申请日2010.06.25
公开(公告)日2011.12.28
IPC分类号C02F1/40
摘要
本发明涉及一种处理废水中重质乳化油的方法;处理装置为下部鼓泡段为气升式内环流反应器,上部泡沫段为溢流槽式的气液分离器;调节废水的pH为8~9,将废水通入鼓泡段;在塔底通入空气,加入絮凝剂和表面活性剂;通过收集泡沫,将乳化油从废水中分离;无机絮凝剂用量为:0.02~0.1mmol/g COD;聚合物絮凝剂用量为:10~50mg/m3废水;阴离子表面活性剂,用量为:5~20mg/g COD,且不低于15~20mg/m3废水;保持空塔气速为0.5~1.5cm/s;分离效率高:一次分离率可达90%以上;工艺过程简单:废水一次通过脱除固体悬浮物;能耗和剂耗低:絮凝剂用量低,流程短。
摘要附图
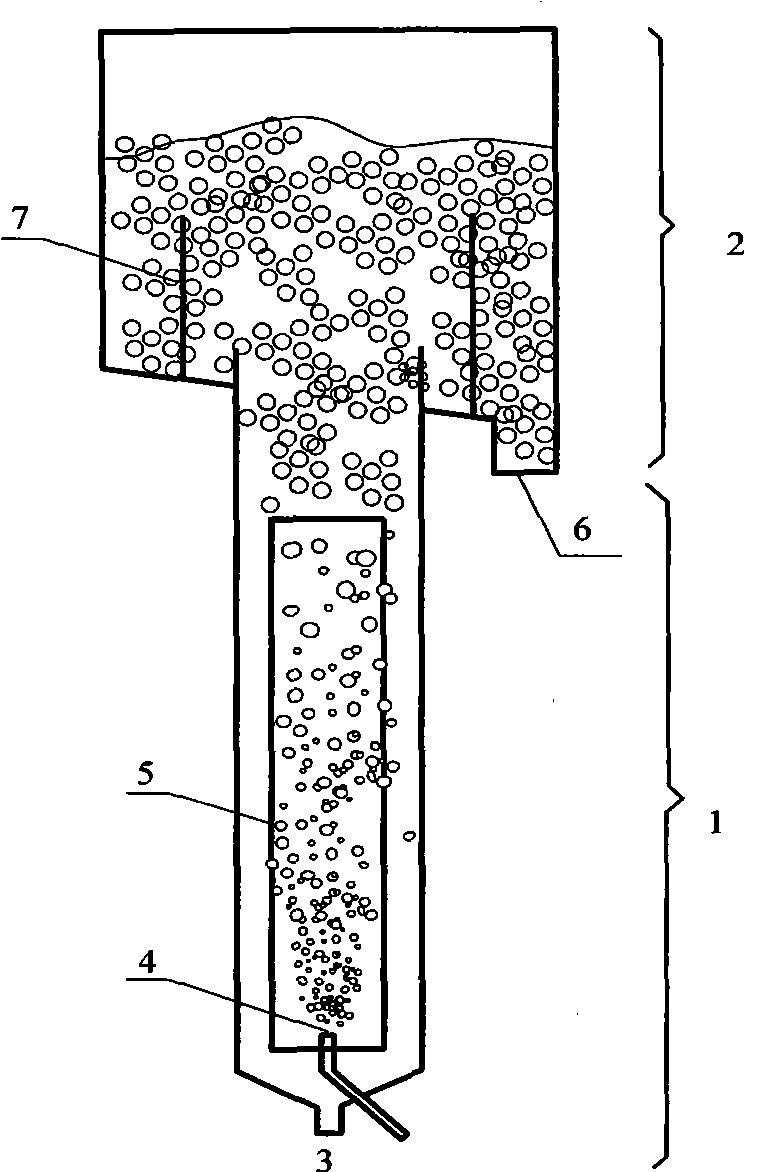
权利要求书
1.一种处理废水中重质乳化油的方法,其特征在于:
处理装置为一种由鼓泡段和泡沫段构成的环流泡沫分离塔,下部鼓泡段为气升式 内环流反应器,上部泡沫段为溢流槽式的气液分离器;调节废水的pH为8~9,将废 水通入环流泡沫分离塔的鼓泡段;在塔底通入空气,加入絮凝剂和表面活性剂;表面 活性剂产生泡沫,使絮凝的乳化油滴富集在泡沫表面,通过收集泡沫,将乳化油从废 水中分离;
所述絮凝剂由无机絮凝剂和聚合物絮凝剂构成;无机絮凝剂用量为:0.02~0.1 mmol/g COD;聚合物絮凝剂用量为:10~50mg/m3废水;
所述表面活性剂为阴离子表面活性剂,其用量为:5~20mg/g COD,且不低于15 ~20mg/m3废水;
所述的空气通入量为:保持空塔气速为0.5~1.5cm/s。
2.根据权利要求1所述的处理废水中重质乳化油的方法,其特征在于:无机絮凝 剂为氯化铝、硫酸铝、硫酸亚铁、三氯化铁、氯化钙;聚合物絮凝剂为聚丙烯酰胺。
3.根据权利要求1所述的处理废水中重质乳化油的方法,其特征在于:可选择 十二烷基磺酸钠、十二烷基硫酸钠中的一种或其组合。
4.根据权利要求1所述的处理废水中重质乳化油的方法,其特征在于:所述环流 泡沫分离塔鼓泡段和泡沫段的直径比为1∶(1.4~1.8),高度比为1∶(0.4~0.8);泡沫 段溢流槽堰和鼓泡段直径比为(1~1.4)∶1,溢流槽堰和泡沫段的高度比为(0.1~0.3)∶1。 鼓泡段中的导流筒可为单级或多级导流筒。
说明书
处理废水中重质乳化油的方法
技术领域
本发明涉及一种从原油加工废水中脱除重质乳化油的方法。
背景技术
