申请日2017.11.08
公开(公告)日2018.03.13
IPC分类号C02F9/06
摘要
本发明属于废水处理技术领域,尤其涉及一种含油废水的处理工艺及处理系统,包括以下步骤:A、将含油废水通过格栅井,再排入隔油池中;B、将隔油池中分离出的废水送入电气浮装置中;C、将电气浮装置中处理后的含油废水送入臭氧池中,得到氧化分解水;D、在氧化分解水中加入过硫酸钠与铁粉;E、在含油废水中加入破乳剂,再加入絮凝剂;F、将含油废水经过微滤膜过滤装置过滤,过滤后排入收集池中;本发明废水处理工艺使含油废水中的油和水进行有效分离,有机物得到有效降解,油水分离效果可达90%以上,COD去除率达60‑80%,本发明提供的含油废水处理系统可有效降低含油污泥的处理成本,符合国家排水标准。
摘要附图
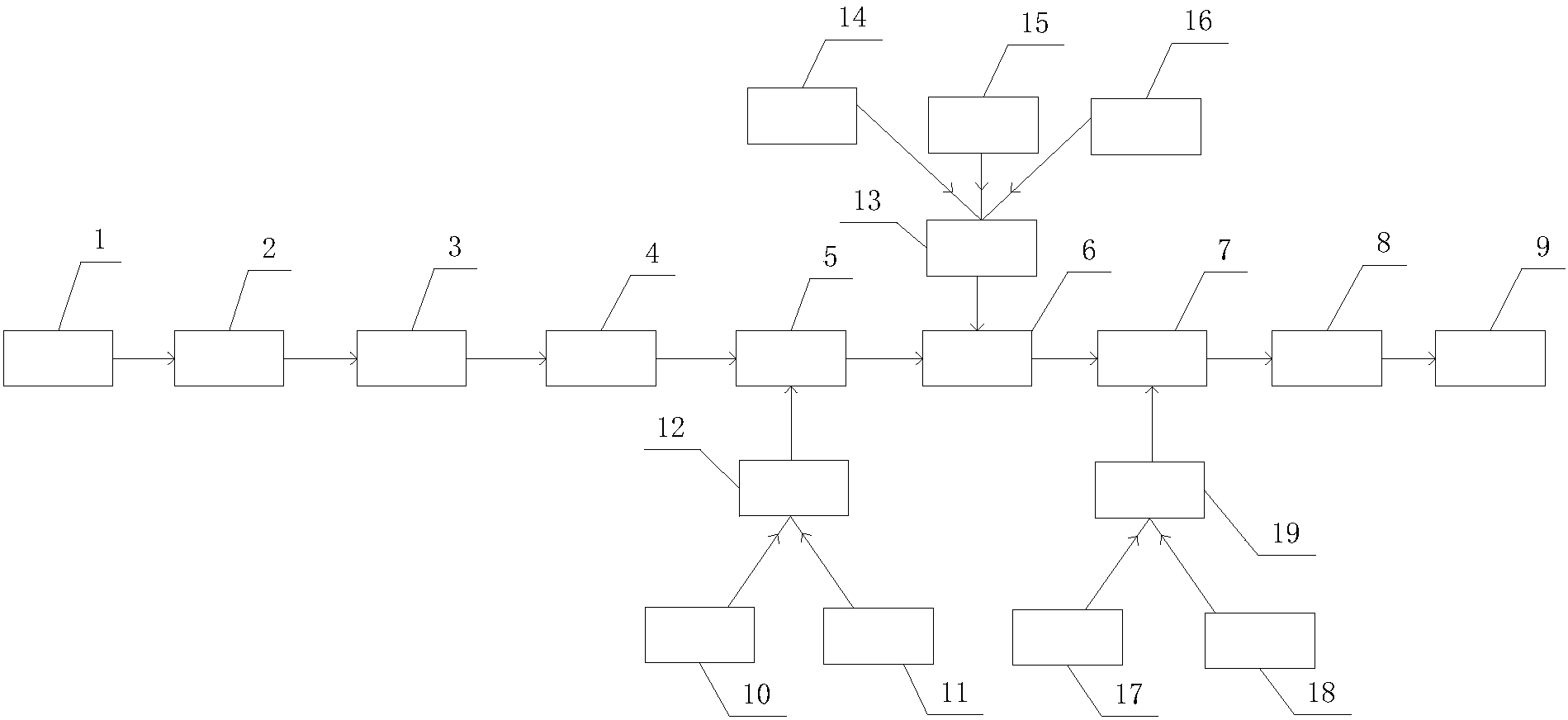
权利要求书
1.一种含油废水的处理工艺,其特征在于,包括以下步骤:
A、将含油废水通过格栅井(1),再排入隔油池(2)中,使含油废水中的悬浮物进行有效的分离;
B、将隔油池(2)中分离出的悬浮物排出,同时分离出的废水送入电气浮装置(3)中,使废水与油初步分离;
C、将电气浮装置(3)中处理后的含油废水送入臭氧池(4)中,含油废水中的有机物在臭氧池(4)中得到分解,得到氧化分解水;
D、在步骤C中处理得到的氧化分解水中加入过硫酸钠与铁粉,并调节PH值为2-3的条件下反应5-8h;
E、在40-60℃温度条件下,在步骤D处理得到的含油废水中加入破乳剂进行破乳处理,使残油与水进行分离,再加入絮凝剂进行沉降处理;
F、将步骤E中沉降处理得到的含油废水经过微滤膜过滤装置(8)过滤,过滤后排入收集池(9)中。
2.根据权利要求1所述一种含油废水的处理工艺,其特征在于,在步骤D中,所述过硫酸钠的加入量为130-200mg/L,所述铁粉的加入量为30-40mg/L。
3.根据权利要求1所述一种含油废水的处理工艺,其特征在于,在步骤D中,所述反应温度控制在30-40℃。
4.根据权利要求1所述一种含油废水的处理工艺,其特征在于,在步骤E中,所述破乳剂通过以下反应步骤制得:在丙二醇溶液体系中加入硅氧烷、聚乙二醇醚与扩链剂,并在60-100℃温度条件下反应5-8h,即得破乳剂。
5.根据权利要求4所述一种含油废水的处理工艺,其特征在于,所述硅氧烷、聚乙二醇醚与扩链剂的摩尔比为1:1.3:2。
6.根据权利要求4或5所述一种含油废水的处理工艺,其特征在于,所述扩链剂为1,4一丁二醇、1,6一己二醇、三羟甲基丙烷、新戊二醇与山梨醇中的一种或几种的混合物。
7.根据权利要求1所述一种含油废水的处理工艺,其特征在于,在步骤E中,所述絮凝剂通过在200-300℃温度条件下,壳聚糖与聚乙二醇按摩尔比1:1.3混合反应3-4h制得。
8.一种含油废水的处理系统,其特征在于,包括格栅井(1)、隔油池(2)、电气浮装置(3)、臭氧池(4)、第一处理池(5)、第二处理池(6)、第三处理池(7)、第一投料罐(10)、第二投料罐(11)、第一反应罐(12)、第三投料罐(14)、第四投料罐(15)、第五投料罐(16)、第二反应罐(13)、第六投料罐(17)、第七投料罐(18)、第三反应罐(19)、微滤膜过滤装置(8)与收集池(9);
