申请日2015.10.30
公开(公告)日2016.03.23
IPC分类号B01D21/02; B01D21/24; C02F1/40; C02F1/52; C02F9/04; C02F1/38
摘要
本实用新型公开了沉降除油罐及采出水处理系统,沉降除油罐包括罐体,罐体内设有中心管柱、配水室、集油槽和设于罐体底部排泥装置;中心管柱设于罐体内并至少下端密封,中心管柱的上部连通有第一出水管,下部连通有多个集水管路,集水管路上设有入水口;配水室连接有多个配水管路和第一进水管,配水管路设有出水口;集油槽围绕罐体的内壁形成环形。本实用新型的沉降除油罐采用立式竖流式储罐,设置均匀的集配水系统,在竖流状态下使水中的油、水和悬浮固体因密度不同而自然分离。本实用新型的采出水处理系统由一级处理的沉降除油罐和二级处理的化学调整旋流反应分离装置组成,采出水经过两级处理后,出水含油和悬浮物可达到15mg/L以内。
摘要附图
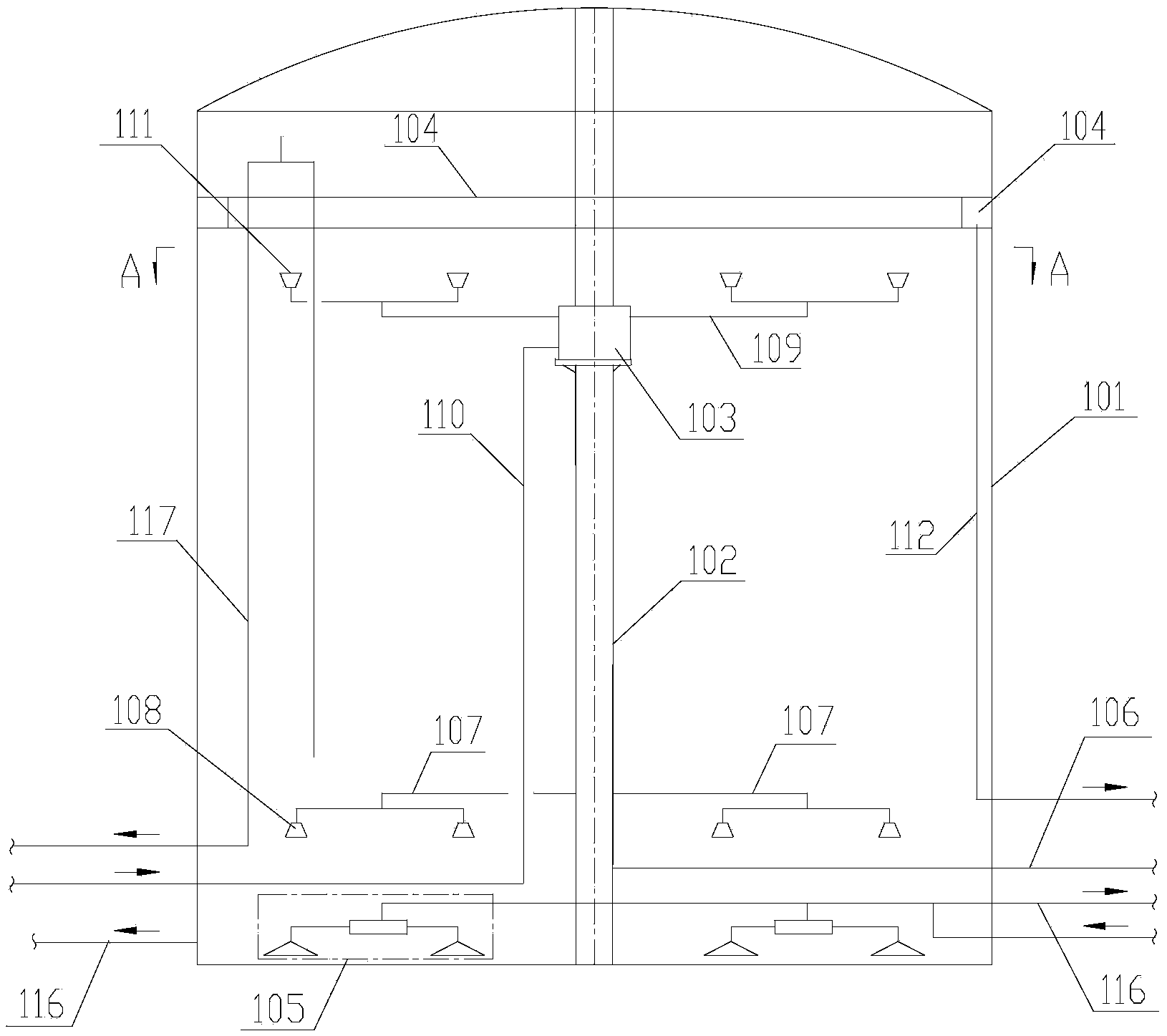
权利要求书
1.沉降除油罐,包括罐体,其特征在于,所述罐体内设置有中空的中心管柱、配水室、集油槽和排泥装置;
所述中心管柱竖直设于所述罐体内并至少下端密封,所述中心管柱的上部连通有延伸至所述罐体外的第一出水管,下部连通有位于所述罐体内的多个集水管路,所述集水管路上设置有入水口;
所述配水室连接有位于所述罐体内的多个配水管路和延伸至所述罐体外的第一进水管,所述配水管路上设置有出水口;
所述集油槽围绕所述罐体的内壁形成环形;
所述排泥装置设置于所述罐体内的底部。
2.根据权利要求1所述的沉降除油罐,其特征在于,每个所述配水管路包括垂直于所述中心管柱的一根配水干管、垂直连接于所述配水干管上的一根配水主支管和连接在所述配水主支管上的多根配水分支管,每根所述配水分支管上分别具有所述出水口。
3.根据权利要求2所述的沉降除油罐,其特征在于,所述出水口呈喇叭状并开口向上。
4.根据权利要求2所述的沉降除油罐,其特征在于,所述配水室套设在所述中心管柱上,多个所述配水管路的多根所述配水干管均布于所述配水室上。
5.根据权利要求1所述的沉降除油罐,其特征在于,每个所述集水管路包括垂直于所述中心管柱的一根集水干管、垂直连接于所述集水干管上的一根集水主支管和连接在所述集水主支管上的多根集水分支管,每根所述集水分支管上分别具有所述入水口。
6.根据权利要求5所述的沉降除油罐,其特征在于,所述入水口呈喇叭状并开口向下。
7.采出水处理系统,包括除油罐和化学调整旋流反应分离装置,其特征在于,所述除油罐为权利要求1至6中任一项所述的沉降除油罐,所述第一出水管连接至所述化学调整旋流反应分离装置。
8.根据权利要求7所述的采出水处理系统,其特征在于,所述化学调整旋流反应分离装置为旋流反应分离罐,所述旋流反应分离罐包括罐体和纵向置于所述罐体内的旋流反应中心筒,所述旋流反应中心 筒的下端与所述罐体的内腔相连通,所述旋流反应中心筒从上到下依次分为第一级旋流反应段、第二级旋流反应段和第三级旋流反应段;
所述罐体上固定连接有伸入到所述第一级旋流反应段内的第二进水管、伸入到所述第二级旋流反应段内的第二净水剂管和伸入到所述第三级旋流反应段内的絮凝剂管,所述第二进水管上连通有第一净水剂管;
