申请日2015.03.19
公开(公告)日2015.06.17
IPC分类号C02F9/04
摘要
本发明提供了一种撬装轻型含油污水处理装置及其处理工艺,所述装置依次包括一级压力泵(2)、一级旋流分离器(3)、二级压力泵(4)、二级旋流分离器(5)、管道混合器(6)、悬浮污泥处理装置(7)和储罐。该工艺采用物理化学方法,将药剂与水经旋流分离器充分混合后,污水继续进悬浮污泥设备,完成混凝、沉淀、过滤三步骤。本发明巧妙的将药剂与水混合,达到除油和悬浮物的目的,工艺系统简单,稳定处理油田高含油污水,运行成本较低,不存在填料更换,设备维修成本低,可根据现场要求即停即操作,设备运输方便,占地面积小,无需对现场进行建站处理。
摘要附图
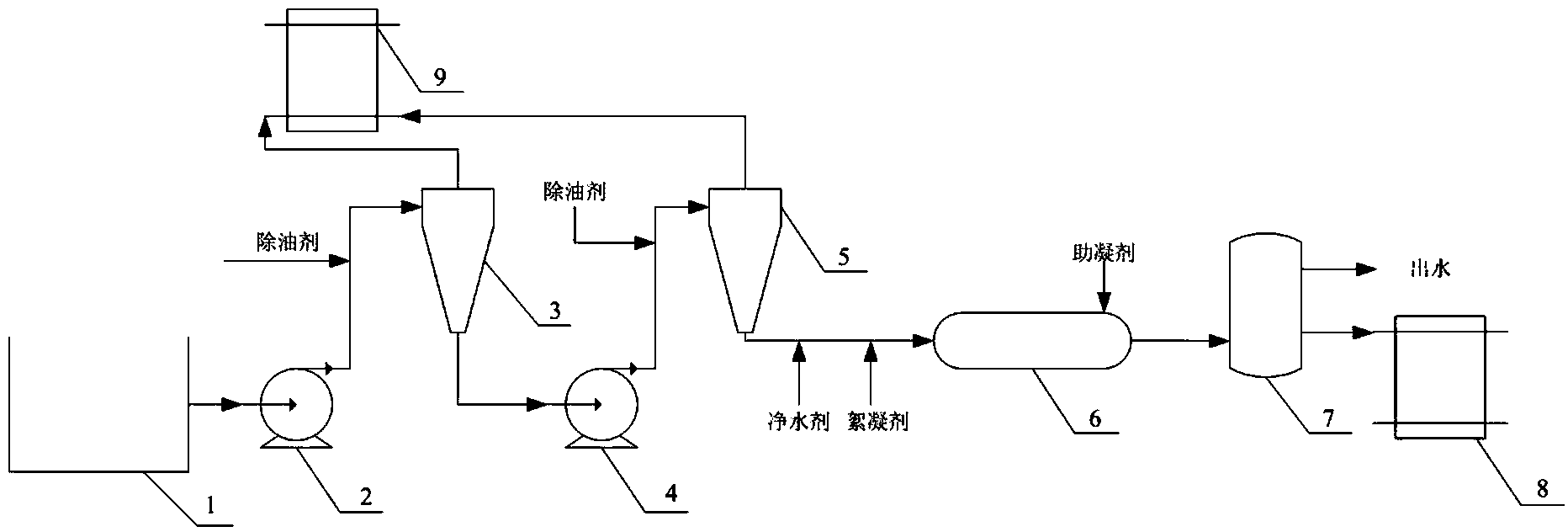
权利要求书
1.一种撬装轻型含油污水处理装置,其特征在于,所述装置依次包括一 级压力泵、一级旋流分离器、二级压力泵、二级旋流分离器、管道混合器、悬 浮污泥处理装置和储罐。
2.根据权利要求1所述的装置,其特征在于,所述一级压力泵为高压泵;
优选地,所述二级压力泵为高压泵;
优选地,所述储罐为储油罐和软体储存罐,其中储油罐与一级旋流分离器 和二级旋流分离器上部相连,软体储存罐与悬浮污泥处理装置下部排泥口相 连。
3.一种如权利要求1或2所述的装置的处理工艺,其特征在于,所述处理 工艺包括以下步骤:
(1)污水经一级压力泵输送至一级旋流分离器,并在一级旋流分离器入口 投加除油剂,污水与除油剂充分混合后油水分离,分离出的油进入储油罐;
(2)步骤(1)中处理后的污水经二级压力泵进入二级旋流分离器,同时 在二级旋流分离器入口投加除油剂,进行二次混凝处理,分离出的油进入储油 罐;
(3)经二级旋流分离器处理后的污水进入管道混合器,同时在管道混合器 前投加净水剂、絮凝剂,在管道混合器后投加助凝剂,污水与药剂在管道混合 器混合均匀后通过整流系统进入悬浮污泥处理装置,经悬浮污泥处理装置处理 后的泥水进入软体储存罐。
4.根据权利要求3所述的处理工艺,其特征在于,所述步骤(1)中一级 压力泵的压力为0.4~0.8MPa;
优选地,所述步骤(1)中一级压力泵采用变频控制,根据污水含油量的高 低调整压力。
5.根据权利要求3或4所述的处理工艺,其特征在于,所述步骤(1)中 的除油剂的用量为0.5~1.5mg/L。
6.根据权利要求3-5任一项所述的处理工艺,其特征在于,所述步骤(1) 中一级旋流分离器油水分离出分散油、浮油和乳化油;
优选地,所述步骤(1)中二级旋流分离器去除分散油、浮油和乳化油。
7.根据权利要求3-6任一项所述的处理工艺,其特征在于,所述步骤(2) 中二级压力泵的压力为0.4~0.8MPa;
优选地,所述步骤(2)中二级压力泵采用变频控制,根据污水含油量的高 低调整压力;
优选地,所述步骤(2)中的除油剂的用量为0.5~1.5mg/L;
优选地,所述步骤(2)中二级旋流分离器去除的分散油的分子粒径为 10~100μm;
优选地,所述步骤(2)中二级旋流分离器去除的浮油的分子粒径> 100μm;
优选地,所述步骤(2)中二级旋流分离器去除的乳化油0.001~10μm。
8.根据权利要求3-7任一项所述的处理工艺,其特征在于,所述步骤(3) 中絮凝剂为有机高分子絮凝剂;