重质原油即稠油加工过程会产生大量含有重质乳化油的废水,包括原油罐底脱 水、脱盐脱钙污水、焦化大吹汽冷凝水等,这种水与普通炼油废水、油田废水相比, 其突出特点是:①乳化油含量高:一般情况下,重质原油加工废水中一半以上的油以 乳化油形式存在,除去浮油和分散油后,80%以上的COD是由于乳化油和胶态悬浮 物产生的;②乳化程度严重,乳滴稳定:重质乳化油的乳滴直径通常只有几百纳米 到几微米,由于废水中存在着采油过程中引入的大量界面活性物质以及大量的胶质、 沥青质的悬浮物,使得乳滴非常稳定;③乳化油粘度大:重质原油的粘度大,其100 ℃的运动粘度可达到100mm2/s以上,高粘度使乳滴界面异常稳定,流动性变差,造 成乳滴不易聚并和吸附;④乳化油密度大:重质原油的密度与水接近,因此通过沉降 方法分离油水的效率非常低,即使絮凝后的乳化油与水分离效果仍然较差。
由于重质乳化油含量高,且难以被生物降解,因此在进入生化处理前,必须先采 用物理和化学的方法进行预处理,而预处理的核心环节就是脱除浮化油。目前,脱除 浮化油方法包括吸附、萃取、絮凝沉降、气浮、膜分离等,其中絮凝沉降和气浮方法 比较常见,由于重质原油的密度高、粘度大,絮凝后的乳化油相分离不好,沉降分离 时间长、效率低,因而采用上述单一方法进行重油乳化油脱除效果很不理想;若经絮 凝沉降分离后,进一步采用气浮等手段分离未沉降分离的乳化油,又存在过程复杂、 能耗高缺陷。如陈春茂等在2007年第4期《炼油技术与工程》“辽河石化超稠油污 水预处理工艺与工程实践”中报道的采用水质水量调节—破乳除油—旋流油水分离— 浮选净化工艺对超稠油污水预处理的方法。
由于乳化程度高,乳滴非常小且异常稳定,而稳定的油滴在气泡界面的吸附量非 常小,因此需要大量的气泡界面吸附乳滴,需要多级气浮以达到需要的分离效果,从 而导致气浮分离能耗高且分离效率低,例如CN101327966公开的一种稠油污水射流 溶气气浮工艺,包括一次气浮、射流溶气、二次气浮等在内的多级分离技术。
近年来,一些新的高效气浮分离设备和技术被报道,如US 2008/0006588公开的 气旋浮选分离技术,CN 1546196公开的加压溶气气浮水力旋流油水分离的方法和装 置,其采用气浮脱油和旋流分离结合方式对含油废水料液进行脱油,上述文献均没有 报道对重质乳化油废水的分离效果。
US 5897772公开了一种多级环流泡沫分离塔等。多级环流泡沫分离塔是一种在 环流反应器基础上开发的气浮分离设备。由于气浮分离的效率很大程度上取决于气泡 与连续相充分、快速的接触,与一般的气浮设备相比,环流反应器内气泡快速湍动, 气液接触充分,可使被分离的物质较快的富集在泡沫表面上,因而能显著提高泡沫分 离的效率。实验证实,该技术对于大小在10μm以上的乳化油有较高的分离效率。对 粒径更小、界面流动性差的重质油乳滴没有显著的分离效果,这是因为乳化体系的稳 定性提高,乳滴的界面性质发生很大变化,界面电荷相斥,很难仅通过泡沫分离的技 术将乳滴聚集分离,必须先采用其他技术使乳滴直径增加,表面性质改善而利于泡沫 分离。
CN1435275A在传统鼓泡式反应器基础上公开了一种多级环流反应器,塔内置有 导流筒,导流筒底部设有气体分布器,该反应器可广泛用于氧化反应、发酵过程、烃 加工反应以及活性污泥污水处理过程等各类气-液或气-液-固化学反应过程当中。
