申请日2010.07.27
公开(公告)日2011.08.24
IPC分类号C02F9/06; C02F1/66; C02F1/78; C02F1/52; C02F1/461
摘要
一种基于臭氧复合催化氧化的钻井废水深度处理方法,属于石油勘探、开发领域。针对当前钻井废水处理效果较差、成本较高的现状,提供一种低成本、效果好、可连续处理钻井废水的方法。本发明将pH值为8~9的钻井废水后先进行混凝处理,调清液pH值为2~4后,再进行微电解处理及氧化处理。采用本发明对经过生化处理的焦化废水进行深度处理,出水COD<100mg/L,色度去除率、硫化物去除率接近100%,对环境无二次污染。
摘要附图
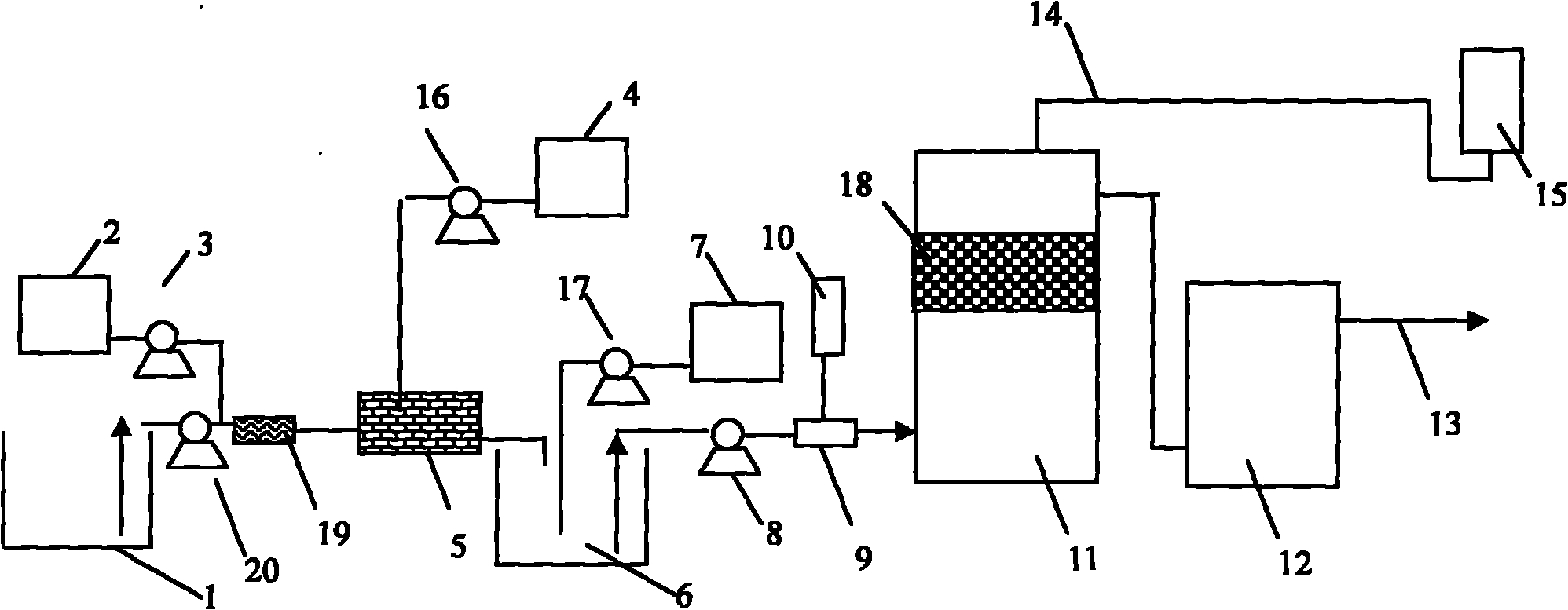
权利要求书
1.一种基于臭氧复合催化氧化的钻井废水深度处理方法,其特征在于,包括如下步骤:
(1)调节废水pH值为8~9;
(2)调节pH值后的废水进行混凝处理,加入混凝剂沉降至上清液浊度为10~30NTU时,泵出上层清液,调清液pH值为2~4;
(3)将步骤(2)中调节pH值后的废水在微电解槽内进行微电解处理;微电解槽内填充有内电解填料,废水与填料重量比为1∶1.5~1∶3,废水在微电解槽内处理时加入双氧水,废水与H2O2的重量比为1000∶1~12,氧化时间为0.5~4小时;
(4)经步骤(3)处理后的废水进入沉淀池,调节废水pH值为8~12,沉淀;
(5)步骤(4)处理后的废水中加入臭氧,每升废水加入280~900mg O3,在氧化反应器中进行处理;
(6)氧化反应器内装填有固体非均相催化剂,固体非均相催化剂体积与氧化反应器容积之比为1∶3~1∶6;废水在氧化反应器中的反应时间为20~40分钟;
(7)处理后的废水过滤后外排。
2.根据权利要求1所述的一种基于臭氧复合催化氧化的钻井废水深度处理方法,其特征在于,所述步骤(5)中的臭氧加入方式为:步骤(4)处理后的废水通过混合射流器进入氧化反应器,混合射流器上连接有臭氧发生器;当废水流经混合射流器时,开启臭氧发生器,臭氧发生器出口端气体中的臭氧浓度控制为70~90mg/L;混合射流器吸入的气体流量与通过混合射流器中的废水流量之比为4∶1~10∶1。
3.根据权利要求1或2所述的一种基于臭氧复合催化氧化的钻井废水深度处理方法,其特征在于,所述混凝剂优选由CaCl2、PJJ、PAC复配而成的混凝剂,CaCl2、PJJ、PAC的重量比为1∶1.5∶1.5。
4.根据权利要求1或2所述的一种基于臭氧复合催化氧化的钻井废水深度处理方法,其特征在于,所述的内电解填料,优选铁、铜与碳颗粒烧结的填料,铁、铜、碳的重量比为1∶0.1∶1.2。
5.根据权利要求1或2所述的一种基于臭氧复合催化氧化的钻井废水深度处理方法,其特征在于,所述的固体非均相催化剂优选TiO2负载掺杂稀土金属Ru的催化剂。
说明书
