申请日2010.04.22
公开(公告)日2010.12.29
IPC分类号C02F11/00; C02F103/16; C01G3/02
摘要
本发明公开了一种含铜电镀污泥加压氢还原制备氧化亚铜粉末的方法,包括预处理、氨浸出、加压氢还原和残渣固化等步骤,在加压氢还原反应之前,调节反应混合液pH值为6.0~7.0,高压釜内保持氢压力2~2.5MPa,温度130℃~160℃,转速400r/min~600r/min,反应50至90分钟,开盖冷却至室温,取出釜内生成物;过滤分离沉淀物和溶液,将得到的沉淀物用去离子水洗涤并烘干,即得到Cu2O粉末。本发明实现资源化利用,降低含铜电镀污泥对环境污染,通过控制二价铜还原的条件,制备Cu2O粉末,反应条件温和且成本较低,增加了从电镀污泥中回收的铜产品的种类。
摘要附图
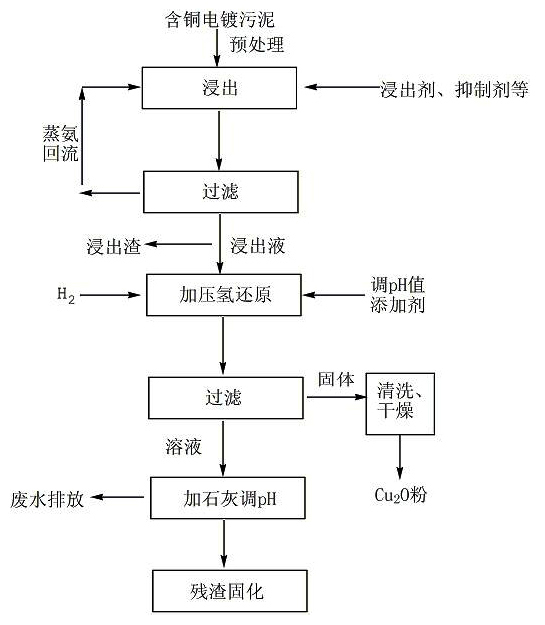
权利要求书
1.一种含铜电镀污泥加压氢还原制备氧化亚铜粉末的方法,其特征在于包括以下步骤:
①预处理,待处理的含铜电镀污泥在105℃~120℃的条件下干燥,研碎,过筛去除大颗粒物及沙粒;
②氨浸出,步骤①预处理后的电镀污泥转移到反应池中,按照氨水与硫酸铵的物质的量之比n(NH3·H2O): n((NH4)2SO4)= 1.5:1~4:1,氨水的摩尔浓度为5mol/L至15mol/L,以氨水与干燥的含铜电镀污泥的质量比为7:1~15:1的比例向反应池中加入作为浸出剂的氨水和硫酸铵固体,在10℃~30℃的温度内反应30至60分钟,分离溶液与沉渣,溶液蒸氨,所得清液即为浸出液;
③加压氢还原:调节步骤②的浸出液pH值为6.0~7.0,转入高压反应釜,盖好釜盖后依次用氮气和氢气置换釜内气体,继续通入氢气至釜内压力升至2~2.5MPa,此时打开磁力搅拌装置,设置转速为400r/min~600 r/min,打开加热装置,使釜内温度上升到130℃~160℃,待反应釜的压力表显示釜内压力开始下降时,开始计时,反应50至90分钟,反应结束后,在5℃至40℃的室内环境温度下开盖自然冷却,取出釜内生成物;过滤分离沉淀物和溶液,将得到的沉淀物用去离子水洗涤并烘干,即得到Cu2O粉末;
④残渣固化,向上述步骤③加压氢还原反应后的溶液中加入石灰水,调节溶液pH呈中性后,废水直接排放,所得残渣进行水泥固化处理。
2.根据权利要求1所述的含铜电镀污泥加压氢还原制备氧化亚铜粉末的方法,其特征在于:步骤③加压氢还原前,用硫酸溶液调节溶液pH值为6.2~7.0,反应混合液在高压反应釜内反应55至65分钟。
3.根据权利要求1所述的含铜电镀污泥加压氢还原制备氧化亚铜粉末的方法,其特征在于:步骤②向反应池中加入氨水和硫酸铵固体时,按照处理每克电镀污泥消耗氨水0.07~0.14摩尔,消耗硫酸氨固体5~8克的比例向反应池中加入。
4.根据权利要求1所述的含铜电镀污泥加压氢还原制备氧化亚铜粉末的方法,其特征在于:步骤③反应过程中维持釜内氢压力2~2.5MPa,温度130℃~160℃。
5.根据权利要求4所述的含铜电镀污泥加压氢还原制备氧化亚铜粉末的方法,其特征在于:步骤③反应过程中维持釜内温度为130℃~155℃。
6.根据权利要求1所述的含铜电镀污泥加压氢还原制备氧化亚铜粉末的方法,其特征在于:步骤①污泥研碎后所过筛的目数为150~250目。
7.根据权利要求3所述的含铜电镀污泥加压氢还原制备氧化亚铜粉末的方法,其特征在于:步骤②向反应池中加入氨水和硫酸铵固体时,按照每处理1克电镀污泥需要消耗10mol/L~15 mol/L的氨水7毫升至9毫升加入、消耗硫酸铵固体6克至7.5克加入。
