申请日2010.02.11
公开(公告)日2010.07.28
IPC分类号C02F103/18; C02F1/44
摘要
本发明为一种石膏制酸炉气净化酸性污水的处理方法,其技术方案为将来自炉气吸收净化装置的待处理酸性污水,经膜过滤器循环过滤处理,分离出所含固体杂质后,清液送回炉气吸收净化装置循环利用;当净化后清液在系统内循环至酸度达到10~15%时,直接送入制酸系统干吸工段配制硫酸;所说的膜过滤器为多孔过滤筒形式的过滤器,由筒体和过滤元件组成,过滤元件为至少一个或多个多孔过滤筒,由花板固定在膜过滤器筒体的中部。本发明运行成本低于0.2元/立方污水,占地仅为传统法污水处理的10%,投资小、自动化程度高,能够实现污水零排放和节能减排,有利于保护环境,对石膏制酸的推广具有重要意义。
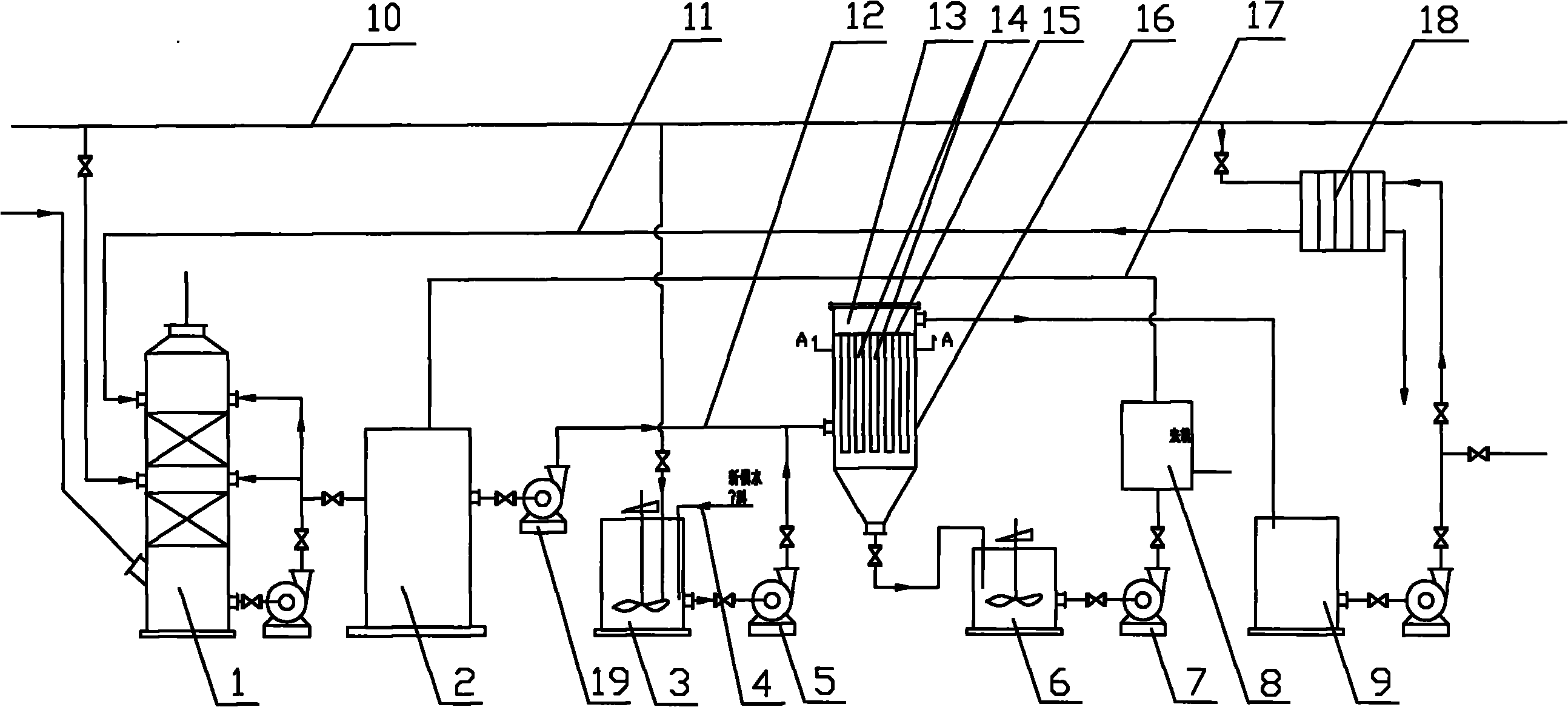
权利要求书
1.一种石膏制酸炉气净化酸性污水的处理方法,其特征在于来自炉气吸收净化装置的待处理酸性污水,经膜过滤器循环过滤处理,分离出所含固体杂质后,清液送回炉气吸收净化装置循环利用;当净化后清液在系统内循环至酸度达到10~15%时,直接送入制酸系统干吸工段配制硫酸。
2.一种适用于权利要求1所述石膏制酸炉气净化酸性污水处理方法的装置,其特征在于包括炉气吸收净化器、污水缓冲池、膜过滤器、板框压滤机、预涂料槽、污泥槽、清液槽和冷凝器;所述炉气净化器的污水出口与污水缓冲池、膜过滤器进水口之间通过污水管依次连接,膜过滤器出水口与清液槽、冷凝器通过管道依次连接,所述冷凝器出水口也炉气吸收净化器进水口通过清液管连接;所述膜过滤器下部的排污口与污泥槽、泥浆泵、板框压滤机通过管道依次连接,板框压滤机出水口通过滤液管与污水缓冲池连接,所述的冷凝器的出水口通过清液管与炉气吸收净化器连接,所述炉气吸收净化器和冷凝器分别与新鲜水管连接;所述预涂料槽通过预涂料泵与膜过滤器进水口连接,预涂料槽的上部分别与预涂料管和新鲜水管连接。
3.如权利要求2所述的污水处理的装置,其特征在于所说的膜过滤器为多孔过滤筒形式的过滤器,由筒体和过滤元件组成,过滤元件为至少一个多孔过滤筒,由花板固定在膜过滤器筒体的中部;筒体中部设有待处理污水—浊液进口,筒体上部设有清液出口,过滤器底部设有分离出泥渣出口。
4.如权利要求2或3所述的用于石膏制酸炉气净化酸性污水处理的装置,其特征在于所说的过滤元件多孔过滤筒的外面套有聚烯烃薄膜为过滤材料,该膜的特点是膜断面形态的不对称性,由表面层与大孔支撑层两层组成;表面层很薄,厚度0.1-1.5μm,孔径3-5微米,表面光滑疏水;支撑层呈多孔状,厚度为50-250μm,起支撑作用。
