申请日2016.03.21
公开(公告)日2016.06.15
IPC分类号C02F11/10; C02F11/12; C10B53/00; B01D50/00
摘要
本发明涉及一种污泥热解炭化供热系统,包括烟气进料管、旋风除尘器、喷淋处理塔、油水分离器、燃烧器、干化室和炭化室;所述油水分离器包括锥形进口、竖直通道、锥形出口和锥形隔板;所述燃烧器包括燃料排出组件、空气管道、燃烧器壁、引燃器,所述燃料排出组件包括排出端头、燃料提升管和火焰稳定结构;所述火焰稳定结构设置在燃烧器壁的轴线的一侧的第一内侧;本发明克服了重质油和轻质油没有分离、烟气燃烧结构复杂及NOX排放量大的问题,提供一种污泥热解炭化供热系统。
摘要附图
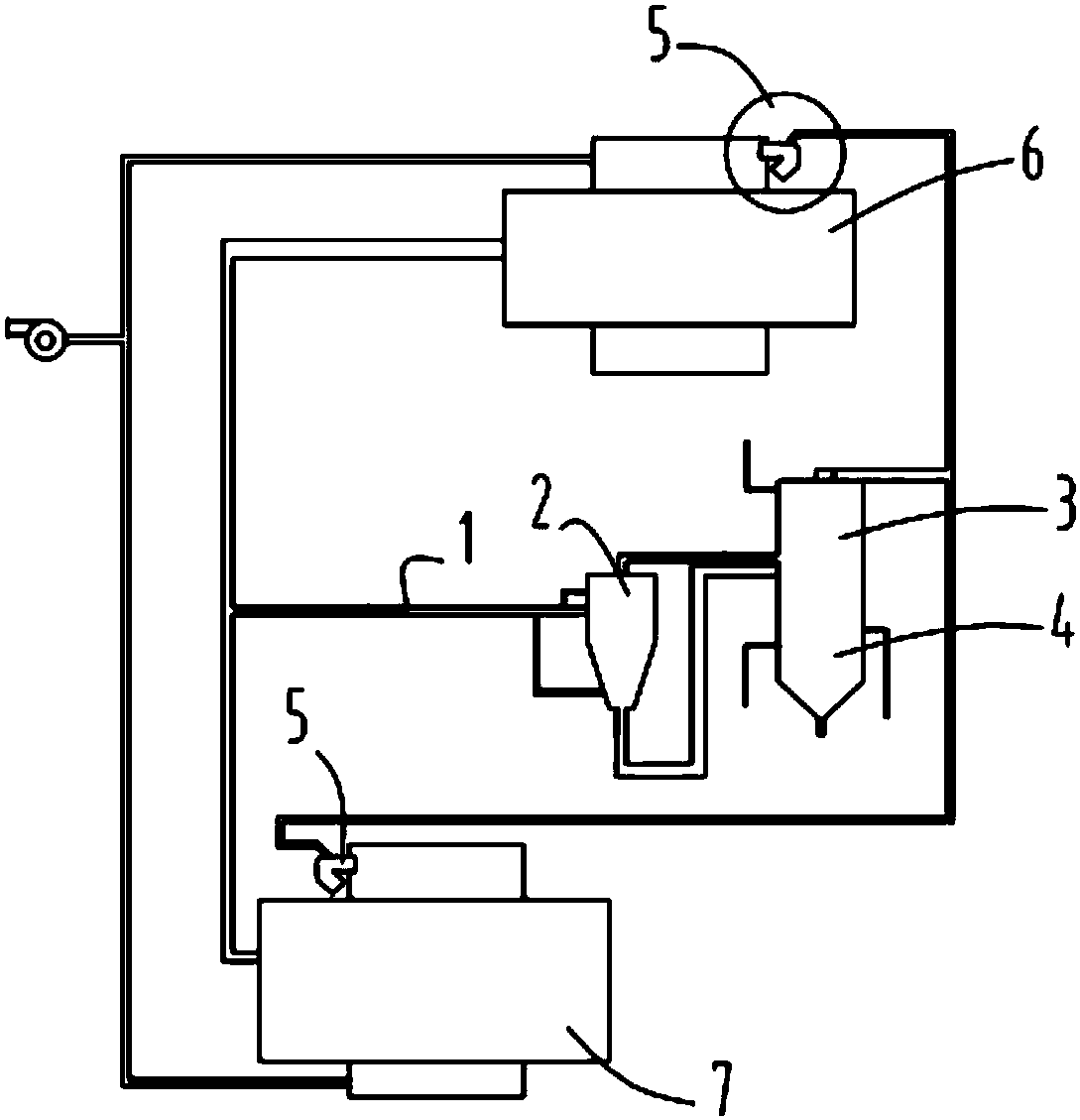
权利要求书
1.一种污泥热解炭化供热系统,包括烟气进料管(1)、旋风除尘器(2)、喷淋处理塔(3)、油水分离器(4)、燃烧器(5)、干化室(6)和炭化室(7);其特征在于,所述干化室(6)与所述炭化室(7)工作过程中产生的一级气相产物经烟气进料管(1)进入旋风除尘器(2)内除尘,后经喷淋处理塔(3)、油水分离器(4)后获得二级气相产物和油分;所述油水分离器(4)设置在喷淋处理塔(3)正下方;所述油水分离器(4)和所述喷淋处理塔(3)的外壁(30)为筒形并同轴设置,气体输送管(21)设置在喷淋处理塔(3)和油水分离器(4)之间;所述油水分离器(4)包括锥形进口(41)、竖直通道(42)、锥形出口(43)和锥形隔板(44),所述锥形进口(41)设置在锥形出口(43)正上方,所述竖直通道(42)上端与锥形进口(41)连通,所述竖直通道(42)下端与锥形出口(43)连通;所述锥形隔板(44)下端连接在所述油水分离器(4)的外壁(30)内侧,所述锥形隔板(44)上端位于锥形进口(41)下端和锥形隔板(44)下端之间;所述锥形隔板(44)与所述竖直通道(42)之间形成环形出口(45);所述燃烧器(5)包括燃料排出组件(51)、空气管道(52)、燃烧器壁(53)、引燃器(54),所述燃料排出组件(51)包括排出端头(511)、燃料提升管(512)和火焰稳定结构(513),所述燃烧器壁(53)环绕的空气通路(55)穿过燃烧器壁(53)延伸;所述燃烧器壁(53)的前端(531)具有空气通路(55)的出口端(532);所述火焰稳定结构(513)设置在燃烧器壁(53)的轴线(533)的一侧的第一内侧(534),所述火焰稳定结构(513)设置在燃烧器壁(53)的出口端(532)处;所述空气管道(52)设置为弯曲状;所述空气管道(52)内设置有导叶(56),导叶(56)延伸穿过燃烧器壁(53)的第二内侧(535)至出口端(532);所述二级气相产物引入所述燃烧器(5)的空气通路(55)内进行燃烧反应并产生高温烟气对干化室(6)、炭化室(7)进行外热式供热。
