申请日2015.12.04
公开(公告)日2016.04.27
IPC分类号C02F9/06; C02F1/461; C02F1/469; C02F103/34
摘要
本发明公开了一种PCB含氨氮废水零排放处理方法及装置,其特征在于,包括以下步骤:将蚀刻水洗废水调整pH值至8~11,经过粗滤、超滤后,利用电极板间距D≤3CM的电极,电流密度为1-3ADS的电解系统电解滤液I,产生的气体用碱性蚀刻液吸收;电解后的滤液经过超滤系统处理,得到滤液II,回用。本发明通过调整极板的距离改变电解产物在电极板间的局部浓度,使阳极产生的氯气因局部过浓以气态逸出来实现对氨氮和Cl-的同步去除,最终使处理后出水符合蚀刻水洗水技术要求,满足工业回用水而实现零排放。
摘要附图
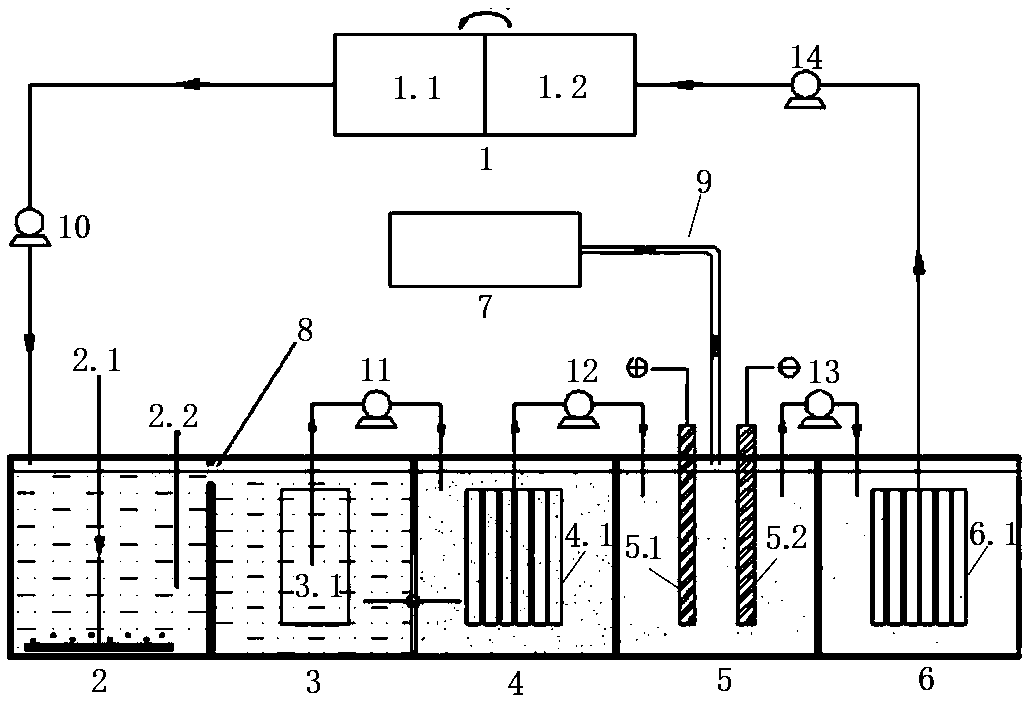
权利要求书
1.一种PCB蚀刻过程含氨氮废水零排放处理方法,其特征在于,包括以下步骤:
(1)调pH值:搅拌待处理的蚀刻水洗废水,调整pH值至8~11,以促使氨能以氨水合物NH3·H2O的形式存在;
(2)超滤:废液经过超滤处理,得到滤液I;
(3)电解:利用极密集的阴阳极板间距离改变电解产物在电极板间的局部浓度,使Cl-在阳极板放电产生的氯气因局部过浓以气态逸出而不是溶入水中,同时铵根离子也以氨水合物NH3·H2O的形式在阳极氧化为氮气而去除,从而使氨氮和Cl-同步去除,实现蚀刻水洗废水中氨、氯离子的同时去除,所述极密集电极极板间距D≤3CM,电流密度为1-3ADS,电解系统电解滤液I后,产生的含氨、氯气体经收集并回到蚀刻机内的喷淋系统,做为蚀刻的有益成份回到蚀刻液中;
(4)超滤:电解后的滤液经过超滤处理进一步去除铜离子,得到去除了氨氮、氯、铜离子并且不增加其它离子污染的滤液II,回用于蚀刻水洗,实现零排放。
2.根据权利要求1所述的PCB含氨氮废水零排放处理方法,其特征在于,步骤(2)超滤前进行粗滤,将调整好pH值的废水通过滤袋过滤,得到粗滤液。
3.根据权利要求1所述的PCB含氨氮废水零排放处理方法,其特征在于,步骤(2)超滤前进行粗滤,将调整好pH值的废水中加入絮凝剂,通过滤袋过滤,所述的絮凝剂为PAC、PAM或PFC,加入量为1-100mg/L。
4.一种用于PCB含氨氮废水零排放处理的装置,其特征在于,包括蚀刻水洗缸(1)、pH调整槽(2)、粗滤槽(3)、超滤槽I(4)、电解槽(5)、超滤槽II(6)、集气罐(7)。
5.根据权利要求4所述的装置,其特征在于,所述的蚀刻水洗缸(1)通过水泵(10)与pH调整槽(2)连接,所述的pH调整槽(2)内设置有搅拌装置(2.1)和pH计(2.2),pH调整槽(2)与粗滤槽(3)通过槽体上部的溢流口(8)连接,所述的粗滤槽(3)内设置有滤袋(3.1),滤袋(3.1)通过水泵(11)与超滤槽I(4)连接,所述的超滤槽I(4)内设置有超滤系统(4.1),超滤系统(4.1)通过水泵(12)与电解槽(5)连接,所述的电解槽(5)通过水泵(13)与超滤槽II(6)连接,电解槽(5)上部通过集气管(9)与集气罐(7)连接,所述的超滤槽II(6)内设置有超滤系统(6.1),超滤系统(6.1)通过水泵(14)与蚀刻水洗缸(1)连接。
6.根据权利要求4或5所述的装置,其特征在于,所述的电解槽(5)内设置有电极,电极板间距离D≤3CM。
7.根据权利要求6所述的装置,其特征在于,所述的电极包括一个阳极板(5.1)和一个阴极板(5.2)。
