申请日2015.04.07
公开(公告)日2015.06.17
IPC分类号C02F103/24; C02F9/14
摘要
一种制革废水的缺氧-好氧综合处理方法,包括以下步骤:(1)将制革生产过程中的废水分类预处理后充分混合;(2)将混合后的废水混凝沉淀处理;(3)将沉淀后的上清液引入缺氧-好氧池,进行硝化和反硝化反应;(4)缺氧-好氧池处理后的废水进入至二沉池沉淀处理,沉淀后的上清液直接排放或根据标准要求进行深度处理,沉淀后的污泥回流至缺氧-好氧池;(5)将混凝沉淀池中的污泥和二沉池中的剩余污泥输送至污泥浓缩池,再由污泥脱水机脱水成泥饼后外运。本发明能够充分均衡进入后续处理单元的水质和水量,有效降低生化系统的处理负荷,改善污泥的沉降性能,快速提升系统的硝化和反硝化效率,防止污泥流失,稳定处理效果,确保上清液出水水质。
摘要附图
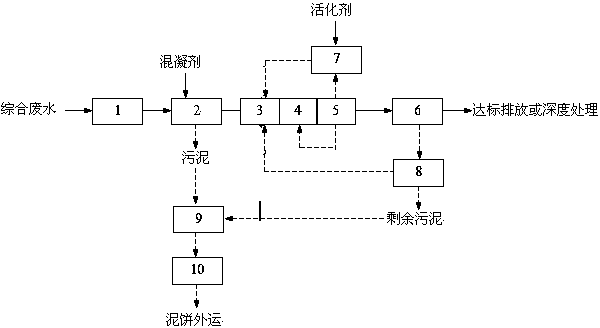
权利要求书
1.一种制革废水的缺氧-好氧综合处理方法,其特征是,包括以下步骤:
(1)将制革生产过程中的含硫废水、含铬废水或其它废水分类预处理后均引入调节池, 进行充分混合;
(2)将在调节池混合后的废水提升至混凝沉淀池进行混凝沉淀处理,混凝沉淀池包括混 凝区和沉淀区,通过控制混凝区进水口端混凝剂的投加量控制上清液pH值为7-10、S2-≤ 50mg/L、总铬<1.5mg/L以及SS≤500mg/L;
(3)将沉淀后的上清液引入缺氧-好氧池,进行硝化和反硝化反应,缺氧-好氧池由缺氧 区和好氧区串联组成,且缺氧区前段设有选择反应区;控制缺氧-好氧池中的混合液污泥浓度 MLSS为4g/L-6g/L,温度为15-30℃,控制缺氧区的溶解氧浓度≤0.5mg/L,好氧区的溶解氧 浓度为2mg/L-4mg/L;
(4)缺氧-好氧池处理后的废水进入二沉池沉淀处理,沉淀后的上清液直接排放或根据 标准要求进行深度处理,沉淀后的污泥回流至缺氧-好氧池;
(5)将混凝沉淀池中的污泥和二沉池中的剩余污泥输送至污泥浓缩池,再由污泥脱水机 脱水成泥饼后外运。
2.根据权利要求1所述的制革废水的缺氧-好氧综合处理方法,其特征是,所述步骤(1)中 调节池的废水停留时间不小于20小时,调节池内的曝气量不小于1.5m3/m2·h。
3.根据权利要求1所述的制革废水的缺氧-好氧综合处理方法,其特征是,所述步骤(2)中 混凝区内废水的反应时间为10分钟-15分钟,沉淀区表面负荷为0.4-0.8m3/m2·h,停留时间 为4-6小时。
4.根据权利要求1所述的制革废水的缺氧-好氧综合处理方法,其特征是,所述步骤(3)中 的选择反应区的水力停留时间为1-3小时;缺氧区的水力停留时间小时=14*[进水总氮浓度 mg/L-出水总氮浓度mg/L]/[混合液污泥浓度mg/L*脱氮速率],其中脱氮速率为 0.03kgNO3-N/kgMLSS.d至0.08kgNO3-N/kgMLSS.d;好氧区停留时间小时=24*[进水氨氮浓度 mg/L-出水氨氮浓度mg/L]/[氨氮负荷*混合液污泥浓度mg/L],其中氨氮负荷为0.02 kgNH3-N/kgMLSS.d至0.05kgNH3-N/kgMLSS.d。
5.根据权利要求1所述的制革废水的缺氧-好氧综合处理方法,其特征是,所述步骤(3)中 的选择反应区和缺氧区内设有混合装置,好氧区内设有曝气装置。