优选地,所述有机高分子絮凝剂为聚丙烯酸、聚丙烯酸钠、聚丙烯酸、聚 丙烯酰胺、苯乙烯磺酸盐、木质磺酸盐、丙烯酸或甲基丙烯酸中任意一种或至 少两种的组合物;
优选地,所述步骤(3)中助凝剂为聚丙烯酸钠、聚乙烯吡烯盐或聚丙烯酰 胺中任意一种或至少两种的组合物。
9.根据权利要求3-8任一项所述的处理工艺,其特征在于,所述步骤(3) 中净水剂的加入量为50~60mg/L;
优选地,所述步骤(3)中絮凝剂的加入量为60~85mg/L;
优选地,所述步骤(3)中助凝剂的加入量为0.4~1.5mg/L;
优选地,所述步骤(3)中整流系统水流控制在0.5~0.8m/s。
10.根据权利要求1或2所述的处理装置,其特征在于,所述装置的处理 水量为1~15m3/h;
优选地,所述装置处理的污水中含油量为20~30%。
说明书
一种撬装轻型含油污水处理装置及其处理工艺
技术领域
本发明污水处理领域,尤其涉及一种撬装轻型含油污水处理装置及其处理 工艺。
背景技术
含油污水源于在油气田生产过程中所产出的地层伴生水,这种伴生水中含 有地层中的原油、悬浮物及其他复杂的矿物杂质,直接外排不仅污染环境,还 可能因地层缺水层支撑引发灾害,不能继续提升连续采油率。因此,采油污水 必须进行处理后才能回注到地层中。而在有些地层中,采出水中含油量比较 高,油田常用的处理工艺不能有效的处理水中所含的油。如在重油地区,较分 散的采油井采出的污水含油约25%以上时,前段必须预处理(主要设备是三相 分离器,重力除油罐、混凝沉降罐、缓冲罐等),将其含油量去除90%以上 后,才能进后续的多介质过滤器处理系统(主要设备核桃壳过滤器、石英砂过 滤器等),达标后回注。整个系统涉及设备比较多,设备维修成本比较高。
目前处理油田高含油污水的方法有:物理法、化学法、物理化学法、生物 法。
物理法中采用的主要技术是重力分离技术、过滤器分离技术、膜分离技 术。这三种技术共同的不足之处是含油量和悬浮物含量较高的情况下,设备结 垢腐蚀严重,填料污堵严重,设备清洗频繁,且能耗较高。
化学法主要是混凝沉淀、化学转化和中和法,用于处理含油污水中部分胶 体和溶解性物质,针对水中乳化油。通过投加药剂实现对胶体粒子的静电中 和、吸附、架桥,将乳化油从污水析出,达到净化的目的。但是,化学法处理 后的污水对后续工艺流程及装置要求较高。否则,即使污水中的部分胶体和溶 解性物质析出,配套的分离设备分离效果比较差时,也不能达到良好的处理效 果。
物理化学法常用方法主要有两种:气浮法和吸附法。气浮法是将空气以微 小气泡的形式注入水中,气泡在污水上升过程中带出污水中的悬浮油粒及悬浮 物,达到油水分离的目的,与药剂配合能使水中的部分乳化油和悬浮物等有害 物质得到有效去除。但是缺点是:面对前段水质含油变化较大时,气浮法出水 水质不稳定,且设备检修频繁。吸附法主要是利用吸附剂吸附污水中的污染 物。油田常用的吸附材料为活性炭,但由于吸附容量有限,吸附材料更换成本 比较高,且再生能力比较差,该方法适用污水深度处理。
发明内容
针对上述含油污水处理技术中系统涉及设备较多,维修成本高,对于水流 量较小的采油站建站不方便,设备结垢腐蚀严重,填料污堵严重,设备清洗频 繁,对后续处理工艺和装置要求较高等问题,本发明提供了对于污水中含油量 较高时的一种撬装轻型含油污水处理装置及处理工艺。针对水流量较小的采油 站,轻型移动式处理力装置不仅简化了处理工艺流程,节省了一次性投资成本, 还保证了出水水质——回注标准。