所述罐体内的上部固定设置有集水管和位于所述集水管的上方的集油管,所述集水管上开设有进水口,所述集水管上连接有伸出所述罐体外的第二出水管;所述集油管上开设有进油口,所述集油管上连接有伸出所述罐体外的出油管;
所述罐体的底部连接有排泥管;
所述第一出水管与所述第二进水管连接。
9.根据权利要求8所述的采出水处理系统,其特征在于,所述集水管和集油管均为环形,所述集水管和集油管均套在所述旋流反应中心筒外,所述进水口为均布于所述集水管上的多个,所述进油口为均布于所述集油管上的多个。
10.根据权利要求8所述的采出水处理系统,其特征在于,所述第二进水管的轴线方向与所述旋流反应中心筒的内壁相切。
11.根据权利要求7所述的采出水处理系统,其特征在于,所述化学调整旋流反应分离装置包括旋流反应器和除渣分离罐;
所述旋流反应器包括罐体,所述罐体内设置有用于将所述罐体分隔为位于下部的第一级反应腔和位于上部的第二级反应腔的隔板;
对应所述第一级反应腔的罐体上开设有进水口,所述进水口内设置有伸入所述第一级反应腔内的第三进水管;
对应所述第二级反应腔的罐体上开设有净水药剂投加口和出水口,所述净水药剂投加口内设置有伸入所述第二级反应腔内的药剂投加管,所述出水口内设置有伸入所述第二级反应腔内的第三出水管,所述药剂投加管位于所述第二级反应腔的下部,所述第三出水管位于所述第二级反应腔的上部;
所述隔板上开设有通孔,所述通孔通过连接管与所述药剂投加管连通;
所述罐体的底部设置有排污放空管;
所述第三进水管与所述第一出水管连接。
12.根据权利要求11所述的采出水处理系统,其特征在于,所述除渣分离罐为喷雾除渣分离罐,所述喷雾除渣分离罐包括罐体、中心旋流筒、喷雾除渣装置、收油装置、排泥装置和收水装置;
所述中心旋流筒位于所述罐体内且上端敞口,下端与所述罐体固定并密封,所述中心旋流筒与所述罐体之间形成环腔,所述中心旋流筒的下部具有至少一个与所述罐体的内腔相连通的连通口,所述中心旋流筒的中部连接有第四进水管,所述第四进水管的一端位于所述中心旋流筒内,另一端与所述第三出水管连接;
所述喷雾除渣装置设置于所述中心旋流筒的上部外侧;
所述收油装置设置于所述中心旋流筒上端对应的罐体内壁上;
所述排泥装置设置于所述罐体底部对应所述连通口的位置;
所述收水装置包括安装于所述罐体外侧上部的外挂水箱和收水管,所述收水管包括收水环管和L状引管,所述收水环管位于罐体内的中部并套于所述中心旋流筒外;所述L状引管的一端与所述收水环管连通,另一端穿出所述罐体并伸入所述外挂水箱内,所述外挂水箱内连接有第四出水管。
13.根据权利要求12所述的采出水处理系统,其特征在于,所述外挂水箱内设置有水位调节器,所述水位调节器包括外筒、调节内筒、丝杆、安装架、手轮和手轮座,所述外筒固定于外挂水箱内的底部,所述L状引管位于所述外筒内,所述第四出水管位于所述外筒的外部;所述调节内筒套装于所述外筒内并能够上下移动,且所述调节内筒的外壁与所述外筒的内壁保持密封,所述调节内筒上固定有所述丝杆,所述安装架位于所述外筒的上方,所述手轮座的下端安装于所述安装架上,所述手轮座的上端安装所述手轮,所述手轮中部安装有能够使所述丝杆穿过的螺母。