8.根据权利要求6所述的装置,其特征在于,当电极板间距离0.1CM≤D≤3CM,所述的电极包括一个阳极板(5.1)、一个阴极板(5.2)以及阳极板(5.1)与阴极板(5.2)之间设有一个或多个从电极板(5.3);当电极板间距离D﹤0.1CM,所述的电极包括一个阳极板(5.1)和一个阴极板(5.2)、以及两极板间设有一层透水性超滤膜或滤布(5.4)。
9.根据权利要求7或8所述的装置,其特征在于,当电极板间距离0.1CM≤D≤3CM,所述的阳极板(5.1)为钛涂铱钌合金或钛镀铂金催化剂不熔阳极,阴极板(5.2)为钛板,当电极板间距离D﹤0.1CM,所述的阳极板(5.1)为网状或多孔钛涂铱钌合金或钛镀铂金催化剂不熔阳极,阴极板(5.2)为网状或多孔结构钛板。
10.根据权利要求8所述的装置,其特征在于,所述的从电极板(5.3)的阳极侧(5.32)为钛基涂铱钌合金或钛镀铂金催化剂不熔电极,阴极侧(5.31)为钛板。
说明书
一种PCB含氨氮废水零排放处理方法及装置
技术领域
本发明涉及PCB废水处理的技术领域,尤其是一种PCB含氨氮废水零排放处理方法及装置。
背景技术
随着电子工业的高速发展,印制线路板的需求量越来越大,PCB的生产已成为电子行业的重要基础产业,而PCB工业废水污染也随着环保要求的提高越来越突出,其中含氨氮废水的处理已成为时下业界关注的热点。线路板含氨氮废水主要来源于蚀刻工序水洗水,该废水主要含氨氮、二价铜离子和氯离子。
零排放是工业生产最理想的结果,也是污水处理行业为之奋斗的终极目标。线路板蚀刻后水洗的目的是清洗掉板面残留的蚀刻液,通常蚀刻后面设一级水洗和二级水洗。其中一级水洗水均来源于二级水洗的溢流水,而一级水洗水即需要处理的水,经处理后的水再回用至二级水洗。通常一级水洗水的主要污染物及浓度见表1:
表1一级水洗水的主要污染物及浓度
污染物浓度(mg/L)NH<sub>3</sub>-N400~40000Cu<sup>2+</sup>100~10000Cl<sup>-</sup>>20000pH10~12
将一级水洗水处理后再回用于生产线二级水洗工序,按照满足清洗板面蚀刻液工业用水的最低要求,其水质需要达到表2的要求。
表2二级水洗水的主要污染物及浓度
污染物浓度(mg/L)NH<sub>3</sub>-N<10Cu<sup>2+</sup><3Cl<sup>-</sup><20000pH6~11
现有国内外对含氨氮废水的处理方法主要有折点加氯法;电化学直接、间接氧化法如中 国专利CN104787937A,公开了一种三维电极电解处理高浓度氨氮废水的方法,该方法引入粒子填料感应电极,大幅提高反应器电极的比表面积,在一个反应器内同时进行电解产生·OH以及Fenton试剂法产生·OH的两种反应,强氧化剂的供给可氧化高浓度氨氮,使废水达到良好的处理效果;膜组件蒸馏分离法,如中国专利CN204474484U,公开了一种氨氮废水的处理系统,使废水通过加热装置形成NH3气体,再利用膜蒸馏组件将NH3吸收,达到与废水分离的目的,解决了其它蒸馏技术占地面积大的问题,达到耗能低、无需建设水池和无二次污染的效果和生物脱氨法等,但从立足于零排放的目的分析,以上现有技术方法因为未能将水中的氯离子去除,均无法满足将氨氮、氯、铜同时去除且不引入新污染物的零排放要求。
折点加氯法:是在适当的pH范围向废水通入氯系氧化剂,将氨氮氧化为氯胺,进而氯胺分解为N2达到将氨氮去除,但该方法无法精确控制,实际操作均按过量处理,因此处理后的水含有大量Cl-,而且处理过程存在副产物二次污染,不适合零排放指标。