本发明采用物理化学方法,将药剂与水力旋流分离器充分混合后,污水继 续进悬浮污泥设备,完成混凝、沉淀、过滤三步骤。
为达此目的,本发明采用以下技术方案:
一种撬装轻型含油污水处理装置,包括一级压力泵、一级旋流分离器、二 级压力泵、二级旋流分离器、管道混合器、悬浮污泥处理装置和储罐,其中一 级高压泵、一级旋流分离器、二级高压泵、二级旋流分离器、管道混合器和悬 浮污泥处理装置依次相连。
所述一级压力泵为高压泵。
所述二级压力泵为高压泵。
所述储罐为储油罐和软体储存罐,其中储油罐与一级旋流分离器和二级旋 流分离器上部经管道相连,软体储存罐与悬浮污泥处理装置下部排泥口相连。
以上含油污水处理装置处理工艺,所述处理工艺包括以下步骤:
(1)污水经一级压力泵缓慢输送至一级旋流分离器,压力的作用下,水分 子与油更易脱离;并在一级旋流分离器入口投加除油剂,污水与除油剂切向进 入一级旋流分离器,污水与除油剂充分混合后,污水中的分散油、浮油快速与 水分离,分离出的分散油、浮油从一级旋风分离器上部收油管道流至储油罐, 而污水沿设备中轴线出水孔进二级旋流分离器。
考虑到污水再次进二级旋流分离器时,进水压力不够,再次投加的除油剂 混合不充分,因此二级旋流分离器入口前配二级压力泵,能将水中90%的 10~100μm分散油和大于100μm的浮油去除,也能去除部分粒径在0.001~10μm 的乳化油。
(2)步骤(1)中处理后的污水经二级压力泵进入二级旋流分离器,同时 在二级旋流分离器入口投加除油剂,进行二次混凝处理,设备分离出来的油进 入储油罐,污水进一下步处理。
(3)经二级旋流分离器处理后的污水进入管道混合器,同时在管道混合器 前投加净水剂、絮凝剂,在管道混合器后投加助凝剂,污水与药剂在管道混合 器混合均匀后通过整流系统进入悬浮污泥处理装置,经悬浮污泥处理装置处理 后的泥水进入软体储存罐。
所述步骤(1)中一级压力泵的压力为0.4~0.8MPa,例如0.4MPa、 0.45MPa、0.5MPa、0.55MPa、0.6MPa、0.65MPa、0.7MPa、0.75MPa或0.8MPa 等。
所述步骤(1)中一级压力泵采用变频控制,根据污水含油量的高低调整压 力。
所述步骤(1)中的除油剂为常规的WD22-401S系列和WD22-401Y系列。
所述步骤(1)中的除油剂的用量为0.5~1.5mg/L,例如0.5mg/L、0.53mg/L、 0.55mg/L、0.57mg/L、0.6mg/L、0.63mg/L、0.65mg/L、0.67mg/L、0.7mg/L、 0.73mg/L、0.75mg/L、0.77mg/L、0.8mg/L、0.83mg/L、0.85mg/L、0.87mg/L、 0.9mg/L、0.93mg/L、0.95mg/L、0.97mg/L、1mg/L、1.3mg/L或1.5mg/L等。
所述步骤(1)中一级旋流分离器油水分离出分散油、浮油和乳化油。
所述步骤(1)中二级旋流分离器去除分散油、浮油和乳化油。
所述步骤(2)中二级压力泵的压力为0.4~0.8MPa,例如0.4MPa、 0.45MPa、0.5MPa、0.55MPa、0.6MPa、0.65MPa、0.7MPa、0.75MPa或0.8MPa 等。
所述步骤(2)中二级压力泵采用变频控制,根据污水含油量的高低调整压 力。
