申请日2016.02.26
公开(公告)日2016.06.22
IPC分类号C02F3/30; C02F101/16
摘要
本发明的两段式去除水中氨氮的组合反应槽,包括第一反应槽和第二反应槽,反应槽底部设置有曝气头,反应槽底部接种有含有亚硝化菌菌落和厌氧氨氧化菌菌落的污泥;特征在于:反应槽进行微氧曝气,以便同时进行亚硝化和厌氧氨氧化过程,将氨氮转化为氮气。本发明的方法包括a).接种污泥;b).间歇进水;c).间歇曝气;d).亚硝化反应;e).厌氧氨氧化反应。本发明的反应槽及处理方法,两反应槽中同时进行亚硝化反应和厌氧氨氧化反应,使用两段式处理方式,提高处理效果。通过设置S形管,解决了以往厌氧氨氧化反应器容易污泥流失的缺点,保证了污泥具有最高的活性。省去了沉淀池及污泥返送附属流程和设备,结构简单、操作方便。
摘要附图
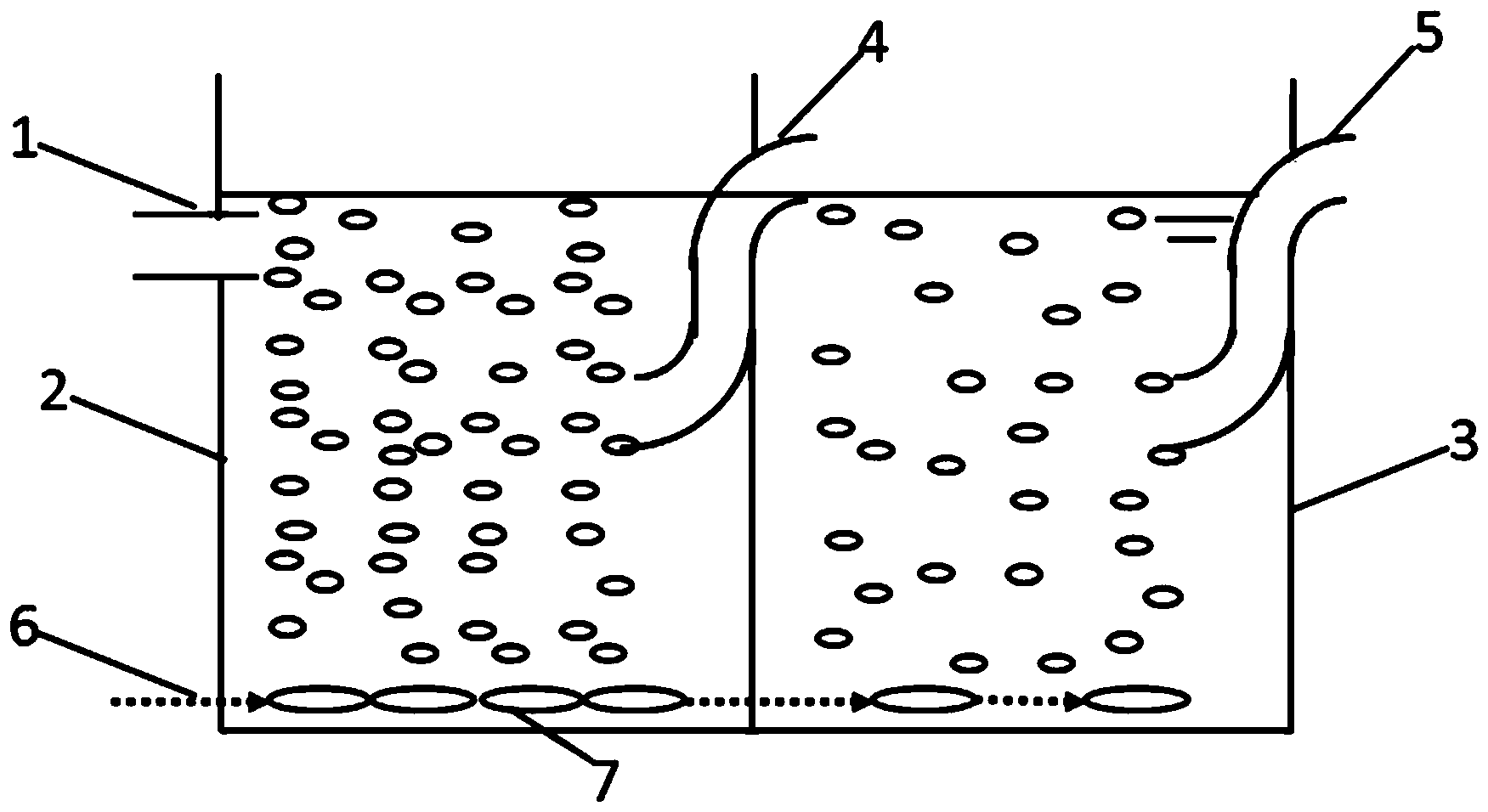
权利要求书
1.一种两段式去除水中氨氮的组合反应槽,包括相邻设置的第一反应槽(2)和第二反应槽(3),第一反应槽的上部开设有向其中注入待处理污水的进水口(1),第二反应槽的上部设置有将净化后污水排出的出水管,第一反应槽、第二反应槽的底部均设置有曝气头(7),曝气头连通有供气管(6);其特征在于:所述第一反应槽和第二反应槽的底部均接种有含有亚硝化菌菌落和厌氧氨氧化菌菌落的污泥;第一反应槽与第二反应槽通过连接管(4)相连通,以便将第一反应槽内的污水导流至第二反应槽内;曝气头实现对第一反应槽和第二反应槽中污水的微氧曝气,以便在两个反应槽内同时进行亚硝化和厌氧氨氧化过程,将污水中的氨氮转化为氮气,实现污水中氨氮的去除。
2.根据权利要求1所述的两段式去除水中氨氮的组合反应槽,其特征在于:所述连通管(4)和出水管(5)均为S形管,S形管的上端和下端均为弧度为90度的弯头,中间为连通两弯头的竖管;作为连通管的S形管的下端口位于第一反应槽内,上端口位于第二反应槽内,作为出水管的S形管的下端口位于第二反应槽内,上端口与外界相通,确保了污泥能够有效地停留在每个反应槽内,同时又可将失去活性没有沉淀能力的污泥自动排出。
3.根据权利要求1或2所述的两段式去除水中氨氮的组合反应槽,其特征在于:由于厌氧氨氧化过程是厌氧过程,过高的溶解氧会对厌氧氨氧化菌落产生抑制作用,因此控制第一反应槽(2)和第二反应槽(3)的微氧曝气的溶解氧值在0.2~0.4mg/l之间;同时,由于第二反应槽中氨氮浓度低于第一反应槽中氨氮的浓度,因此第二反应槽的曝气量应低于第一反应槽的曝气量。