2.如权利要求1所述的一种污泥热解炭化供热系统,其特征在于:所述油水分离器(4)下端设置有沉降室(4a),所述沉降室(4a)呈倒锥形与油水分离器(4)的外壁(30)连接,所述沉降室(4a)的轴线与油水分离器(4)的轴线重合,所述油水分离器(4)的外壁(30)内侧设置有传感器(4b)。
3.如权利要求2所述的一种污泥热解炭化供热系统,其特征在于:所述油水分离器(4)的外壁(30)上设置有轻质油出口(46)和重质油出口(47),所述轻质油出口(46)位于所述锥形隔板(44)上端和下端之间,所述重质油出口(47)位于锥形隔板(44)下端和沉降室(4a)上端之间;所述沉降室(4a)最下端设置有排渣通道(48)。
4.如权利要求1所述的一种污泥热解炭化供热系统,其特征在于:所述锥形出口(43)内设置有旋转元件(410),所述旋转元件(410)为圆盘形,所述旋转元件(410)的轴线与竖直通道(42)的轴线重合;所述旋转元件(410)位于锥形出口(43)上端和下端之间。
5.如权利要求4所述的一种污泥热解炭化供热系统,其特征在于:所述竖直通道(42)内设置有排气管道(49),所述排气管道(49)上端呈圆弧形向下弯曲;所述排气管道(49)上端开口位于锥形进口(41)上端和下端之间,所述排气管道(49)下端位于竖直通道(42)下端和旋转元件(410)上端之间。
6.如权利要求1所述的一种污泥热解炭化供热系统,其特征在于:所述喷淋处理塔(3)内设置有横篦(31),所述横篦(31)设置在喷淋处理塔(3)外壁(30)内侧上,位于气体输送管(21)之上;所述喷淋处理塔(3)内至少设置有一个喷头(33),所述喷头设置在所述横篦(31)上部;所述横篦(31)上设置有填料层(32),所述填料层(32)上端位于所述喷头(33)之下。
7.如权利要求1所述的一种污泥热解炭化供热系统,其特征在于:所述喷淋处理塔(3)顶端开设有气体通道口(34),所述气体通道口(34)连接气体通道(35),所述气体通道(35)中设置有结露板(36),所述结露板(36)是一种带孔的折线形板块,所述结露板(36)位于气体通道口(34)处。
8.如权利要求1所述的一种污泥热解炭化供热系统,其特征在于:所述环形出口(45)与所述竖直通道(42)同轴线;所述竖直通道(42)的轴线与所述油水分离器(4)的轴线重合。
9.如权利要求1所述的一种污泥热解炭化供热系统,其特征在于:所述旋风除尘器(2)通过气体输送管(21)与喷淋处理塔(3)连接,所述旋风除尘器(2)外表面设置有加热套(20),所述加热套(20)和旋风除尘器(2)之间设置有加热管道(22),所述加热管道(22)进口端与烟气进料管(1)相连接,加热管道(22)出口端与烟气进料管(1)相连接并位于加热管道(22)进口端与烟气进料管(1)相连接点之后。