6.根据权利要求1所述的制革废水的缺氧-好氧综合处理方法,其特征是,所述步骤(3)中 好氧区内设有混合液回流设施,将好氧区内的混合液回流至缺氧区,混合液回流比%=70*[进 水总氮浓度mg/L-出水总氮浓度mg/L]/出水总氮浓度mg/L-污泥回流比%。
7.根据权利要求1所述的制革废水的缺氧-好氧综合处理方法,其特征是,所述步骤(3)中的 缺氧-好氧池内设有浮渣收集和溢流设施,将缺氧-好氧池内的浮泥溢流至缺氧-好氧池旁的污 泥活化池内;污泥活化池的容积m3=进水流量m3/d/24,通过在污泥活化池内投加脱脂酶、硅 藻土或微生物菌剂提高浮泥活性后,再重新提升至缺氧-好氧池中,从而提高缺氧/好氧池内 的硝化和反硝化处理效率,改善活性污泥的沉降性能,防止污泥膨胀和流失。
8.根据权利要求1所述的制革废水的缺氧-好氧综合处理方法,其特征是,所述步骤(4)中 二沉池的表面负荷为0.4-0.8m3/(m2·h),停留时间=4-6小时;二沉池沉淀的污泥回流至缺 氧-好氧池的选择反应区内,控制其回流比为100%-200%。
9.根据权利要求1所述的制革废水的缺氧-好氧综合处理方法,其特征是,所述步骤(5)中 污泥浓缩池固体负荷不大于80kg/m2·d,停留时间为14-20小时。
说明书
一种制革废水的缺氧-好氧综合处理方法
技术领域
本发明涉及一种制革废水的处理方法,属于污水处理技术领域。
背景技术
皮革废水的特点是S2-、Cr3+、COD、BOD5、氨氮和总氮浓度高,并含有大量的氯化物和硫 酸盐等,且各工段废水水量和水质差异极大。即使将浸灰脱毛废水、铬鞣废水等分别进行了 分类预处理,混合后的综合废水污染物成分仍然复杂、污染负荷依然很大。因此,对于综合 废水,通常采用物化处理和生化处理相结合的方法,即先对废水进行物化处理,使得废水的 环境适合微生物生存后再进行生化处理,必要时,生化出水还需进一步进行深度处理,使废 水符合标准要求。
目前,常用的物化处理方法主要有:混凝沉淀法、吸附法、高级氧化法、气浮法等(其 中的混凝沉淀、气浮等工艺主要用于生化前处理,吸附法和高级氧化法多用于深度处理)。生 化处理方法主要包括A/O(缺氧/好氧法)、A/A/O(厌氧/缺氧/好氧法)、氧化沟、SBR(间歇 式活性污泥法)和接触氧化法等。这些工艺有效地提高了废水中氨氮和COD的去除效果。但 在处理COD、总氮和氨氮浓度高、含盐量高的皮革废水时,往往存在着总停留时间长、占地 面积大、投资/运行费用高、去除率低、运行管理复杂、处理效果不稳定的弊病。近年来, 随着环保标准的加严,特别是增加了对总氮指标的控制,现有技术很难满足新标准的要求, 为此,一些制革企业开始使用投加微生物的方法,即通过投加某些特种微生物,以提高COD、 氨氮和总氮的去除效率。但由于这些工艺需持续投加特种菌,极大的提高了污水处理工程的 运行费用。
中国专利文献CN103224309A公开了一种皮革废水处理系统及处理工艺,废水经粗细格栅 依次进入沉砂池、曝气调节池,调节后的废水经过混凝沉淀、气浮去除水中悬浮性污染物后, 再依次进入水解酸化池、生物选择池和A/O脱氮池,进行硝化和反硝化反应,反应后的废水 依次进入二沉池和砂滤池,并由砂滤池排放。但该工艺主要针对废水中的氨氮和COD进行控 制,未充分考虑对废水中总氮的去除效果,也未考虑应对进水负荷冲击和生化系统污泥膨胀 或上浮的生物强化和应急措施,并且未公开该工艺的相关参数及处理效果。
