申请日2016.08.29
公开(公告)日2016.12.14
IPC分类号C02F9/14
摘要
本发明涉及一种基于射流生化反应器的焦化废水处理方法,包括气浮预处理、前置反硝化处理、生化反应器处理、脱气处理、后置反硝化处理以及超滤处理、反渗透/纳滤处理。本发明整体流程设计合理,采用生化处理工艺和膜深度处理工艺结合,通过外置式超滤截留活性污泥,与前置反硝化处理、生化反应器以及后置反硝化处理工艺A/O/A共同构成MBR工艺,能提高处理系统的有机容积负荷,组合工艺处理效果好,投资和运行成本较低,出水可达到回用标准,投资和运行成本较低。
摘要附图
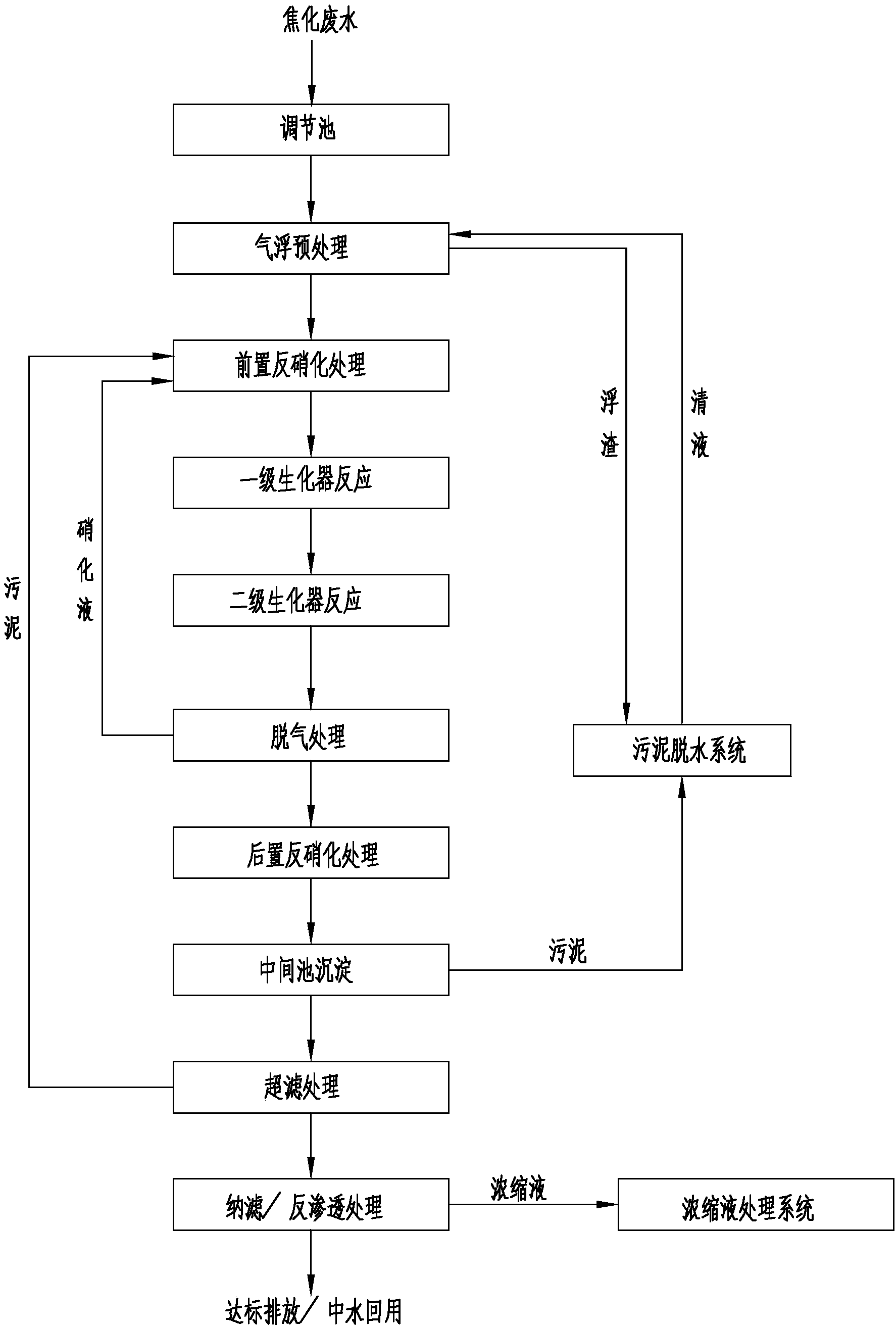
权利要求书
1.一种基于射流生化反应器的焦化废水处理方法,其特征在于:按以下步骤进行:
⑴、气浮预处理:将调节池内的焦化废水通入气浮机中,将焦化废水中的油脂、胶状物以及固体悬浮物在气浮机中形成水-气-颗粒三相混合体系,对分离后的出水送至前置反硝化池内、浮渣送至污泥脱水系统,处理后焦化废水中的油类和SS去除率≥90%,COD去除率≥10%;
⑵、前置反硝化处理:将气浮处理后的出水送至前置反硝化池内与回流的硝化液和污泥充分混合,通过焦化废水原水内的BOD及污泥中的碳源对焦化废水中的有机质进行反硝化,污泥浓度控制在15~30g/L,溶解氧浓度≤0.5mg/L;
⑶、生化反应器处理:
①、将前置反硝化处理的出水送至一级生化反应器内,经一级生化反应器内的循环泵将废水抽出并通过两相喷嘴连续射流喷入一级生化反应器,曝气活性污泥去除废水中的高浓度有机质,所述的活性污泥的优势菌为异养菌,一级生化反应器的水力停留时间控制在3.5~4.5h,污泥浓度为15~30g/L,溶解氧控制在2~8mg/L,COD去除率在85~95%,挥发酚去除率≥99%,氰化物去除率在85~95%;
②、将一级生化反应处理后的出水送入二级生化反应器内,经二级生化反应器内的循环泵将废水抽出并通过两相喷嘴连续射流喷入二级生化反应器,曝气活性污泥对废水进行硝化反应,将氨氮转化为硝态氮,所述活性污泥的优势菌为氨氮自养菌,二级生化反应器的水力停留时间控制在7~9h,二级生化反应器的污泥浓度的控制在15~30g/L,溶解氧控制在2~8mg/L;氨氮去除率≥95%;
⑷、脱气处理:将生化反应器反应后的出水送入脱气池内,通过膜盘曝气对剩余氨氮继续硝化,使活性污泥在脱气池内在悬浮状态下脱气,溶解氧浓度≤0.5mg/L,脱气池中的硝化液回流至前置反硝化池,且硝化液的回流比在100~300%;
⑸、后置反硝化处理:将脱气池的出水送至后置反硝化池中,向后置反硝化池内投加外来碳源,对废水中剩余硝氮进行反硝化反应并转化为氮气,污泥浓度为15~30g/L,溶解氧浓度≤0.5mg/L,后置反硝化的出水送至中间池进行沉淀,中间池的上清液送至外置式超滤器、底部的污泥送污泥脱水系统,中间池的水力留时间为3~5h,中间池的污泥浓度在15~30g/L;
⑹、超滤处理:将中间池的出水送至外置式超滤器内,通过外置式超滤器的膜组件对泥水混合物进行固液分离,清液送入反渗透膜组件或纳滤膜组件,污泥回流到前置式硝化池内;