4.根据权利要求1或2所述的两段式去除水中氨氮的组合反应槽,其特征在于:所述连通管(4)和出水管(5)的顶部高于第一反应槽(2)和第二反应槽(3)中的水面,连通管和出水管下端的进口分别位于第一反应槽和第二反应槽中水位的1/2至2/3位置处,防止沉淀下的或者上浮的污泥流失,绝大部分污泥保留在反应槽中。
5.根据权利要求1或2所述的两段式去除水中氨氮的组合反应槽,其特征在于:所述第一反应槽(2)和第二反应槽(3)的上端均开口,进水口(1)的高度稍低于水面,在进水过程中,通过污水的流动,增加空气向水体的自然溶氧。
6.一种基于权利要求1所述的两段式去除水中氨氮的组合反应槽的污水处理方法,其特征在于,通过以下步骤来实现:
a).接种污泥,在第一反应槽和第二反应槽的底部接种含有亚硝化菌和厌氧氨氧化菌菌落的污泥;
b).进水,待处理的污水通过进水口流入第一反应槽中,并经连通管由第一反应槽进入第二反应槽中,使得第一反应槽和第二反应槽中的水位到达出水管的出口高度;
c).间歇曝气,采用间歇式通入空气的方式,通过供气管和曝气头向第一反应槽和第二反应槽中通入空气,以使两反应槽中的污水中溶解适量的溶解氧;曝气的同时具有混合搅拌泥水混合物的作用,有利于增强微生物的活性,停止曝气期间用于污泥静置分离;
d).亚硝化反应,在第一反应槽和第二反应槽中,在亚硝化菌的作用下,氨氮以氧气为电子受体被转化为亚硝氮,转化污水中的部分氨氮,并消耗掉溶解氧;
e).厌氧氨氧化反应,在两反应槽中,由于处于微氧环境,厌氧氨氧化菌以氨氮为电子供体、亚硝氮为电子受体,将其转化为氮气,实现脱氮过程;
f).间歇进水,在停止曝气的后期污水通过进水口流入第一反应槽,由于第一反应槽与第二反应槽的连通性,第一反应槽的污水会通过连通管自动流入第二反应槽,第二反应槽的污水自动从出水口流出,实现污水中氨氮的去除。
说明书
一种两段式去除水中氨氮的组合反应槽及污水处理方法
技术领域
本发明涉及一种两段式去除水中氨氮的组合反应槽及污水处理方法,更具体的说,尤其涉及一种在反应槽中通过微氧曝气,同时实现亚硝化和厌氧氨氧化过程的两段式反应槽及污水处理方法,用以去除污水中的氮类污染物。
背景技术
