申请日2015.03.30
公开(公告)日2015.07.22
IPC分类号C02F103/30; C02F1/52
摘要
本发明涉及一种用于印染废水处理的复合脱色絮凝剂的制备方法。先用酸洗废水和硫酸溶解含铝废渣,然后加入Mg2+、Zn2+和Mn2+,再加入氯酸盐氧化Fe2+消耗酸使Fe3+、Al3+等水解聚合;然后加入硅烷偶联剂水解调聚,再加入双氰胺-三乙烯四胺缩聚物,保温熟化得复合脱色絮凝剂。本发明所得产品含多种利于与废水污染物作用的成分,分子聚集体较大,各成分协同作用对印染废水具有优异的脱色、去COD和除浊效果,且不引入新污染;一般只需经絮凝一步就能达到GB4287-2012排放标准,简化工艺,降低成本。本发明可同时处理钢铁酸洗废水和铝材加工含铝废渣,实现资源化利用,且工艺简单,易于实现工业化,应用前景广阔。
摘要附图
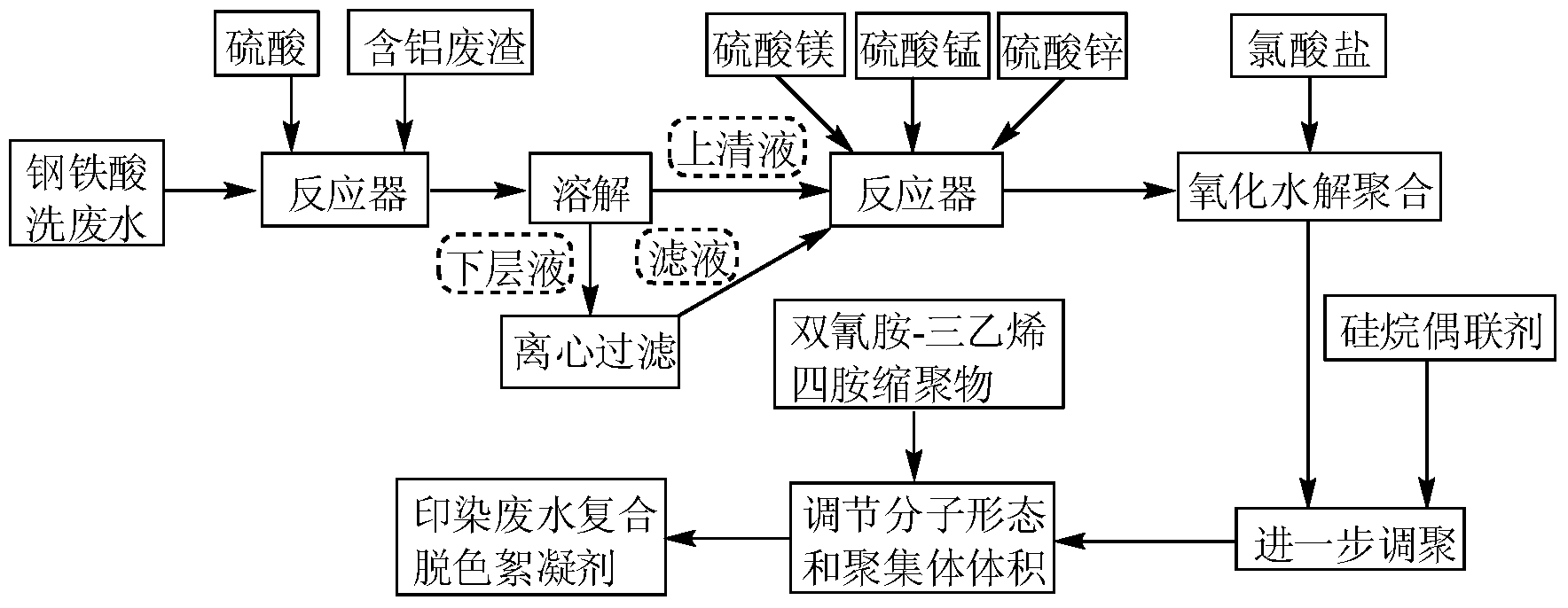
权利要求书
1.一种用于印染废水处理的复合脱色絮凝剂的制备方法,其特征在于,包括以下步骤:
(1)将酸洗废水、硫酸和含铝废渣按质量比100∶8.6~9.8∶4~6配料,先将酸洗废水 和质量分数为95~98%的硫酸加入到反应器中,然后加入含铝废渣,升温至70~90℃搅拌至 溶解,静置,上清液转入另一个反应器中,再在该反应器中转入下层分离渣后的液体;
(2)按硫酸镁、硫酸、硫酸锌与酸洗废水30~190∶1~20∶1~20∶100的质量比在步骤 (1)所得溶液中加入硫酸镁、硫酸锰和硫酸锌,再加入酸洗废水体积2.8~3.2倍的水,升 温至70~80℃搅拌至固体物质完全溶解;然后按与上述溶液中Fe2+0.085~0.17∶1的物质的 量比加入氯酸盐氧化水解0.5~1小时后,按与总铁1.0∶20~30的物质的量比缓慢加入硅烷 偶联剂,在70~80℃下继续反应2~3小时;
(3)降低温度至40~60℃,按与酸洗废水的总铁0.75~1.25∶1的质量比加入双氰胺- 三乙烯四胺缩聚物,搅拌均匀,保温熟化3~4小时,即得粘稠的红色或橙红色印染废水复 合脱色絮凝剂。
2.根据权利要求1所述的用于印染废水处理的复合脱色絮凝剂的制备方法,其特征在 于:所述步骤(1)中的酸洗废水为钢铁酸洗废水,其主要成分为:总铁浓度为2.45~2.65mol/L, 亚铁浓度为2.25~2.54mol/L,H+浓度为0.95~1.25mol/L。
3.根据权利要求1所述的用于印染废水处理的复合脱色絮凝剂的制备方法,其特征在 于:所述步骤(1)中的含铝废渣为铝材加工含铝废渣,即铝材加工过程产生的废水经碱中 和得到的含铝废渣,其主要成分为:氢氧化铝的质量分数为45~55%,Cu2+的质量分数为 0.005~0.01%,Cr3+的质量分数为0.07~0.12%,Ni+的质量分数为0.05~0.08%,Zn2+的质量分 数为0.03~0.05%。
4.根据权利要求1所述的用于印染废水处理的复合脱色絮凝剂的制备方法,其特征在 于:所述步骤(1)的反应器为耐酸密闭式反应器。