一种基于臭氧复合催化氧化的钻井废水深度处理方法
技术领域
本发明涉及一种钻井废水的处理方法,具体涉及采用臭氧复合催化氧化技术对钻井废水进行深度处理的方法,属于石油勘探、开发领域。
背景技术
钻井废水来自于废弃的钻井液和钻井过程中的各种生产用水,其中,导致环境污染的有害成分为油类、盐类、杀菌剂、某些化学添加剂、重金属(如汞、铜、铬、镉、锌、铅等)、高分子有机化合物生物降解产生的低分子有机化合物和碱性物质等,从而造成色度、COD、SS、石油类等主要的污染指标大量超标。另外钻井废水的组成和浓度随着地层结构、泥浆体系、钻井井深的变化而变化,还具有多变性、复杂性、分散性等特点。由于钻井废水的污染性较强,如果不经处理直接排放,将对环境造成巨大危害,因此解决钻井废水COD超标问题,已成为处理钻井废水的关键。
目前,国内外对钻井废水进行处理的主要技术方法可归纳为:物理法、化学法、生物法、物理-化学法。其中物理法和物理-化学处理技术常用在钻井废水预处理阶段,包括混凝处理法、中和-混凝处理法、酸碱处理法等。这些方法对悬浮物、胶体的去除率较高,但是对于水体中存在的大量溶解性有机物难以去除。为解决此类问题,还需要进行深度处理,主要包括:化学氧化法、生物处理、活性炭吸附等。然而这些方法都有各自的不足之处,如活性炭吸附能力小,成本较高;次氯酸钠氧化效率低,若采用催化剂又会造成镍的流失,同时引入新的污染物氯离子。Fenton试剂处理效果较好,也不会造成二次污染但反应时间比较长,它无法满足油田作业中快速,简单的要求。另外由于钻井废水的毒性高,生物处理法对钻井废水处理的实用性较低。于是,寻找一种快速、方便,能够对难处理的废钻井液以有效处理的工艺技术是迫在眉睫的。
发明内容
本发明的目的是针对当前钻井废水处理效果较差、成本较高的现状,提供一种低成本、效果好、可连续处理钻井废水的方法,具体步骤如下:
(1)调节废水pH值为8~9;
(2)调节pH值后的废水进行混凝处理,加入混凝剂沉降至上清液浊度为10~30NTU时,泵出上层清液,调清液pH值为2~4;
(3)将步骤(2)中调节pH值后的废水在微电解槽内进行微电解处理;微电解槽内填充有内电解填料,步骤(2)中调pH值后的废水与该填料的重量比为1∶1.5~1∶3,废水在微电解槽内处理时加入双氧水,废水与H2O2的重量比为1000∶1~12,氧化时间为0.5~4小时;
(4)经步骤(3)处理后的废水进入沉淀池,调节废水pH值为8~12,沉淀;
(5)步骤(4)处理后的废水中加入臭氧,每升废水加入280~900mg O3,在氧化反应器中进行处理;
(6)氧化反应器内装填有固体非均相催化剂,固体非均相催化剂体积与氧化反应器容积之比为1∶3~1∶6;废水在氧化反应器中的反应时间为20~40分钟;
(7)处理后的废水过滤后外排。
