申请日2017.04.27
公开(公告)日2017.08.18
IPC分类号C04B38/00; C04B33/132
摘要
本发明公开了一种利用污染土壤和工业污泥 制备陶粒的方法,包括如下步骤:(1)将重金属污染土壤筛分后与粉碎筛分处理后的工业污泥混合,加水调节含水率后进行造粒;(2)将造粒后的坯料小球置于回转窑窑尾进行水分烘脱后传送至回转窑主体,坯料小球在600~800℃条件下加热50~80min,完成坯料小球的预热;(3)预热完成后将坯料小球转至高温窑头区间,1300℃~1500℃条件下焙烧10min~60min后卸料冷却。本发明利用现有陶粒焙烧窑设施,通过工艺改进后实现两大类废物的较好的资源化可行性,可同时消纳重金属污染土壤和工业污泥两大类污染物质并可制备获得陶粒。
摘要附图
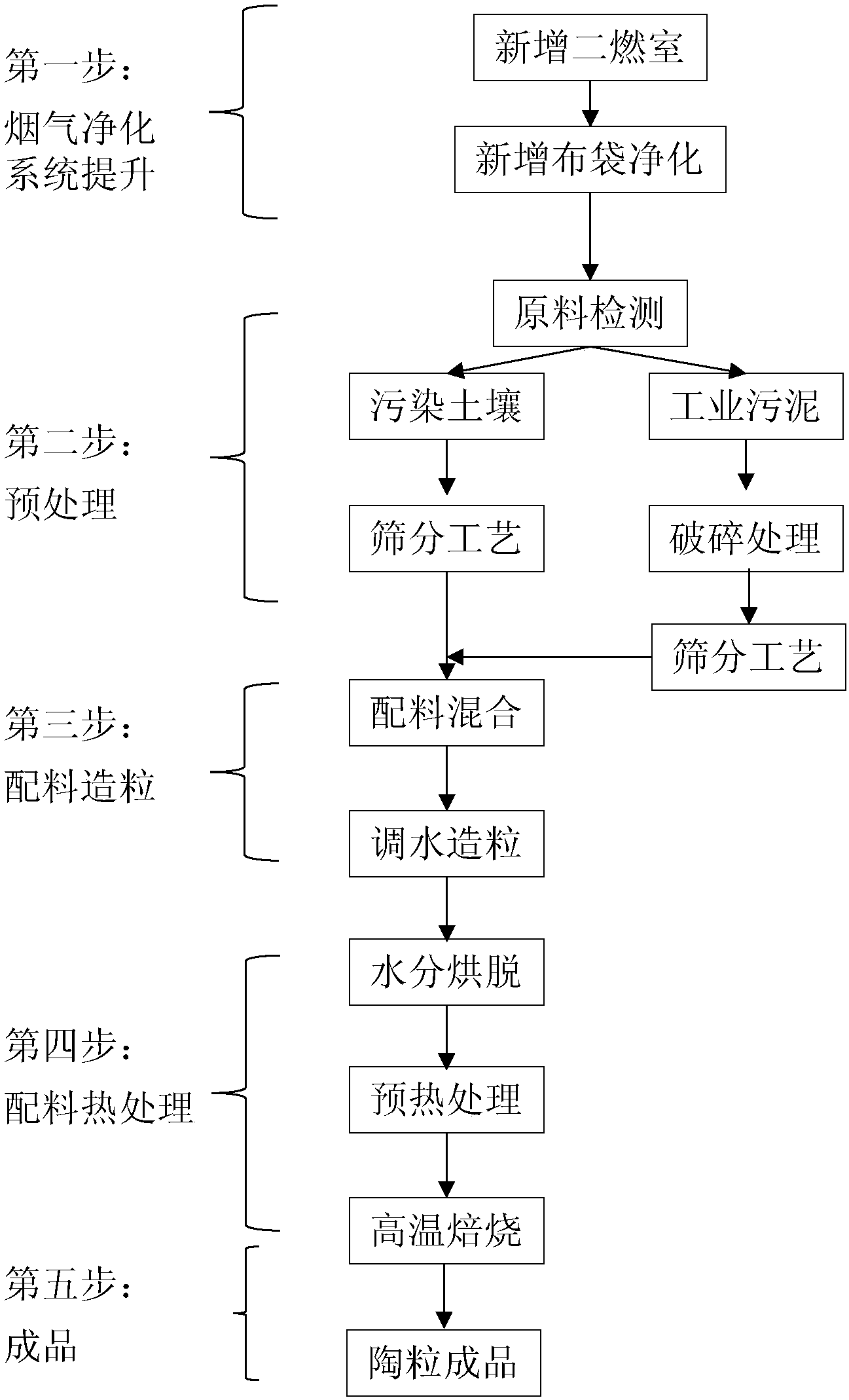
权利要求书
1.一种利用污染土壤和工业污泥制备陶粒的方法,其特征在于,包括如下步骤:
(1)将重金属污染土壤筛分后与粉碎筛分处理后的工业污泥混合,加水调节含水率后进行造粒;
(2)将造粒后的坯料小球置于回转窑窑尾进行水分烘脱后传送至回转窑主体,坯料小球在600~800℃条件下加热50~80min,完成坯料小球的预热;
(3)预热完成后将坯料小球转至高温窑头区间,1300℃~1500℃条件下焙烧10min~60min后卸料冷却。
2.根据权利要求1所述方法,其特征在于,所述重金属污染土壤中的重金属污染物为沸点大于等于400℃的重金属污染物。
3.根据权利要求1所述方法,其特征在于,所述重金属污染土壤中铜浓度控制在10000mg/kg以下,锌浓度控制在10000mg/kg以下,铅浓度控制在1200mg/kg以下,铬浓度控制在2500mg/kg以下,镍浓度控制在300mg/kg以下。
4.根据权利要求1所述方法,其特征在于,所述工业污泥中铜浓度控制在10000mg/kg以下,锌浓度控制在10000mg/kg以下,铅浓度控制在1200mg/kg以下,铬浓度控制在2500mg/kg以下,镍浓度控制在300mg/kg以下;热酌减率40%以上。
5.根据权利要求1所述方法,其特征在于,重金属污染土壤与工业污泥的混合质量比为1:9~9:1。
6.根据权利要求1所述方法,其特征在于,步骤(1)中调节含水率至30%~60%。
7.根据权利要求1所述方法,其特征在于,在所述回转窑窑尾顺次次增设二次燃烧、急冷和布袋除尘设备。
8.根据权利要求7所述方法,其特征在于,二次燃烧温度控制在1000℃~1200℃,烟气停留时间大于2s。
9.一种如权利要求1~8任一权利要求所述方法制备得到的陶粒。
说明书
一种利用污染土壤和工业污泥制备陶粒的方法及制备得到的陶粒
技术领域