5.根据权利要求1所述的用于印染废水处理的复合脱色絮凝剂的制备方法,其特征在 于:所述的硫酸镁、硫酸锰和硫酸锌均为工业级产品,分别为七水硫酸镁、一水硫酸锰和 七水硫酸锌。
6.根据权利要求1所述的用于印染废水处理的复合脱色絮凝剂的制备方法,其特征在 于:所述的氯酸盐为氯酸钠或氯酸钾。
7.根据权利要求1所述的用于印染废水处理的复合脱色絮凝剂的制备方法,其特征在 于:所述的硅烷偶联剂为γ-氨丙基三乙氧基硅烷、γ-缩水甘油醚氧丙基三甲氧基硅烷或γ- (甲基丙烯酰氧)丙基三甲氧基硅烷。
8.根据权利要求1所述的用于印染废水处理的复合脱色絮凝剂的制备方法,其特征在 于:所述的双氰胺-三乙烯四胺缩聚物,单体单元物质的量比为n(双氰胺)∶n(三乙烯四 胺)=2~3∶1。
说明书
一种用于印染废水处理的复合脱色絮凝剂的制备方法
技术领域
本发明属于印染废水处理领域,尤其是涉及一种用于印染废水处理的复合脱色絮凝剂的 制备方法。
背景技术
染料是能够使一定颜色附着在纤维上不易脱落、变色的物质。我国染料产量占世界染料总 产量的60%,居世界首位。每生产1t染料约排放744m3废水,在生产和使用过程中约有10%~20% 的染料释放到水体中,每年有7.56~15.12万吨染料以印染废水的形式直接进入水体环境中。我 国每年产生印染废水约为16亿t,为我国整个工业废水排放第六位。由于印染废水水量大,有机 污染物含量高、成分复杂,且大多是芳烃和杂环化合物,其中带有有色基团(—N=N、—N=O 等)和极性基团(—SO3Na、—OH、—NH2等),因此,色度深,化学需氧量较高且变化大, 生物需氧量(BOD5)相对较小,可生化性差,污染严重。此外,还混有酚类、苯胺、碱等,其 水质随着原材料、生产品种、生产工艺的不同而差异较大,给处理带来了很大困难,因此,印 染废水一直是污染最严重、最难处理的工业废水之一。开发新型高效、经济的处理技术对推进 印染废水的治理具有重要的实际意义。
迄今国内外已研发了多种处理方法,可分为物理方法(吸附法、过滤法、气浮法、膜分 离技术和磁分离法等)、化学方法(絮凝法、氧化法、电化学方法等)和生物处理方法(好 氧、厌氧和厌氧—好氧联用等)等3大类。其中物理方法、絮凝法和电化学方法中的电絮凝电 气浮等属于分离方法,氧化法、电化学氧化、电化学还原和生物法则属于破坏分子结构、降 解有机物的方法。这些方法虽有一定处理效果,但都存在一定的缺点:吸附法中以活性炭为 吸附剂,处理成本较高,活性炭不易再生;采用蒙脱石、海泡石等天然矿物,以及炉渣、剩 余污泥等固体废弃物及其改性产物为吸附剂,虽然成本较低,但吸附容量有限,易产生大量 的废渣而造成二次污染。普通过滤法只适于去除污水中粒径较大的颗粒悬浮物;膜分离技术 用于印染废水处理存在膜设备投资大、渗透通量低、处理过程较复杂、膜污染等问题,因此, 处理成本较高,难以在实际生产中推广应用。磁分离法对操作控制要求高,只能适应部分印 染废水,离推广应用尚有较大距离。