10.如权利要求3所述的一种污泥热解炭化供热系统,其特征在于:所述传感器(4b)可以是压力传感器,所述压力传感器至少为两个,两个压力传感器位于锥形隔板(44)下端和沉降室(4a)上端之间;两个压力传感器上下垂直设置,分别位于重质油出口(47)的上端之上和重质油出口(47)的下端之下。
说明书
一种污泥热解炭化供热系统
技术领域
本发明涉及一种污泥热解炭化供热系统,尤其涉及一种对含油污泥在热解炭化过程中产生的高温烟气进行处理并循环利用的设备。
背景技术
据统计,我国的采油行业含油污泥的产生量超过百万吨。含油污泥中含有大量石油烃类,如果不进行利用,不仅浪费油气资源,而且因为含水率较高,污泥体积比较大,需要占用大面积的土地进行储存或填埋,易对环境造成污染。国内外针对含油污泥的处理技术有焚烧、生物处理和热解等。含油污泥的热解炭化作为一种较为有效的资源化处理技术渐渐被行业所采用。
2015年8月11日授权公告的申请号为201320497216.4的发明创造公开了一种炼油厂污泥炭化处理及炭化回收装置,其前置处理单元为外热式干燥机1’,该干燥机设置有干燥机夹套2’;其炭化单元为外热式旋转炭化炉3’,旋转炭化炉设置有旋转炭化炉夹套4’;其冷凝和油水分离单元包括烟气收集管路5’、喷淋塔6’、油水分离器7’,烟气收集管路5’将气相产物引入喷淋塔6’,喷淋后得到的炭化液经油水分离器7’后实现油、水分离;其可燃气利用单元包括燃烧室8’,燃烧室8’与干燥机夹套2’、旋转炭化炉夹套4’通过烟气输送管路连通进行供热。
然而,该设备在使用过程中存在以下问题:
(1)在该技术方案中,由于该发明创造收集到的重质油和轻质油没有分离,导致在后续工艺中需要专门的设备进行分离,增加了工时,提高了成本,设备利用率不高。
(2)在该技术方案中,需专门设置燃烧室用于对喷淋水处理后的气体进行燃烧处理,其高温烟气支持干化和炭化。
(3)再者,在该装置中其尾气中含有的NOX较高,需进行后续烟气的净化处理,环保性能不高,特别是当一些重质油成分较高的时候,其气体成分较为复杂,其NOX处理的压力高,燃烧室的温度不易控制,进而NOX产量较多。
发明内容
本发明的目的是针对现有技术的不足之处,克服了重质油和轻质油没有分离、烟气燃烧结构复杂及NOX排放量大的问题,提供一种污泥热解炭化供热系统。
一种污泥热解炭化供热系统,包括烟气进料管、旋风除尘器、喷淋处理塔、油水分离器、燃烧器、干化室和炭化室;所述干化室与所述炭化室工作过程中产生的一级气相产物经烟气进料管进入旋风除尘器内除尘,后经喷淋处理塔、油水分离器后获得二级气相产物和油分;所述油水分离器设置在喷淋处理塔正下方;所述油水分离器和所述喷淋处理塔的外壁为筒形并同轴设置,气体输送管设置在喷淋处理塔和油水分离器之间;所述油水分离器包括锥形进口、竖直通道、锥形出口和锥形隔板,所述锥形进口设置在锥形出口正上方,所述竖直通道上端与锥形进口连通,所述竖直通道下端与锥形出口连通;所