本发明属于污染土壤治理和工业固体废物处理利用领域,具体涉及一种利用污染土壤和工业污泥制备陶粒的方法及制备得到的陶粒。
背景技术
我国工业产业经历了长期的粗放型发展,部分企业在此过程中因管理、硬件和技术等不善原因,导致了厂区原址土壤污染问题的发生。随着近年来我国城市产业结构调整加快,大量城市工业企业停产搬迁,数量庞大的退役污染场地问题已经引起了社会的广泛关注。在各种污染场地类型当中,重金属污染场地因数量庞大、重金属污染物种类多、污染程度深、难分解等特性导致了对应土壤修复治理难度较大。
为减少重金属污染场地环境风险,保障人体健康,加快退役场地功能流转,多种修复技术已经投了研究和实际应用。针对重金属污染土壤,当前主要的修复工艺有挖掘填埋、原位固化和化学淋洗等。其中挖掘填埋法对地域内污染物的填埋能力有较大要求,污染土壤封存后其潜在利用价值也被完全浪费;原位固化法通过特定药剂与土壤混合搅拌,利用药剂与重金属的结合能力降低土壤中重金属的释放风险。从实践效果来看,修复效果好差极大取决于现场药剂的混合均匀程度,并且固化后的重金属在酸雨的长期淋溶下仍存在一定释放风险;化学淋洗法主要是通过化学药剂对土壤重金属进行溶解,使重金属去除的一种修复工艺。实质上,即是将重金属从固相介质转移至水相,在工艺实际运行时需面临大量含重金属废水处理问题,且昂贵的药剂费用也成为了此工艺广泛应用、推广的限制性因素。
陶粒是当前应用面广、市场良好的一种轻质原料,可以通过含粘土土壤、城市生活垃圾、粉煤灰、市政污泥等物料经过配比后焙烧制成,相关技术已日趋成熟,已成为部分固体废物消纳的一种新型环保工艺。
然而,目前绝大部分固体废物在进行陶粒制备过程主要以辅料或低比例掺入的形式进行消纳,传统的陶粒焙烧工艺对原料污染物浓度限定要求较高,烟气净化系统能力较弱,面对高浓度、多类别重金属污染土壤和部分高污染工业污泥处理时,陶粒产品的环境安全性、烟气污染的可控性都将成为问题。将重金属污染土壤和部分工业污泥作为陶粒原料,不仅需要保证陶粒内残留重金属的风险可控,同时还要控制工艺过程重金属、二噁英等污染物的释放。
发明内容
针对现有技术存在重金属污染土壤治理能力不足等技术问题,本发明提供一种利用污染土壤和工业污泥制备陶粒的方法,利用现有陶粒焙烧窑设施,通过工艺改进后实现两大类废物的较好的资源化可行性,可同时消纳重金属污染土壤和工业污泥两大类污染物质并可制备获得陶粒。
一种利用污染土壤和工业污泥制备陶粒的方法,包括如下步骤:
(1)将重金属污染土壤筛分后与粉碎筛分处理后的工业污泥混合,加水调节含水率后进行造粒;
本发明对重金属污染土壤进行重金属检测分析,筛选出适宜陶粒制备的重金属污染土壤。
作为优选,所述重金属污染土壤中的重金属污染物为沸点大于等于400℃的重金属污染物。即选择不受沸低于400℃的重金属污染物污染的重金属污染土壤作为陶粒制备原料,例如砷、汞等污染物。