电化学直接或间接氧化法:是在含有大量氨氮的废水中添加或利用污水自有的Cl-,通过电解将氨在阳极直接氧化为N2而去除氨氮,同时利用阳极将Cl-氧化为Cl2,再利用活性Cl2与NH3反应生成N2和HCl的副反应间接氧化去除氨氮,间接的氧化反应后Cl-依然留在处理后的水中,不符合零排放指标。
膜组件蒸馏分离法:是利用高温情况下氨氮废水溢出NH3气体,再通过功能性膜组件将NH3吸收以去除氨氮。该方法最终Cl-还是没有从废水中去除,故也不适合零排放指标。
生物脱氨法:利用微生物降解脱氮,处理效率相对低,而且占地大,同时生物法也无法去除废水中的Cl-,不适合零排放指标。
综合分析以上现有技术原理,若以零排放和在线处理后直接回用为目标,现有技术均不能达到同时将氨氮和Cl-同时去除,因而都无法满足实现零排放和回用的要求。
蚀刻水洗水需处理的主要污染物为氨氮、Cu2+和Cl-,基于回用的目的,其中Cu2+处理工艺采用成熟的中和加沉淀法或超滤过滤法去除,本发明的重点内容是氨氮和Cl-的去除。
发明内容
针对现有技术存在的问题,本发明的目的是提供了一种含氨氮废水零排放处理方法及装置,该系统适应于PCB(印刷线路板)行业蚀刻段含氨氮废水的处理,利用循环再生技术对蚀刻水洗废水进行在线处理,实现处理后污染物零排放,处理后出水100%直接回用于蚀刻后水洗水的设备系统。
为了实现上述目的,本发明采用以下技术方案:
一种PCB含氨氮废水零排放处理方法,包括以下步骤:
(1)调pH值:搅拌待处理的蚀刻水洗废水,调整pH值至8~11,以促使氨能以氨水合物NH3·H2O的形式存在,通常蚀刻后水洗废水的pH值已经在8~11之间不需要调整;
(2)粗滤:根据实际需要可以进行粗滤,将经过步骤(1)调整好pH值的废水通过滤袋进行初步过滤,以除去废水中大部分铜离子,得到粗滤液;
(3)超滤:粗滤液经过超滤处理,除去废水中铜离子,得到滤液I;所述的超滤为本领域技术人员所熟知的膜分离方法;
(4)电解:利用电极板间距D≤3CM的电极,电流密度为1-3ADS的电解系统电解滤液I;电解系统在连续运行情况下,利用电解热效应即能将废水温度维持在40℃~60℃的范围内,电解过程将发生如下反应:
a.(在弱碱性环境下少部分水合物NH3·H2O以气态逸出)
b.NH3·H2O-e→N2↑+6H++H2O(在弱碱性环境下大部分NH3·H2O在带催化的阳极表面直接氧化为氮气逸出)
c.Cl--e→Cl2↑(在40℃~60℃温度条件下,利用极密集的极板间距离使Cl-在阳极板放电产生的氯气因局部过浓以气态逸出)
d.Cu2++e→Cu(废水中少量的Cu2+在阴极上以Cu单质析出)
利用碱性蚀刻液吸收电解产生的氨和氯气,做为蚀刻液的有益成份回到蚀刻系统中循环利用;
(5)超滤:电解后的滤液再经过超滤处理,得到澄清滤液II,回用。
优选的,步骤(2)的粗滤过程中,可以视实际需要向废水中加入絮凝剂。
进一步优选的,所述的絮凝剂为PAC、PAM或PFC,加入量为1-100mg/L。
PCB蚀刻废水通过上述完整技术方案的循环处理,完全可以满足回用水要求,且连续运行的体系不会出现离子积累,可以实现零排放的目标。
一种用于PCB含氨氮废水零排放处理的装置,包括蚀刻水洗缸1、pH调整槽2、粗滤槽3、超滤槽I4、电解槽5、超滤槽II6、集气罐7。