5.如权利要求1所述的炉气净化酸性污水 的处理方法,其特征在于所说的污水循环过滤处理的过程包含预涂—污水循环过滤处理—反冲—排渣四步操作步骤。
6.如权利要求1或5所述的炉气净化酸性污水的处理方法,其特征在于所说的预涂步骤采用的预涂材料为硅藻土、粉煤灰及硫酸钙的组合物,其重量配比为硅藻土∶粉煤灰∶硫酸钙=20∶75∶5,其自然形成的粒度为5-250微米,比表面积300-360g/cm2;预涂操作步骤为:首先在预涂槽中,将预涂料与清水按20∶80重量比例配制成预涂液,同时搅拌防止沉淀,系统开机时用泵将该预涂液自污水进口送人过滤器,对过滤膜预涂15~20秒钟,然后关闭预涂液进料阀,开启污水进料阀,切换至常规污水循环过滤处理流程。
7.如权利要求1或5所述的炉气净化酸性污水的处理方法,其特征在于所说的污水循环过滤处理步骤为:将来自炉气吸收净化装置的待处理的污水,送入污水缓冲池,用进液泵打入膜过滤器,控制过滤压力在0.15-0.23Mpa,清液主流经膜过滤器上部排出,经冷却器降温后返回炉气净化装置;当膜过滤器排出的清液循环至酸度达到10~15%时,即送往制酸系统干吸工段用于配制硫酸;同时,向炉气净化酸性污水的处理系统中补入适量新鲜水,继续进行酸性污水的循环处理。
8.如权利要求1或5所述的炉气净化酸性污水的处理方法,其特征在于所说的反冲步骤为:当过滤压力达0.21~0.23Mpa时,即中止过滤过程,进行反冲操作,自动关闭污水进液阀门的同时打开底部排污阀门,迅速使清液返流,将滤饼和预涂料全部从滤膜表面脱落。
9.如权利要求1或5所述的炉气净化酸性污水的处理方法,其特征在于所说的排渣步骤为:将反冲后脱落的滤渣—泥渣用泥浆泵打入板框压滤机压滤后,滤饼送渣场,滤液送回污水缓冲池;然后,补充新鲜水,开始新的炉气净化酸性污水处理的循环周期。
10.如权利要求2或3所述的污水处理的装置,其特征在适用于年产20万吨石膏硫酸装置的炉气净化酸性污水处理装置如下:
该处理装置包括炉气吸收净化器1、污水缓冲池2、膜过滤器13、板框压滤机8、预涂槽3、污泥槽6、清液槽9和冷凝器18,所述炉气净化器1的污水出口与污水缓冲池2、污水泵19、膜过滤器13进水口之间通过污水管12依次连接,膜过滤器13出水口与清液槽9、冷凝器18通过管道依次连接,所述冷凝器18出水口也炉气吸收净化器1进水口通过清液管9连接;所述膜过滤器13下部的排污口与污泥槽6、泥浆泵7、板框压滤机8通过管道依次连接,板框压滤机8出水口通过滤液管17与污水缓冲池2连接,所述的冷凝器18的出水口通过清液管11与炉气吸收净化器1连接,所述炉气吸收净化器1和冷凝器18分别与新鲜水管10连接;所述预涂料槽3通过预涂料泵5与膜过滤器13进水口连接,预涂料槽3的上部分别与预涂料管4和新鲜水管10连接;