所述格栅井(1)的出水口与所述隔油池(2)的进水口通过管道相连通,所述隔油池(2)的出水口与所述电气浮装置(3)的进水口通过管道相连通,所述电气浮装置(3)的出水口与所述臭氧池(4)的进水口通过管道相连通,所述臭氧池(4)的出水口与所述第一处理池(5)的进水口通过管道相连通,所述第一处理池(5)的出水口与所述第二处理池(6)的进水口通过管道相连通,所述第二处理池(6)的出水口与所述第三处理池(7)的进水口通过管道连通,所述第三处理池(7)的出水口与所述微滤膜过滤装置(8)的进水口通过管道相连通,所述微滤膜过滤装置(8)的出水口与所述集水池(9)的进水口通过管道相连通;
所述第一投料罐(10)的出料口与所述第二投料罐(11)的出料口分别通过管道与所述第一反应罐(12)的进料口相连通,所述第一处理池(5)设有第一加药口,所述第一反应罐(12)的出料口与所述第一加药口通过管道连通;
所述第三投料罐(14)的出料口、第四投料罐(15)的出料口与第五投料罐(16)的出料口分别通过管道与所述第二反应罐(13)的进料口相连通,所述第二处理池(6)设有第二加药口,所述第二反应罐(13)的出料口与所述第二加药口通过管道连通;
所述第六投料罐(17)的出料口与所述第七投料罐(18)的出料口分别通过管道与所述第三反应罐(19)的进料口相连通,所述第三处理池(7)设有第三加药口,所述第三反应罐(19)的出料口与所述第三加药口通过管道连通。
9.根据权利要求8所述一种含油废水的处理系统,其特征在于,所述第一反应罐(12)、第二反应罐(13)与第三反应罐(19)内均设有搅拌装置。
10.根据权利要求8所述一种含油废水的处理系统,其特征在于,全部所述管道上均设有调节阀门。
说明书
一种含油废水的处理工艺及处理系统
技术领域
本发明属于废水处理技术领域,尤其涉及一种含油废水的处理工艺及处理系统。
背景技术
含油废水主要来源为含油雨水和清洗油库、加油机、场地等产生的含油污水,存在水量具有水量变化大、排放不连续等特点。可生化性较差,传统的处理工艺有:如物理法(沉降、机械、离心、粗粒化、过滤、膜分离等);物理化学法(浮选、吸附、离子交换等);化学法(凝聚、酸化、盐析、电解等);生物化学法(活性污泥、生物滤池、氧化塘等),其传统的絮凝沉淀、气浮隔离方法不仅加药量大运行成本高,而且造成二次污染,产生大量含油污泥,属于危险废弃物,处理费用昂贵;吸附、过滤等方法也需要人工频繁清理,管理不便,也同样有处理污泥的难题,难以达到国家排放标准。
发明内容
本发明为了解决上述技术问题提供一种含油废水的处理工艺及处理系统,可有效的处理含油废水,其成本低、处理效率高,符合国家排放标准。
本发明解决上述技术问题的技术方案如下:
一种含油废水的处理工艺,包括以下步骤:
A、将含油废水通过格栅井,再排入隔油池中,使含油废水中的悬浮物进行有效的分离;
B、将隔油池中分离出的悬浮物排出,同时分离出的废水送入电气浮装置中,使废水与油初步分离;
C、将电气浮装置中处理后的含油废水送入臭氧池中,含油废水中的有机物在臭氧池中得到分解,得到氧化分解水;