发明内容
本发明的目的在于提供一种利用环流泡沫分离塔分离脱除重质原油加工废水中 乳化油的方法。本方法是在多级环流泡沫分离塔和环流反应器及多级环流反应器的基 础上,结合絮凝技术,针对粒径在10μm以下的乳化重质油滴,开发出的一种絮凝- 环流泡沫分离处理乳化油的方法,可提高重质乳化油分离效率,简化分离流程。
本发明所述的处理废水中重质乳化油的方法是通过如下技术方案实现的:
处理装置为一种由鼓泡段和泡沫段构成的环流泡沫分离塔,下部鼓泡段为气升式 内环流反应器,上部泡沫段为溢流槽式的气液分离器;调节废水的pH为8~9,将废 水通入环流泡沫分离塔的鼓泡段;在塔底通入空气,加入絮凝剂(由无机絮凝剂和聚 合物絮凝剂组成)和表面活性剂;表面活性剂产生泡沫,使絮凝的乳化油滴富集在泡 沫表面,通过收集泡沫,将乳化油从废水中分离。
所述环流泡沫分离塔由下部鼓泡段和上部泡沫段构成,由于多级环流泡沫塔的鼓 泡段相当于一种多级环流反应器,因此本发明的分离塔下部鼓泡段成为一种气升式内 环流反应器,上部泡沫段为溢流槽式的气液分离器。具体地说,环流泡沫分离塔,由 鼓泡段1和泡沫段2构成,鼓泡段1为气升式内环流反应器,包括导流筒5和气体分 布器4,其中多级导流筒或单级导流筒,单级导流筒为导流筒的常规设计,多级导流 筒按照专利CN1435275设计,专利CN1435275一种用于各类气-液两相和气-液-固三 相化学反应多级环流反应器,包括塔身、导流筒、气体分布器,塔身内有导流筒,导 流筒的底部有气体分布器,塔身总高与反应器内径之比为3~12,导流筒直径与反应 器内径之比为0.3~0.9。泡沫段位于鼓泡段上方,为溢流槽式气液分离器,有溢流堰 7和泡沫排出口6。环流泡沫分离塔鼓泡段和泡沫段的直径比为1∶1.4~1∶1.8,高度比 为1∶0.4~1∶0.8;泡沫段溢流槽堰和鼓泡段直径的比为1∶1~1.4∶1,溢流槽堰和泡沫段的 高度比为0.1∶1~0.3∶1。所述的废水为含有重质原油加工过程中产生含有的重质乳化 油的废水,乳滴在2~10μm范围内,乳化油产生的COD占废水总COD的75%~95%, 包括但不限于油罐底脱水、脱盐脱钙污水、油田超稠油污水、焦化大吹汽冷凝水。
所述的絮凝剂由无机絮凝剂和聚合物絮凝剂组成,其中无机絮凝剂为氯化铝、硫 酸铝、硫酸亚铁、三氯化铁、氯化钙,常规无机铝、铁、钙盐絮凝剂用量为(乳化油 按COD计量,絮凝剂按所含金属离子的物质的量计量):(0.02~0.1)mmol/g COD; 聚合物絮凝剂为聚丙烯酰胺,其用量为:10~50mg/m3废水。所述表面活性剂为阴离 子表面活性剂,可选择十二烷基磺酸钠、十二烷基硫酸钠中的一种或其组合,其用量 为和乳化油含量满足(乳化油按COD计量):5~20mg/g COD乳化油,且不低于 15~20mg/m3废水。