其中共需要四台并联安装的膜过滤器,膜过滤器外形为直立圆筒下锥型,直径为3000mm,总高度为6500mm,分为上筒体、下锥筒体,每台膜过滤器过滤元件为三十二个多孔过滤筒,由花板固定在膜过滤器上筒体的顶部;下锥筒体设有浊液—待处理污水进口,上筒体顶部设有清液出口,膜过滤器底部设有分离出的泥渣出口;
每一个多孔过滤筒的外面均套有聚烯烃滤膜为过滤材料,该滤膜由表面层与大孔支撑层两层组成;表面层厚度0.5μm,孔径3微米,表面光滑疏水;支撑层呈多孔状,厚度为200μm。在每个循环过滤处理周期开始前,须在滤膜表面预组分为硅藻土、粉煤灰及硫酸钙的预涂材料。
说明书
一种石膏制酸炉气净化酸性污水的处理方法及装置
技术领域:
本发明属工业污水处理领域,涉及各种石膏制硫酸窑气和各种含固量低于10%的炉气净化洗涤酸性污水的处理。
背景技术:
用石膏制硫酸的工艺,与传统硫铁矿和硫磺制酸工艺截然不同,传统硫铁矿制硫酸,硫铁矿沸腾燃烧炉达到一定温度后,靠自身燃烧氧化气氛操作,炉气净化所产生的污水中含有氧化铁、砷、氟和少量重金属等杂质,该污水使用传统污水沉降设备,如斜管沉降器可以解决污水净化部分循环利用,少量的酸性水与石灰中和后,过滤达标排放。硫磺制酸靠硫磺在焚硫炉中的燃烧,炉气干净,不需净化,所以不产生酸性污水。而石膏制硫酸时,石膏分解和烧制水泥熟料的温度需烟煤燃烧提供,且用焦炭作还原剂,在回转窑中分解部分属还原气氛,煅烧部分属氧化气氛,因此,所产生的窑气中含有少量硫酸钙、飞灰、微量单质硫、煤焦油等矿尘,水洗净化产生的酸性污水属悬浊液,不沉淀,并含有胶质发粘等物质,采用传统的工艺方法难以分离。现有的污水处理装置采用的流程是首先制备含氢氧化钙10%的乳液后送石灰乳槽待用,用空气搅拌以防沉淀,石灰乳用泵输送至高位槽计量后加入中和槽内在搅拌的情况下与硫酸污水充分混合,进行中和,然后流入沉淀槽,沉降的清液从沉淀槽上部溢出,沉淀下来的含水80-90%的污泥,定期或连续的从沉淀槽底部放入压滤机,进行压滤。分离出的滤液与沉清液汇集在一起,因其含杂质较多,难以循环利用,一般是经调整PH值后达标排放,干污泥则用车运走做炼铁的原料。因此,采用传统的污水处理工艺,会造成大量污水排放,无法实现污水治理闭路循环和节能减排。
发明内容:
本发明提供了一种适用于石膏制酸炉气净化酸性污水的处理方法。该方法是将来自炉气吸收净化装置的待处理酸性污水,经膜过滤器循环过滤处理,分离出所含固体杂质(泥浆)后,清液送回炉气吸收净化装置循环利用;当净化后清液在系统内循环至酸度达到10~15%(以H2SO4重量%计)时,可直接送入制酸系统干吸工段配制硫酸。