D、在步骤C中处理得到的氧化分解水中加入过硫酸钠与铁粉,并调节PH值为2-3的条件下反应5-8h;
E、在40-60℃温度条件下,在步骤D处理得到的含油废水中加入破乳剂进行破乳处理,使残油与水进行分离,再加入絮凝剂进行沉降处理;
F、将步骤E中沉降处理得到的含油废水经过微滤膜过滤装置过滤,过滤后排入收集池中。
作为本发明进一步优选,在步骤D中,所述过硫酸钠的加入量为130-200mg/L,所述铁粉的加入量为30-40mg/L。
作为本发明进一步优选,在步骤D中,所述反应温度控制在30-40℃。
作为本发明进一步优选,在步骤E中,所述破乳剂通过以下反应步骤制得:在丙二醇溶液体系中加入硅氧烷、聚乙二醇醚与扩链剂,并在60-100℃温度条件下反应5-8h,即得破乳剂。
作为本发明进一步优选,所述硅氧烷、聚乙二醇醚与扩链剂的摩尔比为1:1.3:2。
作为本发明进一步优选,所述扩链剂为1,4一丁二醇、1,6一己二醇、三羟甲基丙烷、新戊二醇与山梨醇中的一种或几种的混合物。
作为本发明进一步优选,在步骤E中,所述絮凝剂通过在200-300℃温度条件下,壳聚糖与聚乙二醇按摩尔比1:1.3混合反应3-4h制得。
本发明还提供一种含油废水的处理系统,包括格栅井、隔油池、电气浮装置、臭氧池、第一处理池、第二处理池、第三处理池、第一投料罐、第二投料罐、第一反应罐、第三投料罐、第四投料罐、第五投料罐、第二反应罐、第六投料罐、第七投料罐、第三反应罐、微滤膜过滤装置与收集池;
所述格栅井的出水口与所述隔油池的进水口通过管道相连通,所述隔油池的出水口与所述电气浮装置的进水口通过管道相连通,所述电气浮装置的出水口与所述臭氧池的进水口通过管道相连通,所述臭氧池的出水口与所述第一处理池的进水口通过管道相连通,所述第一处理池的出水口与所述第二处理池的进水口通过管道相连通,所述第二处理池的出水口与所述第三处理池的进水口通过管道连通,所述第三处理池的出水口与所述微滤膜过滤装置的进水口通过管道相连通,所述微滤膜过滤装置的出水口与所述集水池的进水口通过管道相连通;
所述第一投料罐的出料口与所述第二投料罐的出料口分别通过管道与所述第一反应罐的进料口相连通,所述第一处理池设有第一加药口,所述第一反应罐的出料口与所述第一加药口通过管道连通;
所述第三投料罐的出料口、第四投料罐的出料口与第五投料罐的出料口分别通过管道与所述第二反应罐的进料口相连通,所述第二处理池设有第二加药口,所述第二反应罐的出料口与所述第二加药口通过管道连通;
所述第六投料罐的出料口与所述第七投料罐的出料口分别通过管道与所述第三反应罐的进料口相连通,所述第三处理池设有第三加药口,所述第三反应罐的出料口与所述第三加药口通过管道连通。
作为本发明进一步优选,所述第一反应罐、第二反应罐与第三反应罐内均设有搅拌装置。
作为本发明进一步优选,全部所述管道上均设有调节阀门。
本发明的有益效果是:本发明废水处理工艺使含油废水中的油和水进行有效分离,有机物得到有效降解,油水分离效果可达90%以上,COD去除率达60-80%,本发明提供的含油废水处理系统可有效降低含油污泥的处理成本,符合国家排水标准。