进一步优选,土壤中重金属铜浓度应控制在10000mg/kg以下,锌浓度应控制在10000mg/kg以下,铅浓度应控制在1200mg/kg以下,铬浓度应控制在2500mg/kg以下,镍浓度应控制在300mg/kg以下。
对重金属污染土壤进行筛分处理,通过筛分剔除土堆中石块、水泥块、钢筋等硬度较大的非均质杂物;作为优选,筛分处理设备筛分粒径应控制在0.1mm~3cm;进一步优选,筛分处理设备筛分粒径应控制在0.5mm~1cm;更进一步优选,选择粒径小于5mm的颗粒用于后续工艺。
本发明对工业污泥进行重金属检测分析,筛选粗适宜陶粒制备的工业污泥。作为优选,工业污泥的重金属铜浓度应控制在10000mg/kg以下,锌浓度应控制在10000mg/kg以下,铅浓度应控制在1200mg/kg以下,铬浓度应控制在2500mg/kg以下,镍浓度应控制在300mg/kg以下。进一步优选,选择热酌减率40%以上的工业污泥作为陶粒制备原料,例如可在印染污泥、化工废水生化处理污泥、电镀废水生化处理污泥等工业废水生化工艺污泥中选择。)。
优选地,所述工业污泥优选从印染污泥、化工废水生化处理污泥、电镀废水生化处理污泥等工业废水生化工艺污泥等工业污泥中选择,例如可以选择醋酸废水生化处理后经过板框压滤后的污泥或者板框压滤后的印染污泥。
对工业污泥进行粉碎筛分处理。作为优选,筛分网孔径选择范围为0.1mm~3cm;进一步优选,筛分网孔径应选择在0.5mm~1cm;;更进一步优选,选择粒径小于5mm的颗粒用于后续工艺。
传统利用含重金属固体废物进行陶粒制备的工艺,往往只关注产品的物理强度,规避了原料所带来的环境风险;本发明通过科学配料、水分调配、重金属高温工艺参数设计等方式,较好的降低了重金属的环境活性,明显增加了陶粒对重金属的包裹作用,大大地提高了产品使用过程的环境安全性。此外,由于本发明涉及污染较为严重的原料使用,针对性的提出了烟气强化措施,实现严重二噁英、重金属的有效控制。
针对原料中部分低浓度有机污染物或恶臭类污染物,本发明通过高温焚烧,可实现低浓度组分污染物分解、焚毁;原料中氯元素、硫元素等物质高温过程转化为氯化氢、二氧化硫等,可以在碱液脱硫单元进行有效脱除。
将筛分后的重金属污染土壤与工业污泥按照设定比例进行搅拌混合。作为优选,可按照1:9~9:1的土壤与污泥质量比范围将两者进行混合;进一步优选,可按照2:8~8:2的土壤与污泥质量比范围将两者进行混合。
将混合好的物料进行加水造粒。相比传统造粒,本发明造粒后的胚料小球含水率较高,含水率控制在30%~60%;更进一步优选地,含水率控制在40%。
(2)将造粒后的坯料小球置于回转窑窑尾烘脱后传送至回转窑主体,坯料小球在600~800℃条件下加热50~70min,完成坯料小球的预热;