随着我国经济生活水平的提高,居民用水量不断增加,产生的污水量也逐年递增,特别是其中的氮类污染物,给污水厂的运行带来极大的负担。氮类污染物在污水厂的去除,传统上靠主流的反硝化过程,不但工艺复杂,还需要加入大量的碳元素,运行成本很大。而在侧流产生的高浓度消化液也返回到主流中进行脱除,加剧了污水主流处理的难度。在工业领域,由于缺乏有效稳定运行的处理方法,众多高浓度的含氮废水没有得到妥善处理或处置。
近期,随着厌氧氨氧化工艺的实现,为含氮废水提供了良好的解决方法。主要有两种方式,一种为亚硝化过程和厌氧氨氧化过程分步进行的处理方式,另一种为一体式处理。但是,两种处理方法存在极大的缺点:前者由于需要先进行约40%的亚硝化,极难精确控制;后者基于传统处理装置反应器类型或者构造,在实际的运行中出现多种问题,例如污泥流失、设备复杂等。另外,工业含氮废水的处理多使用膜法处理,费用极高,成为经济发展的重大负担。急需一种结构简单,运行方便可靠的处理方法。
发明内容
本发明为了克服上述技术问题的缺点,提供了一种结构简单、运行方便、费用低廉的两段式去除水中氨氮的组合反应槽及污水处理方法。
本发明的两段式去除水中氨氮的组合反应槽,包括相邻设置的第一反应槽和第二反应槽,第一反应槽的上部开设有向其中注入待处理污水的进水口,第二反应槽的上部设置有将净化后污水排出的出水管,第一反应槽、第二反应槽的底部均设置有曝气头,曝气头连通有供气管;其特别之处在于:所述第一反应槽和第二反应槽的底部均接种有含有亚硝化菌菌落和厌氧氨氧化菌菌落的污泥;第一反应槽与第二反应槽通过连接管相连通,以便将第一反应槽内的污水导流至第二反应槽内;曝气头实现对第一反应槽和第二反应槽中污水的微氧曝气,以便在两个反应槽内同时进行亚硝化和厌氧氨氧化过程,将污水中的氨氮转化为氮气,实现污水中氨氮的去除。
本发明的两段式去除水中氨氮的组合反应槽,所述连通管和出水管均为S形管,S形管的上端和下端均为弧度为90度的弯头,中间为连通两弯头的竖管;作为连通管的S形管的下端口位于第一反应槽内,上端口位于第二反应槽内,作为出水管的S形管的下端口位于第二反应槽内,上端口与外界相通,确保了污泥能够有效地停留在每个反应槽内,同时又可将失去活性没有沉淀能力的污泥自动排出。
本发明的两段式去除水中氨氮的组合反应槽,由于厌氧氨氧化过程是厌氧过程,过高的溶解氧会对厌氧氨氧化菌落产生抑制作用,因此控制第一反应槽和第二反应槽的微氧曝气的溶解氧值在0.2~0.4mg/l之间;同时,由于第二反应槽中氨氮浓度低于第一反应槽中氨氮的浓度,因此第二反应槽的曝气量应低于第一反应槽的曝气量。