⑺、反渗透或纳滤器处理:将超滤后清液送入反渗透膜组件或纳滤膜组件,通过反渗透膜组件或纳滤膜组件对清液中的有机污染物及盐分进行截留,处理后的浓缩液送浓缩液处理系统、输出中水回用或达标排放。
2.根据权利要求1所述的基于射流生化反应器的焦化废水处理方法,其特征在于:所述污泥脱水系统对污泥进行分离,清液回流至气浮机中,脱水后干泥填埋。
3.根据权利要求1所述的基于射流生化反应器的焦化废水处理方法,其特征在于:所述气浮预处理时,向气浮机投加投加混凝剂和絮凝剂,按质量百分比,混凝剂的加入量是焦化废水总量的0.001~0.01%,絮凝剂的加入量是焦化废水总量的0.005~0.015%。
4.根据权利要求1所述的基于射流生化反应器的焦化废水处理方法,其特征在于:所述前置反硝化处理中,反硝化速率在0.09~0.12kg NO3-N/kg VS.d,反硝化负荷在0.9~1.2kg NO3-N/m3.d。
5.根据权利要求1所述的基于射流生化反应器的焦化废水处理方法,其特征在于:所述后置反硝化处理中,后置反硝化速率在0.12~0.2kg NO3-N/kg VS.d,后置反硝化负荷在1.2~1.5kg NO3-N/m3.d。
6.根据权利要求1所述的基于射流生化反应器的焦化废水处理方法,其特征在于:所述一级生化反应器和二级生化反应器为喷射环流生化反应器,循环泵流量为进水流量在300~1000%,喷嘴瞬时流速为40~50m/s,一级生化反应器的COD容积负荷≥16kg COD/m3.d,二级生化反应器氨氮容积负荷为1.2~1.5kg NH4-N/m3.d。
说明书
基于射流生化反应器的焦化废水处理方法
技术领域
本发明涉及一种基于射流生化反应器的焦化废水处理方法,属于工业废水处理技术领域。
背景技术
煤化工企业在炼焦、制气等生产过程中,排放大量成分复杂、有机浓度高、难降解的焦化废水。焦化废水主要含有氰化物、硫氰化物、氨氮、重金属等无机污染物和油类、挥发酚、多环芳烃等有机污染物。我国于2012年颁布了《炼焦化学工业污染物排放标准》(GB16171-2012),对焦化废水处理和排放提出了较高的要求,对有机污染物和氮类排放控制更加严格。其规定自2015年1月1日起,污染排放限值为:COD<80mg/L,氨氮<10mg/L,总氮<20mg/L,挥发酚<0.3mg/L,硫化物<0.5mg/L,氰化物<0.2mg/L。焦化废水处理工艺主要包括物理法、化学法和生化法。目前,应用生化处理技术应用最为广泛,但单一的生化处理工艺往往难以保证处理效果。
为保证脱氨效果,目前焦化废水生化处理单元多采用采用硝化/反硝化为核心的生物脱氮工艺,主要通过缺氧(或厌氧)/好氧组合法实现,常见组合工艺包括A/O法、O/A/O法、A/O/O法等等。但上述工艺在实际工程中存在如下问题:
⑴、出水不达标。
采用上述生化组合处理方法对焦化废水进行处理时,焦化废水对进水营养物的要求一般为C:N:P=100:5:1。而焦化废水中酚含量较高,因此COD(化学需氧量)浓度偏高;而氨氮浓度取决于前段蒸氨工艺运行稳定性,一般变化幅度较大,难以达到上述比例。如果进水COD浓度高,好氧反应器中的优势菌为异养菌,抑制了自养硝化菌的生长。另外,进水中的生物抑制剂也会影响硝化菌的活性,造成脱氮效率下降,出水化学需氧量COD、氨氮、总氮难以同时达标。