本发明所述方法,解决了石膏制酸的酸性污水处理问题,实现了炉气净化酸性污水净化后的循环利用,系统无污水对外排放。
实施本发明所述酸性污水处理方法的装置为新型的膜过滤系统装置,包括炉气吸收净化器、污水缓冲池、新型膜过滤器、板框压滤机、预涂料槽、污泥槽、清液槽和冷凝器;所述炉气净化器的污水出口与污水缓冲池、膜过滤器进水口之间通过污水管依次连接,膜过滤器出水口与清液槽、冷凝器通过管道依次连接,所述冷凝器出水口也炉气吸收净化器进水口通过清液管连接;所述膜过滤器下部的排污口与污泥槽、泥浆泵、板框压滤机通过管道依次连接,板框压滤机出水口通过滤液管与污水缓冲池连接,所述的冷凝器的出水口通过清液管与炉气吸收净化器连接,所述炉气吸收净化器和冷凝器分别与新鲜水管连接;所述预涂料槽通过预涂料泵与膜过滤器进水口连接,预涂料槽的上部分别与预涂料管和新鲜水管连接。
本发明所述的炉气净化酸性污水循环过滤处理过程包括自动实现预涂-污水循环过滤处理-反冲-排渣四步操作步骤。
其中污水循环过滤处理为实施炉气净化酸性污水处理和循环利用的常规运行步骤,具体运行过程如下:
将来自炉气吸收净化装置的待处理的污水,送入污水缓冲池,用进液泵打入膜过滤器,过滤出的清液经膜过滤器上部排出,经冷却器降温后返回炉气净化装置,作为炉气吸收净化液循环使用;膜过滤器过滤出的泥渣经反冲后,用泥浆泵打入板框压滤机压滤后,滤饼去渣场,滤液送去污水缓冲池,与来自炉气吸收净化装置的待处理的污水混合,重新进入膜过滤器进行过滤处理;当膜过滤器排出的清液循环至酸度达到10~15%时,即送往制酸系统干吸工段用于配制硫酸;同时,向炉气净化酸性污水的处理系统中补入适量新鲜水,继续进行酸性污水的循环处理。
实施本发明污水处理方法的关键设备为膜过滤器。本发明所选用的膜过滤器为多孔过滤筒形式的过滤器,由筒体和过滤元件组成,过滤元件为至少一个或多个多孔过滤筒,由花板固定在膜过滤器筒体的中部;筒体中部设有待处理污水-浊液进口,筒体上部设有清液出口,膜过滤器底部设有分离出泥渣出口。
过滤元件多孔过滤筒的外面套有聚烯烃滤膜为过滤材料,该膜的特点是膜断面形态的不对称性,由表面层与大孔支撑层两层组成;表面层很薄,厚度0.1-1.5μm,孔径3-5微米,表面光滑疏水;支撑层呈多孔状,厚度为50-250μm,起支撑作用,它决定膜的机械强度。
在进行过滤操作之前,需对过滤膜进行预涂处理,预涂处理采用的预涂材料为硅藻土、粉煤灰及硫酸钙的组合物,其重量配比为硅藻土∶粉煤灰∶硫酸钙=20∶75∶5,其自然形成的粒度为5-250微米,比表面积300-360cm2/g。