14.根据权利要求12所述的采出水处理系统,其特征在于,所述第四进水管的轴线方向与所述中心旋流筒的内壁相切,且所述第四进水管的出口位于所述中心旋流筒的内壁上;所述收油装置为围绕所述 罐体的内壁形成的环形槽,所述环形槽上连接有伸出所述罐体外的收油管。
15.根据权利要求12所述的采出水处理系统,其特征在于,所述喷雾除渣装置包括收渣槽、集渣斗、收渣管和冲洗水管;
所述中心旋流筒的上端穿过所述收渣槽的底面位于所述收渣槽内,所述收渣槽的底面为一端高一端低的斜面;
所述集渣斗设置于所述收渣槽的底端的外部;
所述收渣管连接于所述集渣斗上并伸出所述罐体外;
所述冲洗水管的上端固定于所述中心旋流筒的上方,所述冲洗水管上连接有喷雾喷头,所述冲洗水管的下端穿出所述罐体外。
16.根据权利要求11所述的采出水处理系统,其特征在于,所述除渣分离罐为负压除渣分离罐,所述负压除渣分离罐包括罐体和设置于所述罐体内的筒体,所述筒体的上端敞口,下端与所述罐体固定并密封,所述筒体与所述罐体之间形成环腔,所述筒体的下部具有至少一个与所述罐体的内腔相连通的出口;所述筒体内的上部固定安装有收渣漏斗,所述收渣漏斗的底部连接有伸出罐体外的排渣管;所述筒体的中部连接有第五进水管;所述罐体的上部内壁上形成环形的收油槽,所述收油槽上连接有伸出所述罐体外的收油管;所述环腔的中部固定有环形的填料层;所述填料层上方的环腔内设置环形的收水管,所述收水管上连接有伸出所述罐体外的第五出水管;所述罐体底部固定有位于所述环腔内的第一环形吸泥管,所述填料层上方固定有第二环形吸泥管。
说明书
沉降除油罐及采出水处理系统
技术领域
本实用新型属于油田开发地面工程稠油采出水处理技术领域,特别是应用于国内外SAGD(SteamAssistedGravityDrainage蒸汽辅助重力泄油)稠油开发中产生的高温、低油水密度差和高乳化度的采出水处理中。
背景技术
目前国际通行的油田采出水处理技术主要为重力沉降除油、气浮、旋流除油器、过滤等除油工艺,出水再进行除盐和软化处理,然后用于锅炉给水。由于稠油开采的采出水温度较高,不适于利用生物法处理,主要使用的物理和物理化学处理方法有:
物理法:物理法主要利用物理原理分离水中的油、固体悬浮颗粒等杂质,物理法主要包括重力沉降分离法、旋流除油器去除法、平流式除油池分离以及过滤法。
物理化学法:对于采出水中存在分散油、乳化油及以分散态、溶解态、胶体物质存在的悬浮物时,不能单独采用物理法去除,需要进行化学和物理结合的方法去除。主要包括混凝沉淀、气浮法、化学药剂反应池等方法。
一般采出水处理系统的进水的含油为2000ppm,悬浮物为300ppm,系统总出水要求为含油和悬浮物均低于5ppm,采出水处理系统常见工艺流程为除油罐+气浮机+过滤器,针对于每段流程的处理设施略有不同。目前存在问题主要有两个方面,一是作为第一级的除油罐处理效率有待进一步提升,二是需要应用更加高效稳定的处理工艺来弥补单纯物理法的不足,现有技术特点及不足之处如下:
目前除油罐作为除油工艺的第一级处理设施,接受了含油2000ppm,悬浮物为300ppm的采出水原水水质,设计出水指标一般为含油小于300ppm、悬浮物小于150ppm,除油罐的设计除油率一般达90%,悬浮 物去除率达50%,但投资小于后端气浮和过滤器,属于除油系统达标运行首要关注因素。因除油罐出水不达标而造成后端气浮和过滤设备影响总系统出水水质,进而对后端的MVC(降膜蒸发除盐)等除盐设施带来破坏,并将导致高额的维修费用。因此保证处于整个除油工艺和除盐工艺最前端作为第一级处理设施的除油罐的处理效果是减轻后端处理压力、保证后端稳定运行的关键所在。目前国外常用的除油罐主要有以下两种形式:
平流式除油罐:该除油罐为水平流式,罐内部安装有竖直挡板,将罐体分割为几部分,相邻部分设过流通道,整体形成一个水平折流式除油罐。由于分隔开几部分,因此在有限的罐圆周截面积内形成较长的过流通道,水流流过时,油珠由于密度小于水而上浮至液面上部,从进水口至出水口,较大粒径的油珠依次完成上浮全过程,在除油罐顶部被收集排出,较小的油珠由于上浮速度小未能完成上浮去除过程而随水流进入下一级流程。
普通竖流除油罐:该除油罐为立式除油罐,水流总体来说为竖直流,进水通过罐中心筒上的出水箱出水,水箱出水采用管路出水,水流经配水管分配后垂直向下流,最后进入罐底收水口收集后排出罐外。
这些用于采出水的除油罐只考虑了油水密度差带来的油珠上浮效应,但未从油珠粗粒化改善、提高上浮速度方面做根本改进,且对来水波动性适应性较差,需针对均匀集配水、改善罐内水流态、改进排泥方式等方面进行优化
另一方面,国外大多数油田采出水处理工艺较单一,主要为物理流程即气浮流程,对来水波动性、水质差异性适应性较差,由于前段除油罐和气浮出水的不稳定造成过滤器滤料污染而停用的情况时有发生,且对于系统腐蚀、结垢没有专门的解决措施,药剂成本较高,且目前使用的药剂混凝反应沉降工艺不成熟,不适应油田采出水处理工程建设高效处理、水质稳定达标的要求。
综上所述,现有技术中采出水处理主要存在以下几个问题:
1)除油罐方面:
a、集水配水不均匀:以上两种除油罐均采用进水口大股进水的方式,水流进入罐中时扰动较大,没有均匀配水会影响水的流态,在水 中形成扰流,扰动水流多个方向的剪切力使得油珠除了上浮力带来的上浮速度外还有其他方向的速度,在有限的时间内影响了上浮高度,因此在设计除油率的要求下,提高了停留时间的要求。且没有均匀配水也减小了对来水冲击的适应能力,容易造成团聚状原油未能分配开来就进入除油罐,由于沉降能力不足而直接进入下端流程,对下端设备造成污染。除油后的水由于未能均匀收集,易形成短流,出水段出水口附近流态不好的地方易聚集污油和污泥,带来出水水质波动。
b、无高效的排泥设施:目前这两种除油罐内无专门排泥设施,上游带来的泥沙、有机物胶体和水中沉积污泥均自然沉降至罐底,目前设置排污口接清罐车定期清罐操作的方式去除,当污泥较少时只排出部分罐底水,当沉泥较大时清全罐。这种操作方式一方面不能全部去除罐底污泥,在清罐口另一侧的污泥依然会堆积,另一方面清全罐时需要停产,或除油罐一般要建两座,增加投资。
c、平流式除油罐流态不理想。由于水和油珠为同向流动,油珠除由于浮力带来的上浮速度外,还受水流剪切力左右而有一个水平前进速度,因此油珠实际为抛物线上浮轨迹。因水流流速远大于上浮流速,使得在有限的上浮高度内,水平推进轨迹较长,对流道长度要求较高,在上升高度不变的情况下,增大了除油罐截面积,有效停留时间相应延长。
