申请日2015.09.10
公开(公告)日2016.04.27
IPC分类号C02F9/06
摘要
本实用新型公开了一种含毒挥发性气体高浓度工业废水的处理系统,包括隔离式多相均衡气浮装置、引气旋流发生器和双相循环催化氧化装置;双相循环催化氧化装置包括依次连通的pH调节槽、电解氧化槽、中和槽、絮凝槽和沉淀槽;隔离式多相均衡气浮装置的废气输出口和处理水输出口分别与上述引气旋流发生器和pH调节槽连通。本实用新型提供的含毒挥发性气体高浓度工业废水的处理系统能提高废水的可生化性,能降低废水中恶臭类物质的含量,也能削减废水的毒性,还能降低废水的COD和消除色度,且还具有有效防止有毒气体外逸和防止爆炸等危险发生、安全系数高、可防止废气无组织排放和能对废气进行有效处理的优点,从而避免造成二次污染,成本低。
摘要附图
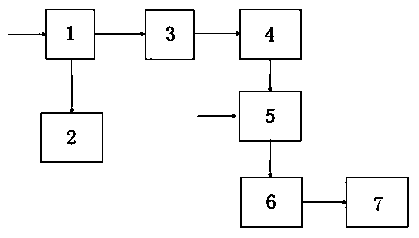
权利要求书
1.一种含毒挥发性气体高浓度工业废水的处理系统,其特征在于,包括隔离式多相均衡气浮装置、引气旋流发生器和双相循环催化氧化装置;
所述双相循环催化氧化装置包括依次连通的pH调节槽、电解氧化槽、中和槽、絮凝槽和沉淀槽;
所述隔离式多相均衡气浮装置的废气输出口和处理水输出口分别与所述引气旋流发生器和pH调节槽连通。
2.根据权利要求1所述的含毒挥发性气体高浓度工业废水的处理系统,其特征在于,所述双相循环催化氧化装置还包括电解反应槽,且所述电解反应槽设置在所述电解氧化槽的排出口和输入口之间。
3.根据权利要求1所述的含毒挥发性气体高浓度工业废水的处理系统,其特征在于,所述沉淀槽为斜板式沉淀槽、竖流式沉淀槽或辐流式沉淀槽。
说明书
一种含毒挥发性气体高浓度工业废水的处理系统
技术领域
本实用新型涉及工业废水处理领域,尤其涉及一种含毒挥发性气体高浓度工业废水的处理系统。
背景技术
目前,含毒挥发性气体高浓度工业废水是指含有大量硫化物、硫醇、氨等挥发性气体的废水,COD含量高达2-10万mg/L,其中特征污染物主要是含苯环、杂环类物质,具有溶解氧低、毒性大、可生化性极差等特点,其污染问题一直是废水处理工程中亟待解决的问题。为了彻底解决含毒挥发性气体高浓度工业废水污染环境的问题,急需开发出适合此类废水的处理高效、低成本、不产生二次污染的工艺技术。目前对于含毒挥发性气体高浓度工业废水处理常用的方法是:萃取法、焚烧法、常规氧化还原法等,这几种方法对于高浓度废水普遍存在成本高、不能长周期稳定运行、难以满足进一步生化要求等问题。
萃取法由有机相和水相相互混合,水相中要分离出的物质进入有机相后,再靠两相质量密度不同将两相分开。萃取法广泛应用于冶金和化工行业中,尤其对高浓度有机物分离具有一定的处理效果,但是对于成分复杂的废水,尤其是单种有机物浓度低时,给分离增加难度,需对萃取液进行二次处理,增加了投资及运行成本;同时,废水中引入萃取剂,易造成二次污染。
焚烧法对于超高浓度废水(COD>20万mg/L)的处理有较大优势,适合水量小、浓度极高的废水处理,但同时焚烧过程中容易产生二次污染。
常规氧化还原法分为湿式氧化法(WAO)和超临界湿式氧化法,这类方法主要是高温、高压下将废水中有机物氧化成二氧化碳和水,从而达到污染物降解目的,该类方法处理效率高,范围广,但高温、高压不仅使得投资运行成本高,而且会带来安全隐患,尤其在石化行业里高温、高压条件会限制该技术应用推广。
发明内容
