申请日2015.09.14
公开(公告)日2017.03.22
IPC分类号C02F9/04
摘要
本发明提供了一种不锈钢稀油生化污水处理系统,其包括进水池、高炉渣吸附罐、中间水池、斜板沉淀池,所述斜板沉淀池包括混合区、沉淀区、排泥管和出水泵,所述进水池与高炉渣吸附罐通过一级提升泵连通,所述高炉渣吸附罐与中间水池通过管路连通,所述中间水池与斜板沉淀池通过二级提升泵连通。本发明首次提出了完整的不锈钢稀油生化出水达标处理技术方案,系统解决了不锈钢稀油生化出水排放引起的污染环境问题,经过本技术方案处理后不锈钢稀油生化出水可达标排放,也可以重新回用与生产系统,循环利用了水资源。
摘要附图
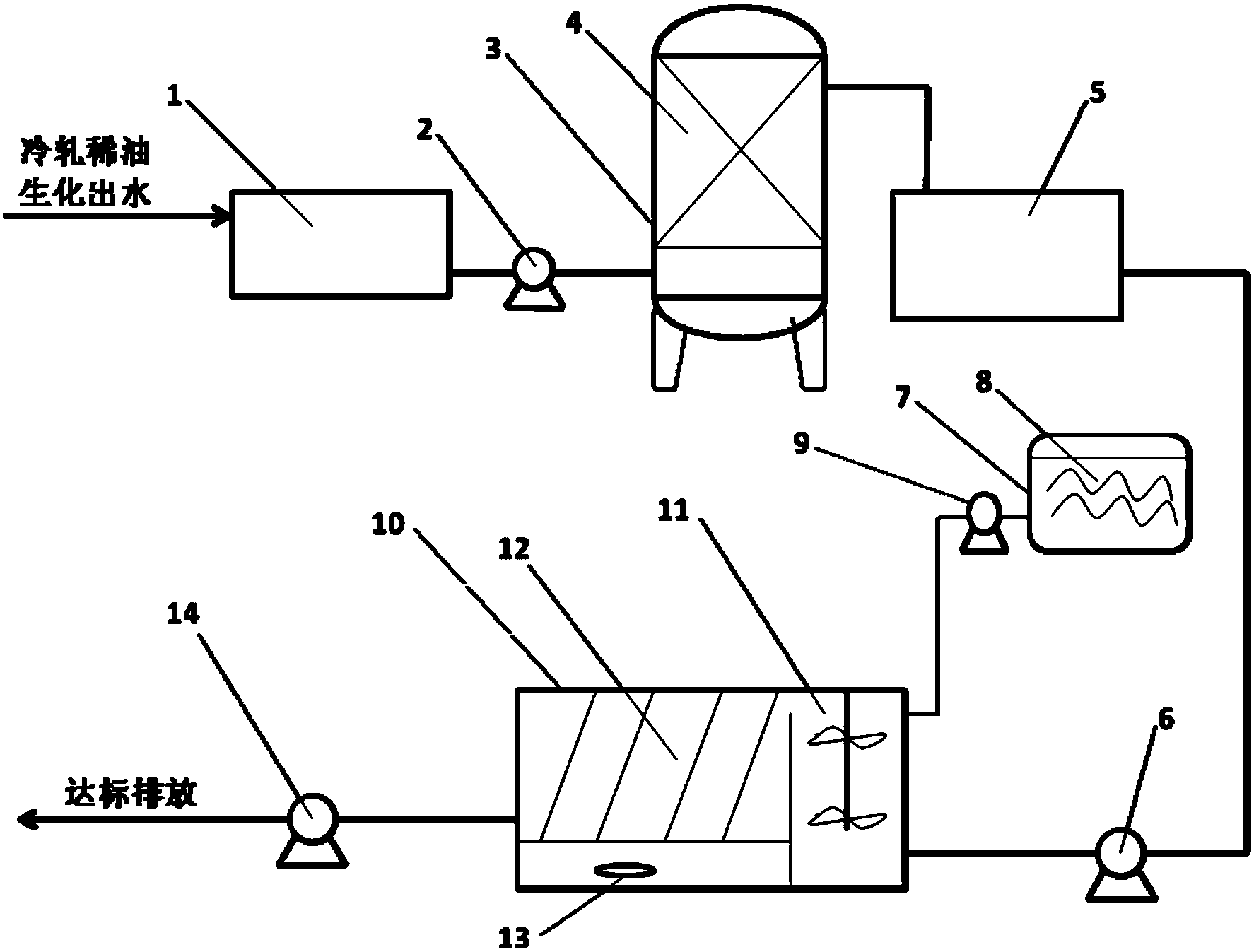
权利要求书
1.一种不锈钢稀油生化污水处理系统,其特征在于,包括进水池、高炉渣吸附罐、中间水池、斜板沉淀池,所述斜板沉淀池包括混合区、沉淀区、排泥管和出水泵,所述进水池与高炉渣吸附罐通过一级提升泵连通,所述高炉渣吸附罐与中间水池通过管路连通,所述中间水池与斜板沉淀池通过二级提升泵连通。
2.如权利要求1所述的不锈钢稀油生化污水处理系统,其特征在于,所述高炉渣吸附罐的高度和直径比为5:1,且高炉渣吸附罐内填装有改性高炉渣混合填料,所述改性高炉渣混合填料的体积为高炉渣吸附罐体积的70~85%。
3.如权利要求2所述的不锈钢稀油生化污水处理系统,其特征在于,所述改性高炉渣混合填料的制备方法包括如下步骤:
将75~87wt%高炉渣的进行预处理后,与10~15wt%陶瓷颗粒、3~12wt%粘土粘结剂混合均匀,以5℃/min的速率升温至1250℃,恒温60~180min后,自然冷却,得到改性高炉渣混合填料,
其中,所述高炉渣的预处理的预处理方法为:将高炉渣先用热碱液浸泡以除去油渍,然后再用盐酸浸泡以除去表面氧化物,最后用纯水洗净。
4.如权利要求3所述的不锈钢稀油生化污水处理系统,其特征在于,所述高炉渣中包含有按重量百分数计的如下组分:
SiO2:21~42%;CaO:26~38%;MgO:6~12%;Al2O3:12~18%;FeO:0.5~1.5%;Fe2O3:0.5~2%;K2O:0.3~0.9%;
所述陶瓷颗粒包含有按重量百分数计的如下组分:SiO2:55~71%;Al2O3:21~29%;Fe2O3:4~9%;CaO:1~7%。
5.一种如权利要求1所述的不锈钢稀油生化污水处理系统的使用方法,其特征在于,包括如下步骤:
将不锈钢稀油生化污水排至进水池;
利用一级提升泵将所述进水池内的不锈钢稀油生化污水抽入高炉渣吸附罐内,以8~12m/s的流速进行6~9min的反冲洗,反冲洗周期240~360小时,直至所述不锈钢稀油生化污水的水质特征:
pH为6~9,悬浮物为17~41mg/L,镍为0.01~0.05mg/L,COD为51~92mg/L;
将经高炉渣吸附罐处理后的不锈钢稀油生化污水通过管路自流入中间水池中后,通过二级提升泵抽至斜板沉淀池内,在所述斜板沉淀池的混合区中与复配水处理混凝剂充分混合反应后,产物排向斜板沉淀池的沉淀区,分离出污泥和达标废水,所述达废水的水质特征为:
PH为6~9,悬浮物为10~21mg/L,镍离子为0.01~0.05mg/L,COD为13~28mg/L。
6.如权利要求1所述的不锈钢稀油生化污水处理系统的使用方法,其特征在于,所述不锈钢稀油生化废水在进入进水池前的水质特征为:
PH为6~9,悬浮物为100~210mg/L,镍离子为0.1~0.3mg/L,COD为63~111mg/L。
7.如权利要求1所述的不锈钢稀油生化污水处理系统的使用方法,其特征在于,所述复配水处理混凝剂由吸附剂和絮凝剂组成。
8.如权利要求7所述的不锈钢稀油生化污水处理系统的使用方法,其特征在于,所述复配水处理混凝剂的制备方法为:
筛取粒径为0.12~0.17mm的活性炭粉和粒径为0.1~0.5mm的N,O-羧甲基壳聚糖作为吸附剂,同时配制质量分数为17~25的聚硅硫酸铝水溶液作为絮凝剂;
将所述活性炭粉和N,O-羧甲基壳聚糖按照(30~50):1的质量比混合后,向所述聚硅硫酸铝水溶液中投加,控制总投加量为每升聚硅硫酸铝溶液投500g活性炭粉和N,O-羧甲基壳聚糖的混合物;
分散均匀后,在650W的微波功率下,辐射10~15min后,在65℃的水浴下搅拌150~180min,冷却后得到复配水处理混凝剂。
说明书
不锈钢稀油生化污水处理系统及其使用方法
技术领域
本发明属于水处理技术领域,具体涉及一种不锈钢稀油生化出水的达标处理工艺。
背景技术
钢铁工业是一个高能耗、高资源、高污染的产业,其水资源消耗巨大,约占全国工业用水量的14%。
2005年7月国家对钢铁工业发展循环经济、节约能源和资源、走可持续发展道路提出了更高的目标和更具体的要求,在全球资源紧缺的情况下,低能耗、低污染、低排放成为社会发展的需要。
我国钢铁企业的单位耗用水量仍高于国外先进钢铁企业的水平,近一步降低钢铁企业吨钢耗用新水量,提高钢铁企业水的循环利用率,加强钢铁企业废水的综合处理与回用是我国钢铁企业实现可持续发展的关键之一。
不锈钢稀油废水为不锈钢生产工艺产生的含油废水,经过生化处理后,废水中有机物及重金属仍然不能够达标排放。因此,加大对不锈钢稀油生化出水的研究力度,制定具有针对性的处理方案,探索不锈钢稀油生化出水低成本达标排放技术,对实现企业的可持续发展和节能减排具有重要意义。
到目前为止,还没有针对不锈钢稀油生化出水达标排放的处理工艺。本发明的目的就是根据不锈钢稀油废水生化出水的水质水量情况,开发出经济、高效的达标排放工艺。开发不锈钢稀油生化出水的达标排放的处理工艺,以循环利用节能减排为主要任务,减少环境污染,积极应对日益严格的环境保护法规。
发明内容
本发明首次提出了完整的不锈钢稀油生化出水达标排放的技术方案,系统解决了不锈钢稀油生化出水污染环境的问题,经过本技术方案处理后不锈钢稀油生化出水可达标排放,也可以应用于钢铁工业领域的生产系统。
本发明是通过以下技术方案实现的:
一种不锈钢稀油生化污水处理系统,其包括进水池、高炉渣吸附罐、中间水池、斜板沉淀池,所述斜板沉淀池包括混合区、沉淀区、排泥管和出水泵,所述进水池与高炉渣吸附罐通过一级提升泵连通,所述高炉渣吸附罐与中间水池通过管路连通,所述中间水池与斜板沉淀池通过二级提升泵连通。
作为优选方案,所述高炉渣吸附罐的高度和直径比为5:1,且高炉渣吸附罐内填装有改性高炉渣混合填料,所述改性高炉渣混合填料的体积为高炉渣吸附罐体积的70~85%。