2)工艺流程方面:现有除油罐和气浮流程不能确保出水水质稳定合格,对过滤器压力较大。部分油田原油脱水效果不良,使污水油含量大,冲击污水处理设施,前端一级处理的重力除油和二级处理的气浮和旋流除油器出水不稳定。随着多种二次、三次采油技术的大范围推广,回收水掺入采出水处理系统处理,使采出水粘度增加,乳化油更加稳定,油水密度差小,气浮和旋流分离器难以达到理想效果。在设备方面普遍存在小颗粒悬浮物及微小粒径油的去除效率低的缺陷,以上多种原因均将处理压力转嫁到过滤器,造成滤料堵塞影响处理效果,并因前端来油量不合格而使滤料污染无法运行的情况时有发生。
3)采出水处理系统无有效离子平衡措施,腐蚀结垢问题严重。由于除油罐+气浮流程仅对采出水进行物理法处理,对水中钙镁等成垢离子不能有效降低,除油系统结垢问题突出,除垢剂加药成本大。
4)化学处理工艺亟待优化。鉴于物理流程对出水稳定性和防垢能力的不足,部分油田开始采用化学药剂反应池的工艺来解决上述问题,但由于应用时间较短,仅为化学药剂反应絮凝池的工艺,没有形成有效、集成化的加药反应分离工艺和设备。絮凝反应池造价高、施工困难。用化学混凝沉降的方法处理含油污水时,需要投加大量的净水药剂,从而形成大量的絮体,絮体沉降后成为污泥,直接被沉降后排出,净水药剂的性能没有完全利用,并且形成的絮体松散,污泥沉降性能差,不利于后续污泥的脱水处理,因此工作效率低,工作质量差、成本高。
实用新型内容
鉴于现有技术中存在的上述问题,本实用新型所要解决的技术问题是提供一种能够有效的去除采出水中的油和悬浮固体的沉降除油罐。
为了解决上述技术问题,本实用新型采用了如下技术方案:沉降除油罐,包括罐体,
所述罐体内设置有中空的中心管柱、配水室、集油槽和排泥装置;
所述中心管柱竖直设于所述罐体内并至少下端密封,所述中心管柱的上部连通有延伸至所述罐体外的第一出水管,下部连通有位于所述罐体内的多个集水管路,所述集水管路上设置有入水口;
所述配水室连接有位于所述罐体内的多个配水管路和延伸至所述罐体外的第一进水管,所述配水管路上设置有出水口;
所述集油槽围绕所述罐体的内壁形成环形;
所述排泥装置设置于所述罐体内的底部。
作为优选,每个所述配水管路包括垂直于所述中心管柱的一根配水干管、垂直连接于所述配水干管上的一根配水主支管和连接在所述配水主支管上的多根配水分支管,每根所述配水分支管上分别具有所述出水口。
作为优选,所述出水口呈喇叭状并开口向上。
作为优选,所述配水室套设在所述中心管柱上,多个所述配水管路的多根所述配水干管均布于所述配水室上。
作为优选,每个所述集水管路包括垂直于所述中心管柱的一根集水干管、垂直连接于所述集水干管上的一根集水主支管和连接在所述集水主支管上的多根集水分支管,每根所述集水分支管上分别具有所述入水口。
作为优选,所述入水口呈喇叭状并开口向下。
本实用新型同时公开一种采出水处理系统,包括除油罐和化学调整旋流反应分离装置,所述除油罐为上述的沉降除油罐,所述第一出水管连接至所述化学调整旋流反应分离装置。