氧化法是利用O2、O3等强氧化剂,以及处理过程中产生 的具有强氧化性的羟基自由基(HO·),如Fenton法,使结构稳定甚至很难被微生物分解的 有机分子,转化为无毒无害的可生物降解的低分子物质,或生成二氧化碳、水和无机离子等 的方法。该法只能有效去除染料废水的色度,不能有效去除废水中的COD,处理工艺较复杂。 电化学方法中电化学氧化和电化学还原单位电耗、铁耗大,成本过高,且电极材料的制备过 程复杂;而电凝聚电气浮法对亲水性染料脱色能力差,COD去除效率低,易产生二次污染。 絮凝法对呈溶解态的染料废水去除效果较差,絮凝剂投加量较大,脱色不彻底,产生沉渣二 次污染等问题。好氧法处理印染废水一般要求废水的可生化性较高,对BOD5的去除率一般可 达80%左右。而现代合成染料废水的可生化性一般都较差(BOD/COD<0.2),好氧法难以有 效去除COD和色度。厌氧法既能去除部分有机物,又能降解结构复杂的有机物,提高其可生 化性,对色度的脱除效果显著,但厌氧过程后,染料多被还原为胺类化合物,对微生物的毒 害作用较大,且有机物去除不彻底,出水COD较高。常需将厌氧与好氧联用。但这种联用方 法抗冲击能力差,适应性差,反应时间过长。因此,生物法常需与其它方法配合使用才能有 效处理印染废水,如采用好氧生物接触氧化与铁/炭微电解耦合工艺处理偶氮染料茜素黄、好 氧活性污泥法与O3氧化和化学絮凝工艺联用处理棉纺合成过程废水等。但近年来随着化学纤 维织物的发展、仿真丝的兴起和印染后整理技术的进步,使PVA浆料、人造丝碱解物、新型 助剂等难生化降解的有机物大量进入印染废水,使COD浓度上升到2000~3000mg/L,原有生 物处理系统COD去除率从70%下降到50%左右,甚至更低;而传统的沉淀、气浮法对这类印 染废水的COD去除率仅为30%左右。因此,传统的印染废水处理方法已不能满足印染废水处 理的需要。
与上述其它方法比较,絮凝法工艺简单、处理效率高、特别适于大规模废水处理;当絮 凝剂选择适当,色度和COD去除率高,成本较低,而且不存在降解产物的毒性问题,因此, 在印染废水的处理中获得广泛应用。
采用絮凝法处理印染废水,其关键在于絮凝剂的性能。不仅要求絮凝剂能很好地将溶胶 状和悬浮状的染料颗粒通过电中和和压缩双电层使之脱稳、絮凝而除去,而且要能通过一定 反应使溶解态的染料及其它组分转变成大分子集团通过絮凝而除去。目前,应用于印染废水 处理的絮凝剂可分为无机絮凝剂和有机高分子絮凝剂。无机絮凝剂主要有铝系和铁系两大类, 包括小分子和高分子的铝盐和铁盐,如Al2(SO4)3、AlCl3、聚合氯化铝(PAC)、聚合硫酸铝 (PAS)、FeCl3、FeSO4、聚合硫酸铁(PFS)、聚合氯化硫酸铁(PFCS)等。这些无机絮凝 剂都是依靠本身带有较高正电荷的聚羟阳离子(高分子)或投加后水解产生的简单羟基阳离 子(小分子)的电中和作用使胶体状和悬浮状的染料颗粒脱稳而除去,对分散染料、还原性 染料、直接染料和分子量大的活性染料有较好的去除效果,但对极性基团含量高、水溶性好 的染料,如中性染料和部分活性染料的去除效果差。