作为优选方案,所述改性高炉渣混合填料的制备方法包括如下步骤:
将75~87wt%高炉渣的进行预处理后,与10~15wt%陶瓷颗粒、3~12wt%粘土粘结剂混合均匀,以5℃/min的速率升温至1250℃,恒温60~180min后,自然冷却,得到改性高炉渣混合填料,
其中,所述高炉渣的预处理的预处理方法为:将高炉渣先用热碱液浸泡以除去油渍,然后再用盐酸浸泡以除去表面氧化物,最后用纯水洗净。
作为优选方案,所述高炉渣中包含有按重量百分数计的如下组分:
SiO2:21~42%;CaO:26~38%;MgO:6~12%;Al2O3:12~18%;FeO:0.5~1.5%;Fe2O3:0.5~2%;K2O:0.3~0.9%;
所述陶瓷颗粒包含有按重量百分数计的如下组分:SiO2:55~71%;Al2O3:21~29%;Fe2O3:4~9%;CaO:1~7%。
一种如本发明所述的不锈钢稀油生化污水处理系统的使用方法,其包括如下步骤:
将不锈钢稀油生化污水排至进水池;
利用一级提升泵将所述进水池内的不锈钢稀油生化污水抽入高炉渣吸附罐内,以8~12m/s的流速进行6~9min的反冲洗,反冲洗周期240~360小时,直至所述不锈钢稀油生化污水的水质特征:
pH为6~9,悬浮物为17~41mg/L,镍为0.01~0.05mg/L,COD为51~92mg/L;
将经高炉渣吸附罐处理后的不锈钢稀油生化污水通过管路自流入中间水池中后,通过二级提升泵抽至斜板沉淀池内,在所述斜板沉淀池的混合区中与复配水处理混凝剂充分混合反应后,产物排向斜板沉淀池的沉淀区,分离出污泥和达标废水,所述达废水的水质特征为:
PH为6~9,悬浮物为10~21mg/L,镍离子为0.01~0.05mg/L,COD为13~28mg/L。
作为优选方案,所述不锈钢稀油生化废水在进入进水池前的水质特征为:
PH为6~9,悬浮物为100~210mg/L,镍离子为0.1~0.3mg/L,COD为63~111mg/L。
作为优选方案,所述复配水处理混凝剂由吸附剂和絮凝剂组成。
作为优选方案,所述复配水处理混凝剂的制备方法为:
筛取粒径为0.12~0.17mm的活性炭粉和粒径为0.1~0.5mm的N,O-羧甲基壳聚糖作为吸附剂,同时配制质量分数为17~25的聚硅硫酸铝水溶液作为絮凝剂;
将所述活性炭粉和N,O-羧甲基壳聚糖按照(30~50):1的质量比混合后,向所述聚硅硫酸铝水溶液中投加,控制总投加量为每升聚硅硫酸铝溶液投500g活性炭粉和N,O-羧甲基壳聚糖的混合物;
分散均匀后,在650W的微波功率下,辐射10~15min后,在65℃的水浴下搅拌150~180min,冷却后得到复配水处理混凝剂。
与现有技术相比,本发明具有如下的有益效果:
1、首次提出了完整的不锈钢稀油生化出水达标处理技术方案,系统解决了不锈钢稀油生化出水排放引起的污染环境问题,经过本技术方案处理后不锈钢稀油生化出水可达标排放,也可以重新回用与生产系统,循环利用了水资源;
2、采用本发明的不锈钢稀油生化出水达标排放技术方案,处理效果稳定,生产运行成本低,操作运行简便,自动化程度高;
3、属于环境友好型的钢铁绿色生产系统。