⑵、氧传递效率低、曝气系统能耗高。
在曝气技术评价指标中,氧传递效率是一个非常重要的评价指标,它决定了单位充氧量的能耗。目前,焦化废水处理厂大部分采用微孔曝气技术,如微孔曝气管和曝气膜盘。其氧传递效率只有5%~20%,需要配套大功率的风机,曝气工艺能耗约占处理厂总能耗的50~70%。另外,微孔曝气器数量较多,更换、维护成本较高。
⑶、有机负荷低,占地面积大。
普通活性污泥法容积负荷一般小于1.0kg BOD5/m3·d,需要大体积的曝气池方可满足处理要求。
⑷、深度处理难度大。
膜深度工艺即纳滤(NF)和反渗透(RO)组合对进水水质有严格要求,生化出水水质恶劣,会造成膜污染加剧,频繁洗膜、换膜,增加运行成本。
因此如CN101913728A公开的一种《焦化废水生化处理方法》,该方法包括对焦化废水进行预处理、将预处理后的焦化废水送入厌氧池进行厌氧处理、将经厌氧处理后的废水送入好氧三相流化床进行好氧处理等步骤,其利用厌氧处理和好氧三相流化床处理焦化废水,该方法无硝化液回流,难以保证总氮达标排放。其次,由于利用上流式厌氧污泥床反应器、缺氧载体流化床生物膜反应器、两级好氧载体流化床生物膜反应器处理焦化废水,但其容积负荷和污泥负荷较低,反应器体积较大,投资成本高。而CN102897979A公开的《一种焦化废水的处理方法》,它包括焦化废水的生化处理和焦化废水的深度处理工艺;焦化废水的生化处理采用A2O工艺,焦化废水深度处理采用内电解+Fenton氧化混凝沉淀+活性炭吸附法,未说明氧化段采用何种反应器和曝气方式,且深度处理工艺简单,难以保证处理效果。
发明内容
本发明的目的是提供一种运行稳定,投资成本低,出水达标的基于射流生化反应器的焦化废水处理方法。
本发明为达到上述目的的技术方案是:一种基于射流生化反应器的焦化废水处理方法,其特征在于:按以下步骤进行:
⑴、气浮预处理:将调节池内的焦化废水通入气浮机中,将焦化废水中的油脂、胶状物以及固体悬浮物在气浮机中形成水-气-颗粒三相混合体系,对分离后的出水送至前置反硝化池内、浮渣送至污泥脱水系统,处理后焦化废水中的油类和SS去除率≥90%,COD去除率≥10%;
⑵、前置反硝化处理:将气浮处理后的出水送至前置反硝化池内与回流的硝化液和污泥充分混合,通过焦化废水原水内的BOD及污泥中的碳源对焦化废水中的有机质进行反硝化,污泥浓度控制在15~30g/L,溶解氧浓度≤0.5mg/L;
⑶、生化反应器处理:
①、将前置反硝化处理的出水送至一级生化反应器内,经一级生化反应器内的循环泵将废水抽出并通过两相喷嘴连续射流喷入一级生化反应器,曝气活性污泥去除废水中的高浓度有机质,所述的活性污泥的优势菌为异养菌,一级生化反应器的水力停留时间控制在3.5~4.5h,污泥浓度为15~30g/L,溶解氧控制在2~8mg/L,COD去除率在85~95%,挥发酚去除率≥99%,氰化物去除率在85~95%;
②、将一级生化反应处理后的出水送入二级生化反应器内,经二级生化反应器内的循环泵将废水抽出并通过两相喷嘴连续射流喷入二级生化反应器,曝气活性污泥对废水进行硝化反应,将氨氮转化为硝态氮,所述活性污泥的优势菌为氨氮自养菌,二级生化反应器的水力停留时间控制在7~9h,二级生化反应器的污泥浓度的控制在15~30g/L,溶解氧控制在2~8mg/L;氨氮去除率≥95%;