有机高分子絮凝剂主要有淀粉改性阳离 子絮凝剂、木质素季铵盐絮凝剂、两性壳聚糖和氰胺聚合物阳离子高分子絮凝脱色剂(WH) 等,这些有机高分子絮凝剂对色度的去除率较高,可达90%以上,但对COD的去除率不高, 一般只达50%左右。总之,目前使用的絮凝剂均依赖电中和作用使胶体状和悬浮颗粒脱稳而 去除污染物,缺乏通过与污染成分特别是水溶性成分反应、配合(缔合)使之转化为疏水性 的、胶体状的易被絮凝除去的作用,因此,对污染物的去除效果不佳。目前,鲜有脱色和去 COD及其它污染物俱佳的印染废水处理剂。
钢铁酸洗废水是钢材酸洗工艺中排放的一种含有高浓度Fe2+的强酸性废水,其主要成分是 Fe2+、酸,pH值一般在0.2~1.0。全国每年约有1亿吨钢材要经过酸洗处理才能进入加工工序, 产生1.2亿~2亿吨钢铁酸洗废水。对于酸洗废水的处理,常用的方法有石灰乳中和法、加入铁 屑反应回收亚铁盐、氧化铁红硫铵法和制备聚合铁盐絮凝剂等。这些方法存在以下缺点:石 灰乳中和处理产生的污泥量大,其中的铁和酸浪费;加铁屑回收亚铁盐,回收产品价值不高, 处理过程有废气产生,造成二次污染;制备氧化铁红只回收其中的铁,其中的酸没有得到利 用。相比较而言,以酸洗废水制备聚合铁盐絮凝剂可充分利用其中的铁和酸,是一种较好的 处理方法。
铝型材的生产需对成型铝材进行脱脂、碱蚀、酸洗、氧化、封孔和着色处理,产生大量 的含铝废水,其中还含有少量的Cu2+、Cr3+、Ni2+、Zn2+等重金属离子。对于这种废水的处理 目前都采用碱中和方法,通过控制一定pH值,使其中铝离子和重金属离子转变成氢氧化物沉 淀而从水体中分离,因此,产生了大量的氢氧化铝废渣。我国铝型材产量近千万吨,产生的 氢氧化铝废渣在100万吨以上。目前,对这种废渣还没有切实可行的处理方法,一般都采取填 埋或堆放等方式处置,存在显著的二次污染和安全隐患。
发明内容
针对上述絮凝法处理印染废水,以及钢铁酸废水和铝型材加工产生的氢氧化铝废渣处理 存在的的问题,本发明的目的是提供一种利用钢铁酸洗废水和铝型材加工产生的含铝废渣制 备用于印染废水处理的复合脱色絮凝剂的方法,其特点是:(1)针对染料废水中各成分的结 构特点,根据配位化学原理和絮凝原理,选择能与染料废水中各成分发生反应特别是配位作 用的离子与铁、铝一起共聚;(2)兼具优良的脱色和去COD及其它污染物的性能,并具有优 异的絮凝性能,可通过絮凝一步实现印染废水的达标排放,简化处理工艺和操作,节省处理 设施和投资,降低处理成本。
为实现上述目的,一种用于印染废水处理的复合脱色絮凝剂的制备方法,包括以下步骤:
(1)将酸洗废水、硫酸和含铝废渣按质量比100∶8.6~9.8∶4~6配料,先将酸洗废水和 质量分数为95~98%的硫酸加入到反应器中,然后加入含铝废渣,升温至70~90℃搅拌至溶解, 静置,上清液转入另一个反应器中,再在该反应器中转入下层分离渣后的液体;