本发明中直接将坯料小球置于回转炉窑尾进行水分烘脱,作为优选,烘脱温度范围为300℃~600℃。进一步优选,烘托温度范围为400℃~600℃。作为优选,烘托时间为10min~120min;进一步优选,烘脱时间为30min~120min。更进一步优选地,在500℃下烘脱60min或在600℃下烘脱90min。
脱水后的胚料小球进行高温预热处理。作为优选,预热温度范围为300℃~800℃;进一步优选,预热温度范围为600℃~800℃。作为优选,预热时间控制在10min~120min;进一步优选,预热时间为50min~80min。
更进一步优选地,在800℃下预热50min或在700℃下预热30min。
(3)预热完成后将坯料小球转至高温窑头区间,1300℃~1500℃条件下焙烧10min~60min后卸料冷却。
优选地,对高温段的小球按照10℃/min~30℃/min(进一步优选为15℃/min~20℃/min)的升温速率进行加热,直至达到高温焙烧所需温度;高温区停留时间进一步优选为20min~60min(更进一步优选为30~45min);卸料后的冷却方式为自然冷却。
进一步优选,焙烧温度为1350~1450℃,更进一步优选为1400℃。
优选地,在所述回转窑窑尾顺次增设二次燃烧、急冷和布袋除尘设备。
进一步优选地,二次燃烧温度控制在1000℃~1200℃,烟气停留时间大于2s。
一般或典型的陶粒生产工艺配套烟气处理设施的目的主要是去除烟气中的二氧化硫和烟尘。由于本发明涉及部分工业污泥和重金属污染土壤,工艺原料当中的氯离子和重金属含量相比常规固体垃圾和其他陶粒生产原料中的更高,因此烟气重金属捕集、二噁英的控制也是本发明的关注重点。
本发明将重金属污染土壤和工业污泥用于陶粒制备,主要影响参数为重金属污染土壤和工业污泥类型、重金属浓度、原料粒径、原料配比、胚料小球含水率、生料小球脱水温度、高温预热时间、高温焙烧升温速度、高温焙烧目标温度、高温焙烧时长和冷却方式。
其中用于陶粒制备的重金属污染土壤和工业污泥类型不宜选用含有砷、汞等低熔点污染物质;重金属浓度越高,则制备的陶粒其在酸雨淋溶下的重金属释放风险会增高;原料粒径会影响造粒质量(胚料小球的密实度)、原料的混合均匀性;原料配比对陶粒的强度、轻质性有巨大影响:重金属污染土壤比例越高,陶粒强度越大,但轻质性越差,工业污泥掺入比例越高,陶粒强度会有所下降,但陶粒轻质化效果会提升;土壤和污泥的初始含水率对胚料生料小球的质量有显著影响,合适的含水率可通过造粒机获得表面致密且有一定强度的生料小球;胚料小球水分烘脱温度、时长关系到重金属与水分的高温氧化过程,关系胚料小球内沸点600℃以下重金属污染物的去除,也关系到陶粒内部蜂窝孔、发泡以及陶粒表面开裂;高温预热效果不仅关系到生料小球内部部分有机质热解和陶粒的轻质化效果,同时也影响陶粒残留重金属氧化、钝化效果、残留量;高温焙烧升温速度大小影响小球