优选的,所述的蚀刻水洗缸1通过水泵10与pH调整槽2连接,所述的pH调整槽2内设置有搅拌装置2.1和pH计2.2,pH调整槽2与粗滤槽3通过槽体上部的溢流口8连接,所述的粗滤槽3内设置有滤袋3.1,滤袋3.1通过水泵11与超滤槽I4连接,所述的超滤槽I4内设置有超滤系统4.1,超滤系统4.1通过水泵12与电解槽5连接,所述的电解槽5通过水泵13与超滤槽II6连接,电解槽5上部通过集气管9与集气罐7连接,集气罐7中装有碱性蚀刻液,可以吸收电解产生的气体,所述的超滤槽II6内设置有超滤系统6.1,超滤系统6.1通过水泵14与蚀刻水洗缸1连接,其中蚀刻水洗缸1中分为一级水洗1.1和二级水洗1.2,其中一级水洗1.1的水均来源于二级水洗的溢流水,而一级水洗水即是本发明技术需要处理的水,经本发明处理后的水再回用至二级水洗。
优选的,所述的搅拌装置2.1为空气搅拌装置或机械搅拌装置,搅拌速度为5-60转/分钟。
优选的,所述的电解槽5内设置有电极,电极通过导线与电源连接,电极板间距离D≤3CM。
进一步优选的,所述的电极包括一个阳极板5.1和一个阴极板5.2。
进一步优选的,当0.1CM≤D≤3CM,所述的电极包括一个阳极板5.1、一个阴极板5.2、以及阳极板5.1与阴极板5.2之间设有一个或多个从电极板5.3,该电极结构的从电极个数是根据污水处理量的不同而设计的。
其中,阳极板5.1为钛涂铱钌合金或钛镀铂金催化剂不溶阳极,阴极板5.2为钛板,从电极板5.3的所有阳极侧5.32为钛基涂铱钌合金或钛镀铂金催化剂不溶电极,所有阴极侧5.31为钛板。
进一步优选的,当D﹤0.1CM,所述的电极包括一个阳极板5.1和一个阴极板5.2、以及两极板间设有一层透水性超滤膜或滤布5.4,其中,阳极板与阴极板间的距离等于超滤膜或滤布的厚度,其作用是防止阴阳极板相互接触造成短路,同时可以保证阳极产生的氯气和氮气能顺利逸出。其中阳极板5.1为网状或多孔钛涂铱钌合金或钛镀铂金催化剂不溶阳极,阴极板5.2为网状或多孔结构钛板。
本发明的核心内容
(1)铵根离子的转化:
PCB废水中氨氮通常以游离NH3和NH+的形式存在,本发明通过将废水调至弱碱性,利用在中温(40℃~60℃)环境下NH+转化为水合物NH3·H2O并部分以气态逸出:
另外在弱碱性环境下大部分的NH3·H2O在带催化阳极表面直接氧化为N2气逸出。
(2)电极板设计
阳极:基于零排放及回用的目的,电解过程不能带入新的污染物,同时考虑材料腐蚀影响,选择钛涂铱钌合金或钛镀铂金催化剂不溶阳极;
阴极:选用成本较低综合性能较优的钛板;
极板间距离:为达到将Cl-转化为气体逸出,需要更为密集的极板排布,经过不断的探索确定极板间距离必须保证D≤3CM,利用密集的极板距离使Cl-在阳极表面放电,造成Cl2局部过浓最终以气态逸出而不是溶入水中。
Cl--e→Cl2↑
(3)极板连接方式
为保证核心内容的实现,极板间距满足D≤3CM的情况下有多种连接方式,详细见附图。
(4)本发明电解处理系统最终产物为Cu单质和三种气体(占大部分的N2和Cl2、及少量的NH3·H2O),其中NH3·H2O和Cl2通过收集后通入碱性蚀刻液做为蚀刻液的有益成份回到蚀刻系统中循环利用,以补充蚀刻过程中消耗的氨和氯离子,实现充分利用,处理出水直接回用于蚀刻段水洗,最终实现零排放的目的。
本发明的有益效果:
①由于使用极密集电极间距离,使电解产物活性氯以气态逸出,有效去除废水中的氯离子;
②实现同时去除废水中的氨氮和氯离子,出水直接满足工业回用水要求,真正实现零排放;
③电解产物循环使用,成为碱性蚀刻液的有益成份而得到综合利用;
④没有反应副产物造成的二次污染,环保效应显著;
⑤电解过程无需使用电极填料,设施简化,节省成本;
⑥利用电解过程热效应维持污水处理所需温度,不用另设加热系统,进一步实现节能降耗。