所述步骤(2)中的除油剂为常规的WD22-401S系列和WD22-401Y系列。
所述步骤(2)中的除油剂的用量为0.5~1.5mg/L,例如0.5mg/L、0.53mg/L、 0.55mg/L、0.57mg/L、0.6mg/L、0.63mg/L、0.65mg/L、0.67mg/L、0.7mg/L、 0.73mg/L、0.75mg/L、0.77mg/L、0.8mg/L、0.83mg/L、0.85mg/L、0.87mg/L、 0.9mg/L、0.93mg/L、0.95mg/L、0.97mg/L、1mg/L、1.3mg/L或1.5mg/L等。
所述步骤(2)中二级旋流分离器去除、的分散油的分子粒径为10~100μm, 例如10μm、15μm、20μm、25μm、30μm、35μm、40μm、45μm、50μm、 55μm、60μm、65μm、70μm、75μm、80μm、85μm、90μm、95μm或100μm 等。
所述步骤(2)中二级旋流分离器去除的浮油的分子粒径>100μm,例如 110μm、200μm、300μm、400μm、500μm、600μm、700μm、800μm或900μm 以及更大的分子粒径。
所述步骤(2)中二级旋流分离器去除的乳化油0.001~10μm,例如 0.001μm、0.005μm、0.01μm、0.05μm、0.1μm、0.5μm、0.7μm、1μm、1.5μm、 2μm、2.5μm、3μm、3.5μm、4μm、4.5μm、5μm、5.5μm、6μm、6.5μm、 7μm、7.5μm、8μm、8.5μm、9μm、9.5μm或10μm等。
所述步骤(3)中净水剂为OTC-A和/或OTC-B,例如:聚合氯化铝和聚合 氯化铝铁的组合,聚合氯化铝铁和碱式氯化铝的组合,碱式氯化铝和聚丙烯酰 胺的组合,硫酸亚铁、硫酸铝和聚合硫酸铁的组合,聚合氯化铝、聚合氯化铝 铁、碱式氯化铝和聚丙烯酰胺的组合,聚合氯化铝、聚合氯化铝铁、碱式氯化 铝、聚丙烯酰胺、硫酸亚铁、硫酸铝和聚合硫酸铁的组合等。
所述步骤(3)中絮凝剂为有机高分子絮凝剂。
所述有机高分子絮凝剂为聚丙烯酸、聚丙烯酸钠、聚丙烯酸、聚丙烯酰 胺、苯乙烯磺酸盐、木质磺酸盐、丙烯酸或甲基丙烯酸中任意一种或至少两种 的组合物,所述组合典型但非限制性的实例有:聚丙烯酸和聚丙烯酸钠的组 合,聚丙烯酸钠和聚丙烯酸的组合,聚丙烯酸钠、聚丙烯酸和聚丙烯酰胺的组 合,苯乙烯磺酸盐、木质磺酸盐和丙烯酸的组合,木质磺酸盐、丙烯酸和甲基 丙烯酸的组合,聚丙烯酸、聚丙烯酸钠、聚丙烯酸、聚丙烯酰胺、苯乙烯磺酸 盐、木质磺酸盐、丙烯酸和甲基丙烯酸的组合等。
所述步骤(3)中助凝剂为助凝剂为聚丙烯酸钠、聚乙烯吡烯盐或聚丙烯酰 胺中任意一种或至少两种的组合物,所述组合典型但非限制性的实例有:聚丙 烯酸钠和聚乙烯吡烯盐的组合,聚乙烯吡烯盐和聚丙烯酰胺的组合,聚丙烯酸 钠、聚乙烯吡烯盐和聚丙烯酰胺的组合等。
所述步骤(3)中净水剂的加入量为50~60mg/L,例如50mg/L、51mg/L、 52mg/L、53mg/L、54mg/L、55mg/L、56mg/L、57mg/L、58mg/L、59mg/L或 60mg/L等。
所述步骤(3)中絮凝剂的加入量为60~85mg/L,例如60mg/L、63mg/L、 65mg/L、67mg/L、70mg/L、73mg/L、75mg/L、77mg/L、80mg/L、83mg/L或 85mg/L等。