述锥形隔板下端连接在所述油水分离器的外壁内侧,所述锥形隔板上端位于锥形进口下端和锥形隔板下端之间;所述锥形隔板与所述竖直通道之间形成环形出口;所述燃烧器包括燃料排出组件、空气管道、燃烧器壁、引燃器,所述燃料排出组件包括排出端头、燃料提升管和火焰稳定结构,所述燃烧器壁环绕的空气通路穿过燃烧器壁延伸;所述燃烧器壁的前端具有空气通路的出口端;所述火焰稳定结构设置在燃烧器壁的轴线的一侧的第一内侧,所述火焰稳定结构设置在燃烧器壁的出口端处;所述空气管道设置为弯曲状;所述空气管道内设置有导叶,导叶延伸穿过燃烧器壁的第二内侧至出口端;所述二级气相产物引入所述燃烧器的空气通路内进行燃烧反应并产生高温烟气对干化室、炭化室进行外热式供热。
作为优选,所述油水分离器下端设置有沉降室,所述沉降室呈倒锥形与油水分离器的外壁连接,所述沉降室的轴线与油水分离器的轴线重合,所述油水分离器的外壁内侧设置有传感器。
作为优选,所述油水分离器的外壁上设置有轻质油出口和重质油出口,所述轻质油出口位于所述锥形隔板上端和下端之间,所述重质油出口位于锥形隔板下端和沉降室上端之间;所述沉降室最下端设置有排渣通道。
作为优选,所述锥形出口内设置有旋转元件,所述旋转元件为圆盘形,所述旋转元件的轴线与竖直通道的轴线重合;所述旋转元件位于锥形出口上端和下端之间。
作为优选,所述竖直通道内设置有排气管道,所述排气管道上端呈圆弧形向下弯曲;所述排气管道上端开口位于锥形进口上端和下端之间,所述排气管道下端位于竖直通道下端和旋转元件上端之间。
作为优选,所述喷淋处理塔内设置有横篦,所述横篦设置在喷淋处理塔外壁内侧上,位于气体输送管之上;所述喷淋处理塔内至少设置有一个喷头,所述喷头设置在所述横篦上部;所述横篦上设置有填料层,所述填料层上端位于所述喷头之下。
作为优选,所述喷淋处理塔顶端开设有气体通道口,所述气体通道口连接气体通道,所述气体通道中设置有结露板,所述结露板是一种带孔的折线形板块,所述结露板位于气体通道口处。
作为优选,所述环形出口与所述竖直通道同轴线;所述竖直通道的轴线与所述油水分离器的轴线重合。
作为优选,所述旋风除尘器通过气体输送管与喷淋处理塔连接,所述旋风除尘器外表面设置有加热套,所述加热套和旋风除尘器之间设置有加热管道,所述加热管道进口端与烟气进料管相连接,加热管道出口端与烟气进料管相连接并位于加热管道进口端与烟气进料管相连接点之后。
作为优选,所述传感器可以是压力传感器,所述压力传感器至少为两个,两个压力传感器位于锥形隔板下端和沉降室上端之间;两个压力传感器上下垂直设置,分别位于重质油出口的上端之上和重质油出口的下端之下。
本发明的有益效果:
(1)本发明巧妙地将喷淋处理塔和油水分离器合二为一,将喷淋处理后获得的油分直接进行分层,油水分离器中重质油出口和轻质油出口分开设置,使得重质油和轻质油在分离阶段可以直接分开,避免了后续工艺的分离过程,而且喷淋处理塔、油水分离器、沉降室和锥形隔板同轴线,保证了喷淋处理塔和油水分离器运转的稳定性。
