)日2017.06.30
IPC分类号C01F5/40; C01C1/02; C02F9/10; C02F103/34
摘要
本发明公开了一种镁法处理含硫酸铵工艺废水并回收硫酸镁的方法,将分解剂加入到含有硫酸铵的废水中,在一定条件下使分解剂中的氧化镁与废水中的硫酸铵发生复分解反应,生成氨和硫酸镁。在加热条件下氨伴随着蒸汽逸出,经冷凝、吸收制得低浓度氨水(7‑10%),也可经汽提进一步将氨水增浓至20‑28%之间。铵分解反应完成后,对铵解料浆进行过滤,收得硫酸镁溶液,将硫酸镁溶液在不蒸发的条件下送入多功能七水硫酸镁结晶器,经结晶、分离收得七水硫酸镁产品。实现硫酸铵废水处理的低消耗化、低成本化、无害化和效益化的目标。
摘要附图
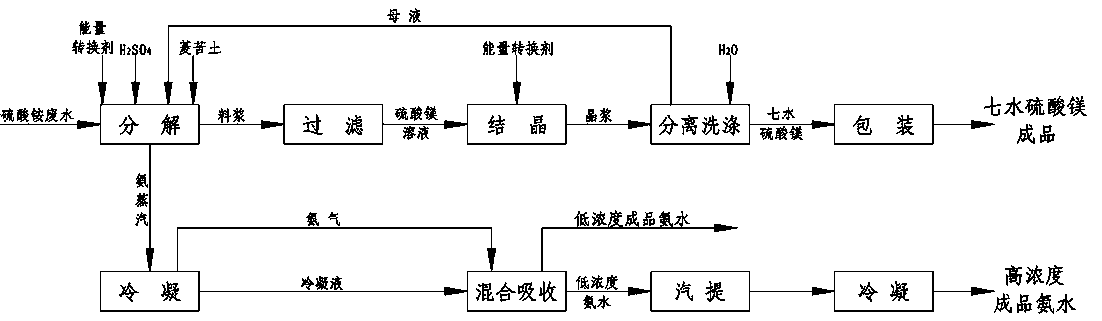
权利要求书
1.一种镁法处理含硫酸铵工艺废水并回收硫酸镁的方法,其特征在于按下述工艺操作:
(1)以制得硫酸镁浓度为280-550g/L的硫酸镁溶液为控制标准,分析含硫酸铵废水中的硫酸铵浓度和分解剂中氧化镁含量,并以此为依据计算处理单位体积硫酸铵废水所需加入分解剂的量,使废水中硫酸铵完全分解并使所生成的硫酸镁溶液浓度达到280-550g/L;
(2)将含硫酸铵废水定量地送入分解工序,分解工序所用设备为多功能专用铵解反应器,按每1m³含硫酸铵废水50-320kg的量加入能量转换剂,再加入与所加能量转换剂等当量的分解剂,利用能量转换剂所释放的热量使反应体系温度提升至85-95℃;
(3)向反应体系中继续加完剩余的分解剂,使溶液中的硫酸铵与分解剂反应,生成氨和硫酸镁,过程以蒸汽补充热量维持反应体系温度,反应60-120min至硫酸铵分解完全,再加硫酸使未反应的分解剂得到分解,反应完成后过滤,得硫酸镁溶液;
(4)将过滤所得浓度为280-550g/L的硫酸镁溶液直接送多功能硫酸镁结晶器,采用真空冷却的方式进行降温,同时进行绝热蒸发;当结晶液体系温度下降到35-65℃时,再按每立方结晶液50-320kg的量向结晶液中加能量转换剂,利用能量转换剂所释放的热量使结晶体系温度恢复至85℃以上,然后再采用真空冷却的方式进行降温使温度下降至35—65℃;
真空冷却过程水分蒸发量控制:水蒸发量为所处理铵氮废水及循环母液总量的8-20%,真空冷却过程应控制在60-120min;当结晶体系温度下降至35-65℃时,停止负压操作,在常压条件下以循环水为冷却剂,采用强制冷却的办法将结晶体系温度冷却至20-30℃,结晶结束;然后经分离、洗涤、包装制得七水硫酸镁产品;硫酸镁结晶率大于80%,所得七水硫酸镁母液含有能量转换剂,占被处理硫酸铵废水及循环母液总量的20-25%,硫酸镁浓度在230-260g/L,返回铵分解工序混合配料;
(5)铵分解过程在负压条件下进行,通过负压使反应体系沸点降低,使所生成的氨溶解度下降,并将所产生的氨蒸汽引入到由冷凝、混合吸收装置组成的氨水制备系统,在全封闭条件下经冷凝、吸收制得浓度为7-10%的氨水;如需制得高浓度氨水,则可将所得7-10%的氨水送入汽提蒸氨塔,经汽提、冷凝收得浓度为20-28%的氨水;铵分解过程分为前后三个阶段,第一阶段为能量转换阶段,以能量转换剂所释放的热量使反应体系温度提升到85-95℃,以减少蒸汽消耗;第二阶段为复分解反应阶段,由分解剂与硫酸铵反应,生成氨和硫酸镁;第三阶段为强化分解阶段,由硫酸分解反应体系中未反应的分解剂,使分解剂分解完全,铵分解过程水分蒸发量控制:水蒸发量为所处理铵氮废水及循环母液总量的25-35%。