所述步骤(3)中助凝剂的加入量为0.4~1.5mg/L,例如0.4mg/L、0.5mg/L、 0.6mg/L、0.7mg/L、0.8mg/L、0.9mg/L、1mg/L、1.1mg/L、1.2mg/L、 1.3mg/L、1.4mg/L或1.5mg/L等。
所述步骤(3)中整流系统水流控制在0.5~0.8m/s,例如0.5m/s、0.53m/s、 0.55m/s、0.57m/s、0.6m/s、0.63m/s、0.65m/s、0.67m/s、0.7m/s、0.73m/s、 0.75m/s、0.77m/s或0.8m/s等。
所述装置的处理水量为1~15m3/h,例如1m3/h、3m3/h、5m3/h、7m3/h、9m3/h、 11m3/h、13m3/h或15m3/h等。
所述装置处理的污水中含油量为20~30%,例如20%、21%、22%、23%、 24%、25%、26%、27%、28%、29%或30%等。
所述装置的尺寸为集装箱尺寸20#、40#,其长×宽×高=9m×2.7m× 2.5m。
依据Stokes定律和同向凝聚理论,当加药后的污水由罐体底部进入悬浮污 泥净化装置后,由于组件的特殊构造,水流方向发生很大的变化,造成较强烈 的紊动。这时污水中剩余的悬浮颗粒正处于前期混合反应阶段,紊动对混合反 应有益。随着后续絮凝不断进行,悬浮颗粒越来越大,悬浮物的絮凝过程到了 后期絮凝阶段,紊动的不利影响也越来越大,与絮凝过程的要求相适应,这时 混合液流过组件弯折,流速大大降低,且流动开始趋于缓和。因此在固液分离 组件下部的很小底层里,絮凝作用已基本完成。即整个完成了部分混凝过程。
由于这个悬浮污泥层是由污水中的污泥及混凝药剂形成的絮体本身组成 的,形成了动态平衡过滤体系。具体表现为:随着絮体由下向上运动,使泥层 的下表层不断增加、变厚,同时,随着污泥浓缩室澄清水旁路流动,引导着悬 浮泥层的上表层不断流入中心接泥桶,上表层不断减少、变薄。这样,悬浮泥 层的厚度达到一个动态的平衡,完成了过滤、沉淀过程。当混凝后的出水由下 向上穿过此悬浮泥层时,此絮体滤层靠界面物理吸附、网捕作用和电化学特性 及范德华力的作用,将悬浮胶体颗粒、絮体、部分细菌菌体等等杂质拦截在此 悬浮泥层上,使出水水质达到处理要求,即“oil≤6mg/L、SS≤2mg/L、粒径中 值≤1.5μm”。悬浮污泥净化装置可根据前段来水的水质变化,调整药剂的用 量,保证出水水质达标。此设备的详细运行方式及结构见专利: 200720169462.19(含油污水净化装置及具有该装置的净化系统)。
有益效果:
本发明所述的处理装置为撬装式,处理工艺包括了混凝、沉淀、过滤处理 过程,污水经二级旋流分离器后,可去除水中90%的10~100微米的分散油和大 于100微米的浮油,也能去除部分粒径在0.001~10微末的乳化油。最后经悬浮 污泥处理装置的出水水质能实现《SYT 5329-2012碎屑岩油藏注水水质推荐指 标及分析方法》中的标准,即“oil≤6mg/L、SS≤2mg/L、粒径中值≤1.5μm”。
本发明利用新型的处理设备,巧妙的将药剂与水混合,达到除油和悬浮物 的目的,工艺系统简单,稳定处理油田高含油污水,运行成本较低,不存在填 料更换,设备维修成本低,可根据现场要求即停即操作,设备运输方便,占地 面积小,无需对现场进行建站处理。