本发明的两段式去除水中氨氮的组合反应槽,所述连通管和出水管的顶部高于第一反应槽和第二反应槽中的水面,连通管和出水管下端的进口分别位于第一反应槽和第二反应槽中水位的1/2至2/3位置处,防止沉淀下的或者上浮的污泥流失,绝大部分污泥保留在反应槽中。
本发明的两段式去除水中氨氮的组合反应槽,所述第一反应槽和第二反应槽的上端均开口,进水口的高度稍低于水面,在进水过程中,通过污水的流动,增加空气向水体的自然溶氧。
本发明的两段式去除水中氨氮的组合反应槽的污水处理方法,其特别之处在于,通过以下步骤来实现:
a).接种污泥,在第一反应槽和第二反应槽的底部接种含有亚硝化菌和厌氧氨氧化菌菌落的污泥;b).进水,待处理的污水通过进水口流入第一反应槽中,并经连通管由第一反应槽进入第二反应槽中,使得第一反应槽和第二反应槽中的水位到达出水管的出口高度;c).间歇曝气,采用间歇式通入空气的方式,通过供气管和曝气头向第一反应槽和第二反应槽中通入空气,以使两反应槽中的污水中溶解适量的溶解氧;曝气的同时具有混合搅拌泥水混合物的作用,有利于增强微生物的活性,停止曝气期间用于污泥静置分离;d).亚硝化反应,在第一反应槽和第二反应槽中,在亚硝化菌的作用下,氨氮以氧气为电子受体被转化为亚硝氮,转化污水中的部分氨氮,并消耗掉溶解氧;e).厌氧氨氧化反应,在两反应槽中,由于处于微氧环境,厌氧氨氧化菌以氨氮为电子供体、亚硝氮为电子受体,将其转化为氮气,实现脱氮过程;f).间歇进水,在停止曝气的后期污水通过进水口流入第一反应槽,由于第一反应槽与第二反应槽的连通性,第一反应槽的污水会通过连通管自动流入第二反应槽,第二反应槽的污水自动从出水口流出,实现污水中氨氮的去除。
本发明的有益效果是:本发明的组合式反应槽及污水处理方法,通过设置两相邻的第一反应槽和第二反应槽,两反应槽的底部均接种有含有亚硝化菌和厌氧氨氧化菌菌落的污泥,通过对两反应槽进行为微曝气,使得两反应槽中可同时进行亚硝化反应和厌氧氨氧化反应,可有效地将污水中的氨氮去除。
通过将连通第一与第二反应槽的连通管设置为S形管,将第二反应槽上的出水管也设计为S形管,使得污水中失去活性没有沉淀能力的污泥可以排出,而具有活性的颗粒污泥停留在反应槽中,解决了以往厌氧氨氧化反应器容易污泥流失的缺点,保证了反应槽中污泥具有最高的活性。同时使用两段式处理方式,提高处理效果。省去了沉淀池及污泥返送等附属流程和设备,结构简单、操作方便。