说明书
含铜电镀污泥加压氢还原制备氧化亚铜粉末的方法
技术领域
本发明涉及一种从电镀污泥中回收有价金属的方法,特别涉及一种从含铜电镀污泥中制备Cu2O粉末的方法。
背景技术
电镀行业是国民经济中不可缺少的基础性行业,也是当今全球三大污染行业之一。电镀行业产生的固体废物主要是电镀污泥,因其所含重金属的质量分数高而被列为危险废物。近些年来,我国电镀企业的数量增长迅速,且大部分电镀企业规模较小、设备落后、管理水平低下,导致污泥产生量大且成分复杂。
电镀、冶金、化工等行业都会产生大量含重金属的电镀废水,一般采用简单有效的化学法处理后,重金属离子及其化合物沉淀析出,随之而来的是产生了大量含重金属的污泥,其中含有大量的铬、镉、镍、锌等有毒重金属,成分十分复杂。在我国《国家危险废物名录》(环发[1998]89号)所列出的47类危险废物中,电镀污泥占了其中的7大类,是一种典型的危险废物,若随意堆置对环境造成极大危害。目前,由于我国电镀行业存在厂点多、规模小、装备水平低及污染治理水平低等诸多问题,大部分电镀污泥仍只是进行简单土地填埋,甚至随意堆放,对环境造成了严重污染。
含铜电镀污泥中富含大量金属资源,等同于低品位矿石,其中铜含量超过8%,国内采用镀铜工艺时将会产生大量含铜的含铜电镀污泥,在目前金属资源紧缺的情况下,如果能够对其中的Cu等有色金属回收,进行资源化利用,将产生较好的经济效益和社会效益。
目前,含铜电镀污泥资源化利用技术主要有:1、湿法冶金回收重金属技术,该技术能从多种组分的电镀污泥中回收铜﹑镍﹑锌等重金属,资源回收层次比较高,处理效果较稳定。工艺过程主要包括浸出、置换、净化、制取硫酸镍和固化;采用本工艺可以得到品位在90%以上的海绵铜粉,铜的回收率达95%。但该技术采用置换方式来回收铜,置换效率低,费用偏高,且对铬未能有效回收,有一定的局限性。
2、离子交换膜法,一般采用液膜来进行回收。液膜包括无载体液膜、有载体液膜、含浸型液膜等。液膜分散于电镀污泥浸出液时,流动载体在膜外相界面有选择地络合重金属离子,然后在液膜内扩散,在膜内界面上解络。重金属离子进入膜内相得到富集,流动载体返回膜外相界面,如此过程不断进行,废水得到净化,重金属得到回收利用。这种方法能量转化率高,装置简单,操作容易,易控制、分离效率高;但是投资大、运行费用高,而且薄膜的寿命短,比较容易堵塞,因而操作管理烦琐,处理成本比较昂贵。
3、溶剂萃取法,铜在此工艺过程中以化学试剂CuSO4·5H2O或电解高纯铜的形式回收,初步经济分析表明,其产值抵消日常的运行费用,还具有较高的经济效益。整个工艺过程较简单,循环运行,基本不产生二次污染,环境效益显著。但是萃取法操作过程和设备较复杂,而且成本较高,工艺有待于进一步优化。
4、氢还原分离技术,在高压釜中氢还原分离制取铜、镍粉是比较成熟的技术,这种方法可分离回收电镀污泥氨浸产物中的铜、镍、锌等有价金属。对氨浸产物进行焙烧、酸溶处理后,进而氢还原分离出铜粉,然后在酸性溶液中还原提取镍粉,最后沉淀回收氢还原尾液中的锌,有价金属的回收率达98%~99%。这种方法可在液相体系、浆料体系通过各种工艺条件的变化分离和生产各种类型(粗、细、超细)的、各种型体(单一、复合)的金属粉末和金属包复材料。与其他分离方法相比,湿法氢还原方法流程简单,设备投资少,操作方便,产品质量好且产值较高,可以针对不同需要改变生产条件,获得不同纯度、不同粒度的铜、镍产品。
此外还有回收铜的肼还原技术和煅烧酸溶法,前者要求pH稳定在11以上;后者回收得到的铜盐含杂质较多,工艺有待进一步优化。