本实用新型要解决的技术问题在于,针对现有技术的上述缺陷,提供一种能提高废水的可生化性、能大大降低高浓度工业废水中硫化物和硫醇等恶臭类物质的含量、能削减工业废水的毒性、能降低工业废水的COD和消除色度、可有效防止挥发性有毒气体外逸和防止空气进入引发爆炸等危险发生、安全系数高、可以防止废气无组织排放、能对废气进行有效处理、可避免造成二次污染且成本低的含毒挥发性气体高浓度工业废水的处理系统。
本实用新型为解决上述技术问题,其所采用的技术方案如下:
一种含毒挥发性气体高浓度工业废水的处理系统,包括隔离式多相均衡气浮装置、引气旋流发生器和双相循环催化氧化装置;
上述双相循环催化氧化装置包括依次连通的pH调节槽、电解氧化槽、中和槽、絮凝槽和沉淀槽;
上述隔离式多相均衡气浮装置的废气输出口和处理水输出口分别与上述引气旋流发生器和pH调节槽连通。
在本实用新型所述含毒挥发性气体高浓度工业废水的处理系统中,pH调节槽中配有搅拌装置,使得第一处理水能够与酸液或碱液充分接触,加速对第一处理水进行pH调节。
上述电解氧化槽用于对第一处理水中的有机物进行催化氧化,且该电解氧化槽为不锈钢密闭电解氧化槽,这样的设计不仅有助于增强电解氧化槽的耐腐蚀性能,有益于延长该电解氧化槽的使用寿命,而且还可以防止挥发性物质逸出,保证催化氧化的效果,并能避免外界环境对催化氧化造成不利影响。另外,该电解氧化槽内设有电解阳极和电解阴极,该电解阳极为DSA钛板,电解阴极为不锈钢板。
上述中和槽用于对上述第二处理水进行加碱液调节pH值,并将第二处理水的pH值调节为6~9,以便获得第三处理水,为后续的杂质沉淀工序做好准备,如若第三处理水的pH值小于6,则第三处理水偏酸性,不利于杂质沉淀,如若第三处理水的pH值大于9,则会造成无谓的资源浪费,不利于成本的降低。
上述絮凝槽中设有搅拌桨,以在絮凝过程中进行搅拌,从而提高第三处理水的传质速率,从而增强反应效果;该搅拌桨采用桨叶式搅拌桨、框式搅拌桨或锚式搅拌桨。
上述隔离式多相均衡气浮装置还设有智能加剂模块、气浮模块和气体安全保护模块;其中,智能加剂模块,当废水经过静态混合器时,通过该智能加剂模块向静态混合器中添加混凝剂,使得废水与混凝剂在静态混合器中充分混合,这样避免了采用人工添加混凝剂,有助于减弱工作人员的劳动强度;气浮模块,会使得加药后的废水与多相流溶气泵产生的溶气水充分接触,利用将其中油类及不溶性有机物浮至水面;气体安全保护模块,该气体安全保护模块采用氮气作为气源,可以阻止该隔离式多相均衡气浮装置内的硫化氢、氨等有毒及挥发性气体外逸出,防止二次污染产生,又能防止该隔离式多相均衡气浮装置外部的氧气进入其中,从而避免带来安全隐患。
作为对本实用新型所述含毒挥发性气体高浓度工业废水的处理系统的一种改进,上述双相循环催化氧化装置还包括电解反应槽,且该电解反应槽设置在上述电解氧化槽的排出口和输入口之间。电解反应槽的设置使得从电解氧化槽中流入电解反应槽中的尚未充分氧化的混合物料回流到电解氧化槽中进行二次催化氧化,使得第一处理水中的有机物被充分氧化分解,从而保证对工业废水的处理效果和出水水质。
优选地,上述沉淀槽为斜板式沉淀槽、竖流式沉淀槽或辐流式沉淀槽。
利用上述含毒挥发性气体高浓度工业废水的处理系统对废水进行处理的处理工艺,包括如下工艺步骤:
步骤S1:将废水输送至隔离式多相均衡气浮装置中以将废水中的油类及非溶性有机物带至水面,并将带至水面的油类及非溶性有机物去除且获得第一处理水和废气;
步骤S2:由步骤S1获得的废气经引气旋流发生器处理后达标排放;
步骤S3:将由步骤S1获得的第一处理水输送至双相循环催化氧化装置中以对第一处理水中的有机物进行催化氧化并获得符合要求的排出水。
在上述步骤S1中,废水首先在静态混合器中与混凝剂充分混合后再输送至上述隔离式多相均衡气浮装置中,这样的设计可以去除废水中的油类和悬浮物,降低了后续催化氧化的运行成本,能够保证后续处理工艺的稳定运行。