在本发明中,所述步骤(5)中加入臭氧主要是利用臭氧的高级氧化功能,臭氧的加入方式除常用的曝气方式加入废水中外,还可以在沉淀池与氧化反应器间增设一个混合射流器,混合射流器上连接有臭氧发生器,臭氧发生器可产生臭氧,当步骤(4)处理后的废水被水泵从沉淀池中泵出,并流经混合射流器时,开启臭氧发生器,臭氧发生器出口气体中的臭氧浓度控制为70~90mg/L;当废水流经混合射流器时,会产生负压,利用此负压将含臭氧的气体吸入混合射流器中,在混合射流器中进行气体和废水的两相混合后进入氧化反应器,混合射流器吸入的气体流量与通过混合射流器中的废水流量之比为4∶1~10∶1;氧化反应器内装有固体非均相催化剂,固体非均相催化剂体积与氧化反应器容积之比为1∶3~1∶6,实现以OH-和H2O2为主的均相催化过程和固体非均相催化剂的复合催化过程,废水在氧化反应器中的反应时间为20~40分钟;
针对上述步骤(2)中所述的混凝剂,优选由CaCl2、PJJ、PAC复配而成的混凝剂,CaCl2、PJJ、PAC的重量比为1∶1.5∶1.5。上述步骤(3)中所述的内电解填料,优选铁、铜与碳颗粒烧结的填料,铁、铜、碳的重量比为1∶0.1∶1.2。上述步骤(5)中所述的固体非均相催化剂优选TiO2负载掺杂稀土金属Ru的催化剂。
本发明的基本原理是:(1)混凝法是通过向水体中投加混凝剂破坏胶体的稳定性,使胶体粒子(简称胶粒)发生絮凝,产生絮凝物,并发生吸附作用,将废水中污染物吸附在一起,然后沉降而与水分离的方法。该法主要是利用双电层压缩、静电中和、吸附架桥、沉淀网捕等作用机理。固液分离是颗粒物在重力的作用下沉降。(2)偏酸性的废水在微电解槽内,以铁或其他金属作阳极、碳或其他物质作阴极在水中形成无数个微电池场,从而发生微电解反应,反应产生的新生态的氧原子具有极强的氧化性,可氧化水中的部分无机物和有机物;同时产生的新生态的氧原子具有很强的还原作用,使污水中的某些物质得以还原;另外,由于有机物参与阴极的还原反应,使得官能团发生了变化,改变原有机物性质,而且水中溶解的阳离子会形成羟基络合物,在污水中起混凝作用,有助于去除废水中的悬浮物质和胶体杂质。(3)经微电解处理后的污水中新生成有大量的Fe2+,因此可以作为催化剂强化H2O2氧化能力,形成经典的Fenton试剂,大大减轻后续臭氧氧化部分的有机负荷。(4)臭氧是一种强氧化剂,在碱性和催化剂存在的条件下,臭氧是以间接反应为主,臭氧会分解产生二次氧化剂——羟基自由基(·OH),·OH具有比臭氧更强的氧化能力,在与水中有机物反应时具有反应速度快、无选择性、无二次污染等优点。
本发明中,若使用铁、铜与碳颗粒的烧结的填料,更换周期为4~6个月;Fenton氧化主要利用内电解过程生成的Fe2+,无需外加亚铁盐作为催化剂;若自制臭氧,臭氧的制备主要通过空气制备,运行成本主要为电耗和催化剂的成本;采用本发明对经过生化处理的焦化废水进行深度处理,出水COD<100mg/L,色度去除率、硫化物去除率接近100%,对环境无二次污染。