上述各种现有工艺所得到的铜的产物均是以金属铜的形式存在(除溶剂萃取法还可得到水合硫酸铜形式的产物),鲜少得到Cu2O产物,而Cu2O是无机化工原料,在颜料、防污涂料、焊膏、催化剂方面都有特殊的用途。
在由二价铜还原至铜单质的过程中,经历了二价铜到一价铜的还原和一价铜到铜单质的还原过程,步骤多且对反应条件的要求苛刻,而且成本较高;如果让还原反应停留在第一步得到氧化亚铜,则还原过程条件温和、工艺简单、步骤少且成本低;但是在实际操作中需要控制工艺条件,否则难以得到纯度高的氧化亚铜粉末。
发明内容
本发明的目的是解决上述电镀污泥的回收产物单一的问题,提供一种反应条件温和、成本较低的从含铜电镀污泥中得到氧化亚铜粉末的方法。
实现本发明目的的技术方案是一种含铜电镀污泥加压氢还原制备氧化亚铜粉末的方法,包括以下步骤:
①预处理,待处理的含铜电镀污泥在105℃~120℃的条件下干燥,研碎,过筛去除大颗粒物及沙粒;
②氨浸出,步骤①预处理后的电镀污泥转移到反应池中,按照氨水(指氢氧化铵)与硫酸铵的物质的量之比n(NH3·H2O): n((NH4)2SO4)= 1.5:1~4:1,氨水(指氢氧化铵的水溶液)的摩尔浓度为5mol/L至15mol/L,以氨水与干燥的含铜电镀污泥的质量比为7:1~15:1的比例向反应池中加入作为浸出剂的氨水(指氢氧化铵的水溶液)和硫酸铵固体,在10℃~30℃的温度内反应30至60分钟,分离溶液与沉渣,溶液蒸氨,所得清液即为浸出液;
③加压氢还原:调节步骤②的浸出液pH值为6.0~7.0,转入高压反应釜,盖好釜盖后依次用氮气和氢气置换釜内气体,继续通入氢气至釜内压力升至2~2.5MPa,此时打开磁力搅拌装置,设置转速为400r/min~600 r/min,打开加热装置,使釜内温度上升到130℃~160℃,待反应釜的压力表显示釜内压力开始下降时,开始计时,反应50至90分钟,反应结束后,在5℃至40℃的室内环境温度下开盖自然冷却,取出釜内生成物;过滤分离沉淀物和溶液,将得到的沉淀物用去离子水洗涤并烘干,即得到Cu2O粉末;
④残渣固化,向上述步骤③加压氢还原反应后的溶液中加入石灰水,调节溶液pH呈中性后,废水直接排放,所得残渣进行水泥固化处理。
上述步骤③加压氢还原前,用硫酸溶液调节溶液pH值为6.2~7.0,反应混合液在高压反应釜内反应55至65分钟。
上述步骤②向反应池中加入氨水(指氢氧化铵的水溶液)和硫酸铵固体时,按照处理每克电镀污泥消耗氨水(指氢氧化铵)0.07~0.14摩尔,消耗硫酸氨固体5~8克的比例向反应池中加入。
上述步骤③反应过程中维持釜内氢压力2~2.5MPa,温度130℃~160℃。
上述步骤③反应过程中维持釜内温度为130℃~155℃。
上述步骤①污泥研碎后所过筛的目数为150~250目。
上述步骤②向反应池中加入氨水(指氢氧化铵的水溶液)和硫酸铵固体时,按照每处理1克电镀污泥需要消耗10mol/L~15 mol/L的氨水7毫升至9毫升加入、消耗硫酸铵固体6克至7.5克加入。
本发明具有积极的效果:(1)本发明含铜电镀污泥的回收方法实现资源化利用,降低含铜电镀污泥对环境污染,成本较低,操作简单,工艺易实现,能够实现大规模的工业化生产。(2)本发明通过控制二价铜还原的条件,制备Cu2O粉末,增加了从电镀污泥中回收的铜产品的种类。(3)本发明利用加压氢还原技术,不存在杂质积累问题,排放的尾液中的主要重金属离子含量均控制在极低的范围内,基本不污染环境,对环境几乎无负担和危害,具有良好的环境和经济效益。