在上述步骤S1中,上述隔离式多相均衡气浮装置为专利权人为南京中衡元环保设备有限公司、专利号为ZL201210072393.8的专利文件中所述的专利技术,利用该隔离式多相均衡气浮装置将废水中的油类及非溶性有机物带至水面并将油类及非溶性有机物去除,不仅可以有效防止挥发性有毒气体外逸和防止空气进入引发爆炸等危险发生,安全系数高,而且还能保证出水水质,有利于降低膜污染。
在上述步骤S2中,上述引气旋流发生器为专利权利人为南京中衡元环保设备有限公司、专利号为ZL201320592932.0的专利文件中所述的专利技术,采用该引气旋流发生器对废气进行收集、处理,有效防止了废气的无组织排放,并对废气进行了有效处理,使得其满足达标排放要求。
在上述步骤S3中,上述双相循环催化氧化装置为专利权利人为南京中衡元环保设备有限公司、专利号为ZL201210379268.1的专利文件中所述的专利技术,在本实用新型所述技术方案中,利用该双相循环催化氧化装置对第一处理水中的有机物进行催化氧化,该双相循环催化氧化装置能将工业废水中的难降解、抑制性物质分解为易生化的小分子物质,提高了工业废水的可生化性,大大降低了高浓度工业废水中硫化物和硫醇等恶臭类物质的含量,也大幅削减了工业废水的毒性,还有助于降低工业废水的COD和消除色度,降低了二次污染。
上述双相循环催化氧化装置在进行催化氧化时,利用H2O2作为氧化剂,与电解还原产生的Fe2+作为催化剂,并经由特殊的氧化还原反应生产羟基自由基(OH),羟基自由基(OH)是一强氧化剂,故可将有机物氧化分解。其主要反应式如下所示:
具体反应式如下:
阳极上的反应,主要包括水的解离和有机物的氧化:
2H2O→O2+4H++4e-
Fe2+→Fe3++e-
Organics+O2→CO2+H2O
阴极上的反应,主要包括水的解离和和三价铁的还原:
Fe3++e-→Fe2+
2H2O+2e-→H2+2OH-
2O2+6H++6e-→2H2O+H2O2
水溶液相的反应,主要包括双氧水的催化和有机物的分解反应:
H2O2+Fe2+→OH+OH-+Fe3+
H2O2+Fe3+→Fe2++H++HO2
RH+OH→H2O+R
Fe2++OH→Fe3++OH-
R+Fe3+→Fe2++Products
R+OH→ROH
R+H2O2→ROH+OH
HO2+Fe3+→O2+Fe2++H+
OH+H2O2→HO2+H2O
而主要反应如下式所示,将有机物氧化成二氧化碳和水:
H2O2+Fe2++有机物→CO2+H2O+Fe3+
从上式可看出有机物被氧化成二氧化碳和水的同时,Fe2+催化剂也变成了Fe3+,故利用电解还原的方法使Fe3+在阴极再还原为Fe2+催化剂,此即为双相循环催化氧化,实现了Fe2+和Fe3+的双相循环,有效节省了FeSO4的用量,提高了催化氧化的效率;由阴极的反应式可看出Fe3+还原成Fe2+,与另一种利用牺牲阳极铁来产生Fe2+催化剂的方法比较,牺牲阳极铁每产生1摩尔Fe2+需2摩尔电量,而本实用新型所述技术方案中仅需1摩尔电量,且不断将Fenton法产生的Fe3+还原成Fe2+重复再利用,因此可大幅的降低阳极金属铁的消耗量及电的消耗量以及最终的污泥产量;再者,H2O2直接添加于双相循环催化氧化装置并与电解产生的Fe2+及废水中的有机物反应,而反应产生的Fe3+又可直接于阴极还原成Fe2+并源源不断的参与反应,使得H2O2的氧化效率提高,降低H2O2的加药量及降低操作成本;此外,在阳极发生的电极氧化作用亦可将有机物之一部份去除。由此可知,本实用新型所述含毒挥发性气体高浓度工业废水的处理工艺不仅提升了传统催化氧化的处理效果,而且进一步降低了催化剂的使用量,减少Fe3+产生的污泥量并大大降低运行费用,也有效地将其中有害的有机物转化为无害的且易于降解的物质,提高了废水的可生化性。