⑷、脱气处理:将生化反应器反应后的出水送入脱气池内,通过膜盘曝气对剩余氨氮继续硝化,使活性污泥在脱气池内在悬浮状态下脱气,溶解氧浓度≤0.5mg/L,脱气池中的硝化液回流至前置反硝化池,且硝化液的回流比在100~300%;
⑸、后置反硝化处理:将脱气池的出水送至后置反硝化池中,向后置反硝化池内投加外来碳源,对废水中剩余硝氮进行反硝化反应并转化为氮气,污泥浓度为15~30g/L,溶解氧浓度≤0.5mg/L,后置反硝化的出水送至中间池进行沉淀,中间池的上清液送至外置式超滤器、底部的污泥送污泥脱水系统,中间池的水力留时间为3~5h,中间池的污泥浓度在15~30g/L;
⑹、超滤处理:将中间池的出水送至外置式超滤器内,通过外置式超滤器的膜组件对泥水混合物进行固液分离,清液送入反渗透膜组件或纳滤膜组件,污泥回流到前置式硝化池内;
⑺、反渗透或纳滤器处理:将超滤后清液送入反渗透膜组件或纳滤膜组件,通过反渗透膜组件或纳滤膜组件对清液中的有机污染物及盐分进行截留,处理后的浓缩液送浓缩液处理系统、输出中水回用或达标排放。
本发明焦化废水处理方法的生化处理工艺采用气浮预处理、前置反硝化处理、生化反应器处理以及脱气处理和后置反硝化处理组合工艺,通过气浮预处理去除焦化废水中的胶状物以及固体悬浮物,减轻后续处理段的负荷,使后续处理工艺能稳定运行。通过前置反硝化处理进行脱氮处理,能对高有机浓度的焦化废水得到充分稀释,且能利用焦化废水中原水的BOD进行反硝化,并将纳滤的污泥以及脱气处理后的硝化液回流到前置式硝化池内作为碳源,对焦化废水中的有机质能进行充分反硝化,达到脱氮的目的,能减少外加碳源的投加,降低了处理成本。本发明生化反应器处理采用两级生化反应器,通过生化反应器内的循环泵及两相喷嘴连续射流,进行高速喷嘴射流曝气,增加了空气、活性污泥和废水之间的接触反应面积,使得活性污泥与废水进行充分反应,通过生化反应器的高充氧的曝气活性污泥去除废水中的高浓度有机质,去除焦化废水中的COD及氨氮。本发明采用喷射环流生化反应器,有机负荷高,能提高微生物反应效率和氧利用率,污泥产量低,同时生化反应器占地面积小,保证硝化反应稳定进行。本发明通过脱气处理能避免因生化反应器中的活性污泥处于高充氧状态,使硝酸盐混合液回流至前置反硝化池时造成池内溶氧过高,而影响反硝化效果的问题,经后置反硝化处理,解决了焦化废水中可应用于反硝化的易降解碳源含量不稳定,使反硝化脱氮效果难以保证的问题。本发明通过前置反硝化和后置反硝化进行脱氮处理,能充分保证了脱氮效果,使得出水总氮可稳定达标。本发明膜深度处理工艺采用超滤处理以及反渗透或纳滤处理,通过外置式超滤截留活性污泥,无需专门的膜池,减少了占地面积,并且清洗、维护较为方便,经反渗透或纳滤作为膜深度处理工艺,出水水质较高,能够稳定达中小回用或达标排放。本发明整体处理工艺设计合理,采用了高效生化器处理工艺和膜深度处理工艺结合,通过外置式超滤截留活性污泥,与前置反硝化处理、生化反应器以及后置反硝化处理工艺A/O/A共同构成MBR工艺,在MBR工艺中,各生化反应池内污泥浓度均可控制在15~30g/L,提高处理系统的有机容积负荷,组合工艺处理效果好,投资和运行成本较低。