所述通入空气的量为:保持空塔气速为0.5~1.5cm/s。
本发明的絮凝-环流泡沫分离废水中重质乳化油的方法,可采用连续操作,也可 采取批式操作。
批式操作:废水一次性泵入环流泡沫分离塔鼓泡段,液面高度不低于导流筒上沿, 且和导流筒上沿高度的比为1∶1~1∶1.25,用酸碱调节pH为8~9;从气体分布器通入空 气,通气量保证空塔气速为0.5~1.5cm/s;分别缓慢流加无机絮凝剂水溶液(浓度为 饱和浓度5%~25%)和聚合物絮凝剂聚丙烯酰胺的水溶液(浓度为25~250mg/L); 表面活性剂配置成一定浓度(为临界胶束浓度10%~40%)的水溶液,存储在储罐中, 待絮凝过程发生后,开始用计量泵以恒定速率流加表面活性剂溶液到鼓泡段任意位 置,表面活性剂用量为5~20mg/g COD,且不低于15~20mg/m3废水,流加速率根 据用量和溶液浓度以及分离总时间的确定;同时开始从泡沫段底部的泡沫收集口6 收集泡沫,当乳化油的脱除率达到排放要求后,完成一个批次的操作。
连续操作:环流泡沫塔中通入空气,保证空塔气速为0.5~1.5cm/s,废水事先用 酸碱调节pH为8~9,然后以通过泵8泵入环流泡沫分离塔的鼓泡段,水力停留时间 为0.5~2h,进料速率根据水力停留时间确定,进料口可在鼓泡段的任意位置;表面 活性剂、无机絮凝剂、聚合物絮凝剂配置成一定浓度的水溶液(无机絮凝剂浓度为饱 和浓度5%~25%,聚合物絮凝剂浓度为25~250mg/L,表面活性剂浓度为临界胶束浓 度10%~40%,),分别储存在不同的储罐9、10、11中,用计量泵12以恒定速率流加 到鼓泡段任意位置,流加速率根据用量、溶液的浓度和液相的停留时间确定;从泡沫 收集口连续收集泡沫而收集乳化油;从鼓泡段底部排液口3排出脱除乳化油后的废 水,整个操作过程中保证塔内装液量不变。
本发明原理:在含乳化油污水中,添加一定类型和一定量的絮凝助剂,将乳滴聚 集成一定大小,中和乳滴上的部分表面电荷,改善乳滴的表面性质,降低乳化体系的 稳定性,使用与絮凝助剂配合的表面活性剂形成泡沫,使聚集长大的乳滴高效的吸附 在泡沫相中从而被分离。本发明中所谓的“控制絮凝”并不形成絮凝相,而是使油滴 长大,达到泡沫分离较好的范围,然后用泡沫进行分离。
本发明的优点和有益效果是:
分离效率高:采用控制絮凝的方法,使乳化油的直径增加,界面性质改变,并中 和了部分界面电荷,从而满足了泡沫分离的要求,再结合采用高效的环流泡沫分离, 重质乳化油的一次分离率可达90%以上。
工艺过程简单:废水一次通过环流泡沫分离塔,即可实现乳化油和固体悬浮物的 脱除,脱油后的污水可直接进行生化处理,使重质原油加工废水的处理工艺和过程简 化。
能耗和剂耗低:絮凝剂的用量低于传统的絮凝-沉降分离方法,同时由于缩短了 工艺流程,也就避免了废水在各处理单元的传输和循环,降低了能耗。