作为优选,所述化学调整旋流反应分离装置为旋流反应分离罐,所述旋流反应分离罐包括罐体和纵向置于所述罐体内的旋流反应中心筒,所述旋流反应中心筒的下端与所述罐体的内腔相连通,所述旋流反应中心筒从上到下依次分为第一级旋流反应段、第二级旋流反应段和第三级旋流反应段;
所述罐体上固定连接有伸入到所述第一级旋流反应段内的第二进水管、伸入到所述第二级旋流反应段内的第二净水剂管和伸入到所述第三级旋流反应段内的絮凝剂管,所述第二进水管上连通有第一净水剂管;
所述罐体内的上部固定设置有集水管和位于所述集水管的上方的集油管,所述集水管上开设有进水口,所述集水管上连接有伸出所述罐体外的第二出水管;所述集油管上开设有进油口,所述集油管上连接有伸出所述罐体外的出油管;
所述罐体的底部连接有排泥管;
所述第一出水管与所述第二进水管连接。
作为优选,所述集水管和集油管均为环形,所述集水管和集油管均套在所述旋流反应中心筒外,所述进水口为均布于所述集水管上的多个,所述进油口为均布于所述集油管上的多个。
作为优选,所述第二进水管的轴线方向与所述旋流反应中心筒的内壁相切。
作为优选,所述化学调整旋流反应分离装置包括旋流反应器和除渣分离罐;
所述旋流反应器包括罐体,所述罐体内设置有用于将所述罐体分 隔为位于下部的第一级反应腔和位于上部的第二级反应腔的隔板;
对应所述第一级反应腔的罐体上开设有进水口,所述进水口内设置有伸入所述第一级反应腔内的第三进水管;
对应所述第二级反应腔的罐体上开设有净水药剂投加口和出水口,所述净水药剂投加口内设置有伸入所述第二级反应腔内的药剂投加管,所述出水口内设置有伸入所述第二级反应腔内的第三出水管,所述药剂投加管位于所述第二级反应腔的下部,所述第三出水管位于所述第二级反应腔的上部;
所述隔板上开设有通孔,所述通孔通过连接管与所述药剂投加管连通;
所述罐体的底部设置有排污放空管;
所述第三进水管与所述第一出水管连接。
作为优选,所述除渣分离罐为喷雾除渣分离罐,所述喷雾除渣分离罐包括罐体、中心旋流筒、喷雾除渣装置、收油装置、排泥装置和收水装置;
所述中心旋流筒位于所述罐体内且上端敞口,下端与所述罐体固定并密封,所述中心旋流筒与所述罐体之间形成环腔,所述中心旋流筒的下部具有至少一个与所述罐体的内腔相连通的连通口,所述中心旋流筒的中部连接有第四进水管,所述第四进水管的一端位于所述中心旋流筒内,另一端与所述第三出水管连接;
所述喷雾除渣装置设置于所述中心旋流筒的上部外侧;
所述收油装置设置于所述中心旋流筒上端对应的罐体内壁上;
所述排泥装置设置于所述罐体底部对应所述连通口的位置;
所述收水装置包括安装于所述罐体外侧上部的外挂水箱和收水管,所述收水管包括收水环管和L状引管,所述收水环管位于罐体内的中部并套于所述中心旋流筒外;所述L状引管的一端与所述收水环管连通,另一端穿出所述罐体并伸入所述外挂水箱内,所述外挂水箱内连接有第四出水管。
作为优选,所述外挂水箱内设置有水位调节器,所述水位调节器包括外筒、调节内筒、丝杆、安装架、手轮和手轮座,所述外筒固定于外挂水箱内的底部,所述L状引管位于所述外筒内,所述第四出水 管位于所述外筒的外部;所述调节内筒套装于所述外筒内并能够上下移动,且所述调节内筒的外壁与所述外筒的内壁保持密封,所述调节内筒上固定有所述丝杆,所述安装架位于所述外筒的上方,所述手轮座的下端安装于所述安装架上,所述手轮座的上端安装所述手轮,所述手轮中部安装有能够使所述丝杆穿过的螺母。