2.如权利要求1所述的镁法处理含硫酸铵工艺废水并回收硫酸镁的方法,其特征在于:所述分解剂为白云石粉、菱苦土、水镁石粉、菱镁矿粉中的一种或多种混合而成。
3.如权利要求1所述的镁法处理含硫酸铵工艺废水并回收硫酸镁的方法,其特征在于:所述的能量转换剂为质量分数25%—98%的硫酸。
说明书
一种镁法处理含硫酸铵工艺废水并回收硫酸镁的方法
技术领域
本发明属于废水处理技术领域,具体涉及一种以镁法处理含硫酸铵工艺废水回收氨水,并在不消耗蒸汽的条件下生产硫酸镁的方法。
背景技术
铵氮废水是指在镁盐、冶金、无机颜料、电子等行业生产过程所产生的含有铵盐,如:硫酸铵、氯化铵等成份的工艺废水。如予排放,不仅会对环境造成严重污染,而且会造成铵资源的流失。
现有技术中对铵氮废水的处理方法,目前主要有以下几种:一是将铵氮废水浓缩,结晶收得铵盐;二是以氧化钙或氢氧化钙与铵氮废水中的铵盐反应,使铵盐分解,生成氨和钙盐。当铵氮废水中的铵盐为硫酸铵时,过滤后得含氨溶液和硫酸钙滤饼,将含氨溶液汽提制得工业氨水,将硫酸钙滤饼洗涤干燥制得副产硫酸钙。当铵氮废水中的铵盐为氯化铵时,将氧化钙或氢氧化钙与铵氮废水中的氯化铵反应,生成氨和氯化钙,分解过程氨逸出,经吸收、汽提制得工业氨水,铵解残液经蒸发结晶收得氯化钙产品;三是以氢氧化钠与铵氮废水中的铵盐反应,使铵盐分解生成氨和钠盐,吸收挥发出的氨制得低浓度氨水,再经汽提制得工业氨水;四是以菱苦土(轻烧氧化镁)与铵氮废水中的铵盐反应,使铵盐分解并挥发出氨,再经吸收、汽提制得氨水,将铵解残液蒸发、结晶收得副产镁盐。
在上述工艺中,将铵氮废水浓缩、结晶收得铵盐工艺虽然可以收得铵盐产品,但处理过程能耗较高,成本难以控制,加之铵盐产品附加值较低,因此难以获得经济效益。钙法工艺为成熟的铵氮废水处理工艺,但存在的问题是,当铵氮废水中的铵盐为硫酸铵时,有大量的副产石膏产生,销售与环境负担沉重。当铵氮废水中的铵盐为氯化铵时,在收得副产氯化钙时需要对铵解残液进行蒸发,能耗较高。氢氧化钠法处理铵氮废水成本较高,而且有大量的含有钠盐铵解残液排放,对环境有影响。以菱苦土(轻烧氧化镁)处理铵氮废水,即镁法工艺,近年已有报道,其优点是处理过程无二次残渣产生,对铵解残液可以综合利用,但缺点是处理过程蒸汽消耗量相对较大。
发明内容
为解决现有技术存在的上述缺陷,本发明的目的在于提供一种镁法处理含硫酸铵工艺废水并回收硫酸镁的方法,实现硫酸铵废水处理的低消耗化、低成本化、无害化和效益化的目标。
为实现上述目的,本发明采用的技术方案:该镁法处理含硫酸铵工艺废水并回收硫酸镁的方法,其特征在于按下述工艺操作:
1、以制得硫酸镁浓度为280-550g/L的硫酸镁溶液为控制标准,分析含硫酸铵废水中的硫酸铵浓度和分解剂中氧化镁含量,并以此为依据计算处理单位体积硫酸铵废水所需加入分解剂的量,使废水中硫酸铵完全分解并使所生成的硫酸镁溶液浓度达到280-550g/L;
2、将含硫酸铵废水定量的送入分解工序,分解工序所用设备为多功能专用铵解反应器,按每1m³含硫酸铵废水50-320kg的量加入能量转换剂,再加入与所加能量转换剂等当量的分解剂,利用能量转换剂所释放的热量使反应体系温度提升至65-100℃;
3、向反应体系中继续加完剩余的分解剂,使溶液中的硫酸铵与分解剂反应,生成氨和硫酸镁,过程以蒸汽补充热量维持反应体系温度,反应60-120min至硫酸铵分解完全,再加硫酸使未反应的分解剂得到分解,反应完成后过滤,得硫酸镁溶液;