所说的预涂步骤是在每一次循环运行周期开始时进行的,其操作步骤如下:
首先在预涂槽中,将预涂料与清水按20∶80重量比例配制成预涂液,同时用空气搅拌防止沉淀,系统开机时用泵将该预涂液自污水进口送人过滤器,对过滤膜预涂15~20秒钟,然后关闭预涂液进料阀,开启污水进料阀,自动切换至常规污水循环过滤处理流程。
当过滤器阻力达到0.21~0.23Mpa时,即需中止过滤过程,进行反冲操作,自动关闭污水进液阀门的同时打开底部排污阀门,迅速使清液返流,将滤饼和预涂料全部从滤膜表面脱落。
反冲洗后脱落的滤渣-泥渣用泥浆泵打入板框压滤机压滤后,滤饼送渣场,滤液送回污水缓冲池;然后,补充新鲜水,开始新的炉气净化酸性污水处理的循环。
本发明所述炉气净化酸性污水的处理方法的具体操作工艺条件如下:
预涂时间:15-20秒
过滤压力:0.15-0.23Mpa
送干吸工段清液酸度:10-15%(以H2SO4重量%计)
本发明所述炉气净化酸性污水处理循环过程中,所得的清液中含固量为:悬浮物(ss)<20mg/l。
本发明采用系统内直接过滤,当循环清液和补充的水经循环使用和过滤后,酸度达到要求即送去干吸工段配酸,所有清液均全部回用,实现了污水零排放。
而现有各硫酸厂酸洗流程污水排放量大致在1-1.2吨/吨酸,水洗流程污水排放量大至15-20吨/吨酸,部分污水循环流程污水排放量大至12.8吨/吨酸。
本发明采用聚烯烃滤膜材料过滤分离溶液中的大分子、胶体微粒介质,该高分子聚合滤膜耐酸、强度高,孔径3-5微米,表面光滑疏水,在污水过滤后反冲时脱饼性能更好,并对污水胶质分离性能较好。新型膜坚韧耐磨,过滤中的坚硬物质和反冲压力对滤膜损伤不影响使用。
与传统的戈尔膜不同,由于戈尔膜是复合在布表面的一层膜,不能在酸性条件下过滤,需中和后过滤,使得流程长、操作复杂、投资高。且酸水中的杂质不能溶解,堵塞膜内部,部分胶体粘结在表面堵塞。
传统的滤布孔径大,过滤精度不够,且胶体堵塞后不易脱落,造成更换频繁,劳动强度大,不能连续生产。
本发明所选用的预涂材料中的活性SiO2、活性Al2O3和f-CaO(游离氧化钙)都是活性的有效成分,它对胶凝体的形成是有利的。由于其粒度细,比表面积大,附着在膜的表面,从而杜绝单质硫和煤焦油等粘性物质与膜直接接触,提高过滤性能,在污水过滤后反冲时脱饼性能更好,并且达到长期运行;该预涂材料的价格低廉,有利于降低处理成本。
本发明运行成本低,低于0.2元/立方污水;而传统法为0.50元/立方污水。
本发明占地少,仅为传统法污水处理的10%。
本发明还具有投资小、自动化程度高等特点。
本发明达到了污水零排放,实现了节能减排,降低了生产成本,保护了环境,对石膏制酸的推广具有更大的重要意义。