作为优选,所述第四进水管的轴线方向与所述中心旋流筒的内壁相切,且所述第四进水管的出口位于所述中心旋流筒的内壁上;所述收油装置为围绕所述罐体的内壁形成的环形槽,所述环形槽上连接有伸出所述罐体外的收油管。
作为优选,所述喷雾除渣装置包括收渣槽、集渣斗、收渣管和冲洗水管;
所述中心旋流筒的上端穿过所述收渣槽的底面位于所述收渣槽内,所述收渣槽的底面为一端高一端低的斜面;
所述集渣斗设置于所述收渣槽的底端的外部;
所述收渣管连接于所述集渣斗上并伸出所述罐体外;
所述冲洗水管的上端固定于所述中心旋流筒的上方,所述冲洗水管上连接有喷雾喷头,所述冲洗水管的下端穿出所述罐体外。
作为优选,所述除渣分离罐为负压除渣分离罐,所述负压除渣分离罐包括罐体和设置于所述罐体内的筒体,所述筒体的上端敞口,下端与所述罐体固定并密封,所述筒体与所述罐体之间形成环腔,所述筒体的下部具有至少一个与所述罐体的内腔相连通的出口;所述筒体内的上部固定安装有收渣漏斗,所述收渣漏斗的底部连接有伸出罐体外的排渣管;所述筒体的中部连接有第五进水管;所述罐体的上部内壁上形成环形的收油槽,所述收油槽上连接有伸出所述罐体外的收油管;所述环腔的中部固定有环形的填料层;所述填料层上方的环腔内设置环形的收水管,所述收水管上连接有伸出所述罐体外的第五出水管;所述罐体底部固定有位于所述环腔内的第一环形吸泥管,所述填料层上方固定有第二环形吸泥管。
与现有技术相比,本实用新型的沉降除油罐、采出水处理系统和处理方法的有益效果在于:
1、本实用新型中的沉降除油罐采用立式竖流式储罐,设置均匀的 集配水系统,在竖流状态下使采出水中的油、水和悬浮固体因密度不同而自然分离,并具有收油及排泥功能,因而极大的提高了采出水除油的工作效率和工作质量。相比传统的平流式除油罐除油效率提高约40%,节约工程投资约30%,有效解决了现有技术中除油罐处理效率低的问题。
2、本实用新型的采出水处理系统主要由作为一级处理的沉降除油罐和作为二级处理的化学调整旋流反应分离装置组成,可弥补单纯物理法的不足,随着含油污水处理后达标回用的环保要求日益严格,以及对采出水处理系统出水稳定达标和有效防止腐蚀结垢的需求凸显,本实用新型兼顾水质净化和水质稳定,利用能有效控制采出水腐蚀结垢的化学调整旋流反应分离装置,以适应油水密度差小、含一定量高分子有机物或复杂水性采出水的处理。通过投加净水药剂(化学药剂),实现对采出水水性的改良,并通过高效的反应设备实现油、悬浮物和净水药剂的混合反应,并有效分离,实现水的净化,并对水中的成垢和腐蚀性离子进行控制。
3、本实用新型能够应用于国内外SAGD稠油开发中产生的高温低油水密度差和高乳化度采出水处理中,采出水经过这两级处理后,出水含油和悬浮物可达到15mg/L以内,后端辅以过滤即可满足回用要求。解决了高温低油水密度差高乳化度采出水油珠粒径小、油水稳定性强、常规处理流程难度大的问题,为稠油开发解决采出水达标处理回用锅炉的出路问题,避免的污水外排污染环境,同时节约清水产生巨大的经济效益。