4、将过滤所得浓度为280-550g/L的硫酸镁溶液直接送多功能硫酸镁结晶器,采用真空冷却的方式进行降温,同时进行绝热蒸发;当结晶液体系温度下降到35-65℃时,再按每立方结晶液50-320kg的量向结晶液中加能量转换剂,利用能量转换剂所释放的热量使结晶体系温度恢复至65℃以上,然后再采用真空冷却的方式进行降温使温度下降至35—65℃,真空冷却过程水分蒸发量控制:水蒸发量为所处理铵氮废水及循环母液总量的13-15%,真空冷却过程应控制在60-120min;当结晶体系温度下降至45-50℃时,停止负压操作,在常压条件下利用盘管换热器或夹套换热器,以循环水为冷却剂,采用强制冷却的办法将结晶体系温度冷却至20-30℃,结晶结束;然后经分离、洗涤、包装制得七水硫酸镁产品;硫酸镁结晶率大于80%,所得七水硫酸镁母液含有能量转换剂,占被处理硫酸铵废水及循环母液总量的20-25%,硫酸镁浓度在230-260g/L,返回铵分解工序混合配料;
5、铵分解过程在负压条件下进行,通过负压使反应体系沸点降低,使所生成的氨溶解度下降,并将所产生的氨蒸汽引入到由冷凝、混合吸收装置组成的氨水制备系统,在全封闭条件下经冷凝、吸收制得浓度为7-10%的氨水;如需制得高浓度氨水,则可将所得7-10%的氨水送入汽提蒸氨塔,经汽提、冷凝收得浓度为20-28%的氨水;铵分解过程分为前后三个阶段,第一阶段为能量转换阶段,以能量转换剂所释放的热量使反应体系温度提升到65-100℃,以减少蒸汽消耗;第二阶段为复分解反应阶段,由分解剂与硫酸铵反应,生成氨和硫酸镁;第三阶段为强化分解阶段,由硫酸分解反应体系中未反应的分解剂,使分解剂分解完全,铵分解过程水分蒸发量控制:水蒸发量为所处理铵氮废水及循环母液总量的25-35%。
所述分解剂为白云石粉、菱苦土、水镁石粉、菱镁矿粉中的一种或多种混合而成。
所述的能量转换剂为质量分数25%—98%的硫酸。
本发明的基本工艺原理为:以菱苦土(轻烧氧化镁)为分解剂,将菱苦土(轻烧氧化镁)加入到含有硫酸铵的废水中,在一定条件下使菱苦土(轻烧氧化镁)中的氧化镁与废水中的硫酸铵发生复分解反应,生成氨和硫酸镁。在加热条件下氨伴随着蒸汽逸出,经冷凝、吸收制得低浓度氨水(7-10%),也可经汽提进一步将氨水增浓至20-28%之间。铵分解反应完成后,对铵解料浆进行过滤,收得硫酸镁溶液。将硫酸镁溶液在不蒸发的条件下送入多功能七水硫酸镁结晶器,经结晶、分离收得七水硫酸镁产品。
该镁法处理含硫酸铵工艺废水并回收硫酸镁的方法中,铵分解反应前期以能量转换剂所释放的热量将反应体系温度提升至预定值,使反应体系升温过程不消耗蒸汽、以减少反应过程蒸汽消耗量的方法,利用能量转换剂所释放的热量使反应体系温度提升至65-100℃,目的是免去因反应体系前期加热所发生的蒸汽消耗,不增加蒸汽消耗量的条件下实现对反应体系的浓缩。采用直接吸收方式收得浓度不低于7%的氨水并无尾气排放,在不消耗蒸汽的条件下使铵解残液中硫酸镁结晶率达到80%以上,利用酸效应原理降低硫酸镁溶解度以提高结晶率,结合真空结晶,采用绝热蒸发的方式对结晶液进行浓缩。控制铵分解及硫酸镁生产过程水平衡,铵解残液中硫酸镁浓度280-550g/L,硫酸镁结晶过程水分蒸发量占被处理液总量的13-15%,控制硫酸镁结晶后所得母液量占所投入被处理液量的20-25%,硫酸镁浓度230-260g/L,铵分解过程使蒸发量达到所处理铵氮废水及循环母液总量25-35%。与现有技术相比,本专利的优点:
1、以菱苦土(轻烧氧化镁)处理含硫酸的工艺废水使铵得到分解,在回收氨水的同时制得了市场前景较好的七水硫酸镁,经济效益好。
2、处理过程无废气、废渣、废水产生。
3、处理过程蒸汽消耗量低,有利于降低和控制处理成本。