(2)本发明利用旋风除尘器、喷淋处理塔将干化和热解炭化过程中产生的气相产物进行喷淋液化处理,分离后的气相产物直接通入燃烧器中进行燃烧并获得高温烟气直接对干化或炭化进行供热;在此过程中,因利用本技术方案其气相产物能够直接与本燃烧器进行配合使用,且其能够有效协助本燃烧器有效降低燃烧过程中产生的NOX;简化了本装置的结构,同时环保性能更强。
(3)本发明油水分离器的锥形出口内设置的旋转元件可以在对油水分离器内的液体进行搅拌,在加速重质油和轻质油分离的同时,旋转元件旋转时还可以达到这样一种预料不到的效果:即,旋转元件旋转时,旋转元件上部可形成低压区方便竖直通道内的液体向下流动;另外,旋转元件旋转时还可以对旋转元件下部液体施加压力,迫使锥形出口下方的液体向油水分离器四周流动,使其中的重质油和轻质油向上浮起,避免部分重质油和轻质油滞留在锥形出口附近难以排出。
(4)本发明的竖直通道内设置有排气管道,避免锥形出口内聚集空气,阻碍竖直通道内液体向下流动。
(5)本发明利用一级气相产物自身的热量对旋风除尘器进行加热,使得旋风除尘器与烟气接触面的表面温度高于烟气露点温度,避免接触面上漏点腐蚀现象的产生;同时本发明为防止露点腐蚀所采取的的加热措施其热量来自一级气相产物本身,节能环保。
(6)本发明先通过旋风除尘器进行单独的除尘处理又通过喷淋处理塔内的喷头进行了喷淋处理,而喷淋处理本身又有着除尘的作用。所以,本发明实际进行了一次喷淋,两次除尘,而粉尘上是极易附着大量重质油和轻质油成分的,两次除尘相当于进一步除去烟气中的重质油和轻质油成分,从而更彻底的除去烟气中的重质油和轻质油成分,同时粉尘本身也得以更为彻底的清除。
(7)本发明利用烟气本身的温度对旋风除尘器进行加热还有一个预料不到的优点:加热后烟气本身的温度有所降低,温度降低后气体粘度降低,粘度降低可以提高旋风除尘器的沉降速度,提高旋风除尘器的除尘效率。
(8)本发明采用的填料层使得上升的气体与下降的喷淋液体的接触时间更长,接触更加充分,气体中重质油和轻质油成分的冷凝过程进行的更加充分,重质油和轻质油的分离更为彻底。
(9)本发明提供的燃烧装置偏心非对称的设置克服了现有的燃烧器供热炉膛内温度过高导致较多NOx的生成的问题,使燃料燃烧充分又能控制温度,降低NOx的生成;空气管道设计成弯曲形状使空气流经弯曲的管道时产生流速差,不仅配合了本发明降低NOx生成的目的还达到了减小设备占用空间的目的;烟气最终得以燃烧,防止最终气体内仍然含有有害成分对环境造成危害,本发明不需要专门的燃烧室,简化了设备;而且本发明还有一个难以预料的效果,将从喷淋处理塔出来的气体通入燃烧器的空气通路,可以利用该气体的余热对空气进行预热,同时由于该气体内氧含量极低,可以在燃烧时起到类似惰性气体的作用,进一步降低NOx的生成。