(2)按硫酸镁、硫酸、硫酸锌与酸洗废水30~190∶1~20∶1~20∶100的质量比在步骤(1) 所得溶液中加入硫酸镁、硫酸锰和硫酸锌,再加入酸洗废水体积2.8~3.2倍的水,升温至 70~80℃搅拌至固体物质完全溶解;然后按与上述溶液中Fe2+0.085~0.17∶1的物质的量比即 n(氯酸盐):n(Fe2+)=0.085~0.17∶1加入氯酸盐氧化水解0.5~1小时后,按与总铁1.0∶20~30 的物质的量比即n(硅烷偶联剂):n(总铁)=1.0∶20~30缓慢加入硅烷偶联剂,在70~80℃ 下继续反应2~3小时;
(3)降低温度至40~60℃,按与酸洗废水的总铁0.75~1.25∶1的质量比即m(双氰胺- 三乙烯四胺缩聚物):m(酸洗废水的总铁)=0.75~1.25∶1加入双氰胺-三乙烯四胺缩聚物, 搅拌均匀,保温熟化3~4小时,即得粘稠的红色或橙红色印染废水复合脱色絮凝剂。
进一步,步骤(1)中的酸洗废水为钢铁酸洗废水,其主要成分为:总铁浓度为2.45~2.65 mol/L,亚铁浓度为2.25~2.54mol/L,H+浓度为0.95~1.25mol/L。
进一步,步骤(1)中的含铝废渣为铝材加工含铝废渣,即铝材加工过程产生的废水经碱 中和得到的含铝废渣,其主要成分为:氢氧化铝的质量分数为45~55%,Cu2+的质量分数为 0.005~0.01%,Cr3+的质量分数为0.07~0.12%,Ni+的质量分数为0.05~0.08%,Zn2+的质量分数 为0.03~0.05%。
进一步,步骤(1)所述的反应器优选耐酸密闭式反应器。
进一步,步骤(2)所述的硫酸镁、硫酸锰和硫酸锌均为工业级产品,分别为七水硫酸镁、 一水硫酸锰和七水硫酸锌。
进一步,步骤(2)所述的氯酸盐优选氯酸钠或氯酸钾。
进一步,步骤(2)所述的硅烷偶联剂优选γ-氨丙基三乙氧基硅烷、γ-缩水甘油醚氧丙基 三甲氧基硅烷或γ-(甲基丙烯酰氧)丙基三甲氧基硅烷。
进一步,步骤(3)所述的双氰胺-三乙烯四胺缩聚物,单体单元物质的量比为n(双氰 胺)∶n(三乙烯四胺)=2~3∶1。
本发明涉及一种用于印染废水处理的复合脱色絮凝剂的制备方法。采用以钢铁酸洗废水 和铝材加工含铝废渣为基本原料,先用酸洗废水加适量硫酸将含铝废渣溶解,然后根据印染 废水的特点,加入一定比例Mg2+、Zn2+和Mn2+,再加入氯酸盐氧化Fe2+而消耗其中酸,从而 使其中Fe3+、Al3+等离子水解聚合,同时Mg2+、Zn2+和Mn2+等离子也部分参与到Fe3+、Al3+形成的大分子网络中,再通过加入适量的硅烷偶联剂进行水解调聚,最后加入双氰胺-三乙烯 四胺缩聚物,进一步调节絮凝剂的分子形态和聚集体颗粒,生成分子聚集体大、各成分相互 协同作用的印染废水复合脱色絮凝剂技术方案。
相比现有技术,本发明具有如下有益效果:
(1)本发明根据印染废水中污染物的结构特点,有针对性地选择添加与污染物有较强作 用或能有效破坏污染物稳定结构体系的成分,构成了以Fe3+(或Fe2+)、Al3+和Mg2+为主体, Zn2+、Mn2+和双氰胺-三乙烯四胺缩聚物为辅助成分的高效复合脱色絮凝剂。其中各成分可充 分发挥各自的优势并通过协同作用,大大提高了对污染物的去除效果,其中Fe3+和Al3+主要 产生带有较高正电荷的Fe、Al的羟基(氧)聚阳离子,中和、压缩和破坏颗粒(胶粒)的双 电层结构,使之脱稳而絮凝;另外加入的Mg2+、Zn2+、Mn2+、双氰胺-三乙烯四胺缩聚物和原 料中原有的Fe2+、Cr3+、Cu2+等离子则可与废水中染料污染成分的基团发生反应生成水溶性低 的物质,或改变废水体系的电性质,破坏原有稳定结构,促使污染成分发生吸附、络合等反 应,使污染物分子缔合或与之形成大分子络合物,降低染料的亲水性从而使之转为胶体性质 的体系而易于被Fe、Al的羟基(氧)聚阳离子絮凝除去,而这些离子也随絮体一起被去除, 因此,本发明产品对各种印染废水具有优异的脱色、去COD和除浊效果,使用本发明的产品 只需经絮凝一步即可同时实现脱色、去COD和除浊的目的,达到《纺织染整工业水污染物排 放标准》(GB4287-2012)的标准,且简化了处理工艺,降低了处理成本。虽然产品中含有Zn2+、 Mn2+、Cr3+、Cu2+等重金属离子,但由于其参与了脱色絮凝过程,促进了脱色絮凝,一起随絮 体分离出来,因此,不会在处理水中带来新的污染物。
(2)本发明可方便地根据污染物的结构特点来调整复合脱色絮凝剂的组分而生成各种更 具针对性和优良性能的特色絮凝剂,对常见的印染废水都具有优异的脱色絮凝效果,因此, 适用范围广。
(3)本发明通过加入硅烷偶联剂进行调聚,并加入双氰胺-三乙烯四胺缩聚物进一步调 节絮凝剂的分子形态和聚集体颗粒,有效地提高絮凝剂中Fe和Al的活性过渡性低度聚合物 和高聚态的含量,提高了絮凝剂分子聚集体的体积,从而提高了其絮凝性能,一般絮凝过程 中可少加甚至不加助凝剂。
(4)本发明采用加入硅烷偶联剂进行调聚,将含硅基团引入到Fe3+、Al3+的分子网络中, 不仅有利于提高絮凝剂分子聚集体体积,而且在制备过程不易析出含硅沉淀物,产物更稳定, 克服了传统方法通过加入硅酸钠引入硅酸根存在容易析出硅酸沉淀、产物不稳定等缺点。
(5)本发明加入双氰胺-三乙烯四胺缩聚物,不仅能调节絮凝剂的分子形态和聚集体颗 粒,而且其上所带正电荷和丰富的—NH2、—NH—、=N+H2、—CONH2和—OH等可与染料 分子上的活性基团反应、缔合,提高了对接近真溶液状态的难去除污染物的去除效果。
(6)本发明以钢铁酸洗废水和铝材加工含铝废渣为基本原料,大大降低了制造成本,而 且为这两种工业废弃物提供了有效的处理方法和出路,实现其资源化利用,达到了变废为宝 的目的,具有显著的环境、经济和社会效益。
(7)本发明的制备方法,工艺流程简单,操作条件温和,易于控制,而且不需要特殊或 复杂的设备,投资省,便于普及推广和实现工业化,因此,具有广阔的推广应用价值。
(8)本发明的产品适用范围较广,适合于各种印染废水的处理