在上述步骤S1中,上述废水在隔离式多相均衡气浮装置中的废水停留时间t1为10~30min。在该步骤S1中,将废水停留时间t1限制为10~30min,一方面,能更好地将废水中的油类及非溶性有机物带至水面并去除,另一方面,能更好地将废水中的COD去除率提高到10~40%,还能更好地将废水中的VOC的去除率提高到80~90%,如若t1小于10min,则不仅会影响去除废水中的油类及非溶性有机物,而且还影响到废水中的COD和VOC,如若t1大于30min,则会造成无谓的资源浪费,不利于成本的降低。
在上述步骤S3中,在对第一处理水中的有机物进行催化氧化之前先对第一处理水进行pH值调节,并将第一处理水的pH值调节为3~5。
将该第一处理水的pH值调节为3~5,这样给双相循环催化氧化装置中进行催化氧化提供了比较有利的条件。
进一步地,在上述步骤S3中,在对第一处理水中的有机物进行催化氧化之后获得第二处理水,并在第二处理水中添加碱液以调节其pH值获得第三处理水。在第二处理水中添加碱液有助于对第三处理水进行后续杂质的沉淀工作,如若仍保持为酸性环境,则会在很大程度上影响到后续杂质的絮凝和沉淀。
更进一步地,在上述步骤S3中,在上述第三处理水中添加絮凝剂以将其中的杂质沉淀下来并获得污泥和符合要求的排出水。该絮凝剂为聚合硫酸铝铁、硫酸铁、聚合氯化铝铁或高分子絮凝剂;在絮凝过程中通过搅拌桨对第三处理水进行搅拌以提高传质速率,增强反应效果。
在获得污泥后,本实用新型采用离心脱水机、板框脱水机、叠螺脱水机、陀螺脱水机或带式脱水机对污泥进行脱水,优选叠螺脱水机,叠螺脱水机对于含油类的污泥具有很好的处理效果,且其自动化程度高,稳定性好,运行成本低,密闭性好,相比其它脱水机减少了恶臭排放,不会产生二次污染。
更进一步地,在上述步骤S3中,上述第一处理水在双相循环催化氧化装置中的水力停留时间t2为0.5~3h。将步骤S3中第一处理水的水力停留时间t2限制为0.5~3h,能保证双相循环催化氧化装置利用催化氧化对废水中的有机物进行充分降解,如若水力停留时间t2小于0.5h,则可能导致废水中的部分有机物没有降解,严重影响到了对废水的处理效果,如若水力停留时间t2大于3h,则会造成无谓的资源浪费,不利用成本的降低。
在该步骤S3中,第一处理水在双相循环催化氧化装置中于30oC~50oC、一个标准大气压时进行催化氧化,这样的设计使得催化氧化在常温、常压下进行,不仅可避免现有技术中高温高压氧化带来的安全隐患,而且有利于降低运行成本,另外,还扩大了本实用新型所述含毒挥发性气体高浓度工业废水的处理工艺的应用领域和应用范围。
另外,在该步骤S3中,Fe2+与H2O2的摩尔比为1:1~1:5。
在本实用新型所述技术方案中,凡未作特别说明的,均可通过采用本领域中的常规手段来实现本技术方案。
因此,本实用新型的有益效果是提供了一种含毒挥发性气体高浓度工业废水的处理系统,该处理系统能提高废水的可生化性,能大大降低高浓度工业废水中硫化物和硫醇等恶臭类物质的含量,也能削减工业废水的毒性,还能降低工业废水的COD和消除色度,且还具有可有效防止挥发性有毒气体外逸和防止空气进入引发爆炸等危险发生、安全系数高、可防止废气无组织排放和能对废气进行有效处理的优点,从而避免造成二次污染,成本也大幅降低。