表面熔融对内部气体的包裹效果,过慢的升温速度会导致在小球表面玻璃化熔融速度较慢,从而进一步导致内部气体外溢、形成气孔;高温焙烧目标温度决定了小球表面SiO2的熔融效果、冷却后的陶化效果、陶粒强度、焙烧过程无机物产气效果、重金属污染物的最终钝化和氧化效果;高温焙烧停留时长影响小球表面SiO2的熔融程度和小球内部无机物产气总量,同时也影响了重金属污染物的钝化效果、污染物包裹作用和工艺的能耗高低。
每个工艺步骤都对参数进行严格控制,各步骤参数之间相互协同作用,即使本发明所用原料均为高污染的废弃物,但是本发明方法制备得到陶粒仍然具有重金属残留率低、重金属环境释放风险低、烟气污染风险可控的特点。
一种最优选的制备方法,包括如下步骤:(1)对常规的陶粒窑烟气处理系统进行提升改造:在烟气出口后新增烟气二次燃烧室(二次燃烧温度控制在1000℃~1200℃,烟气停留时间大于2s)。二次燃烧室后配套烟气急冷系统处理、布袋净化处理系统和脱硫处理系统。
(2)对重金属污染土壤进行筛分处理,通过筛分剔除土堆中石块、水泥块、钢筋等硬度较大的非均质杂物;选择粒径5mm以下的污染土壤用于后续工艺;
(3)选择板框压滤后的醋酸污泥用于陶粒制备。将压滤后的块状醋酸污泥进行粉碎处理,选择粒径小于5mm的用于后续工艺;
(4)将重金属污染土壤与醋酸污泥按照土壤与污泥质量比8:2进行混合;
(5)将混合好的物料进行加水造粒。造粒后,胚料小球含水率为40%。
(6)对造粒获得的胚料小球进行水分烘脱处理。烘脱温度设为500℃,烘脱时间定为60min。
(7)对水分烘脱处理后的胚料小球进行高温预热处理。预热温度设为700℃,预热时间设为30min。
(8)将预热后的胚料小球直接转移至陶粒窑高温度段焙烧。调节窑体转速,使得胚料小球逐渐向窑头移动,移动过程胚料小球升温速度设为20℃/min,直至小球移动至温度为1400℃的窑头,随后在该温度下停留15min。
本发明还提供一种如所述方法制备得到的陶粒。
与现有技术相比,本发明具有如下有益效果:
1)本发明利用建材行业数量可观的陶粒窑,通过烟气处理系统能力提升设计、重金属污染土壤与工业污泥的科学配比、陶粒生产参数针对性改动等手段,即可发挥出陶粒窑对重金属污染和工业污泥的资源化处理能力,实现废物资源化的目的。相比单一污染土壤或污泥制备陶粒发明,本发明对污染物的消纳量更大;相比新建工业污泥焚烧设施,本发明投资更少,资源化效果也更突出。
2)相比填埋或化学淋洗工艺,本法具有更显著的污染土壤资源化效果,对设施的建设改造要求也更低;相比固化/稳定化工艺,本法的重金属稳定化效果更佳;
3)本发明法充分基于陶粒窑结构,通过参数物料配比、参数设计,对重金属污染物的环境形态、活性进行了调节。变通过本法制备的陶粒,具有重金属残留率低、重金属环境释放风险低、烟气污染风险可控的特点。