发明内容
本发明的目的在于克服现有制革废水处理技术存在的不足,提供一种能够高效削减皮革 废水中COD、氨氮和总氮的制革废水的缺氧-好氧综合处理方法,该方法运行管理方便,运行 成本低,出水水质稳定。
本发明的制革废水的缺氧-好氧综合处理方法,包括以下步骤:
(1)将制革生产过程中的含硫废水、含铬废水或其它废水分类预处理后均引入调节池, 进行充分混合;
(2)将在调节池混合后的废水提升至混凝沉淀池进行混凝沉淀处理,混凝沉淀池包括混 凝区和沉淀区,通过控制混凝区进水口端混凝剂的投加量控制上清液pH值为7-10、S2-≤ 50mg/L、总铬<1.5mg/L以及SS(固体悬浮物浓度)≤500mg/L;
(3)将沉淀后的上清液引入缺氧-好氧池,进行硝化和反硝化反应,缺氧-好氧池由缺氧 区和好氧区串联组成,且缺氧区前段设有选择反应区;控制缺氧-好氧池中的混合液污泥浓度 为4g/L-6g/L,温度为15-30℃,控制缺氧区的DO(溶解氧浓度)≤0.5mg/L,好氧区的DO (溶解氧浓度)为2mg/L-4mg/L;
(4)缺氧-好氧池处理后的废水进入二沉池沉淀处理,沉淀后的上清液直接排放或根据 标准要求(国家或地方排放标准)进行深度处理(如采用高级氧化、吸附等方法),沉淀后的 污泥回流至缺氧-好氧池;
(5)将混凝沉淀池中的污泥和二沉池中的剩余污泥输送至污泥浓缩池,再由污泥脱水机 脱水成泥饼后外运。
所述步骤(1)中调节池的废水停留时间不小于20小时,调节池内的曝气量不小于 1.5m3/m2·h。
所述步骤(2)中混凝区内废水的反应时间为10分钟-15分钟,沉淀区表面负荷为 0.4-0.8m3/(m2·h),停留时间为4-6小时;
所述步骤(3)中的选择反应区的水力停留时间为1-3小时;缺氧区的水力停留时间(小 时)=14*[进水总氮浓度(mg/L)-出水总氮浓度(mg/L)]/[混合液污泥浓度(mg/L)*脱氮速率], 其中脱氮速率为0.03kgNO3-N/kgMLSS.d至0.08kgNO3-N/kgMLSS.d;好氧区停留时间(小时) =24*[进水氨氮浓度(mg/L)-出水氨氮浓度(mg/L)]/[氨氮负荷*混合液污泥浓度(mg/L)], 其中氨氮负荷为0.02kgNH3-N/kgMLSS.d至0.05kgNH3-N/kgMLSS.d。
所述步骤(3)中的选择反应区和缺氧区内设有混合装置,好氧区内设有曝气装置。
所述步骤(3)中好氧区内设有混合液回流设施,将好氧区内的混合液回流至缺氧区,混 合液回流比(%)=70*[进水总氮浓度(mg/L)-出水总氮浓度(mg/L)]/出水总氮浓度(mg/L)-污泥 回流比(%)。
所述步骤(3)中的缺氧-好氧池内设有浮渣收集和溢流设施,将缺氧-好氧池内的浮泥溢流 至缺氧-好氧池旁的污泥活化池内;污泥活化池的容积(m3)=进水流量(m3/d)/24,通过在 污泥活化池内投加脱脂酶、硅藻土或微生物菌剂提高浮泥活性后,再重新提升至缺氧-好氧池 中,从而提高缺氧/好氧池内的硝化和反硝化处理效率,改善活性污泥的沉降性能,防止污泥 膨胀和流失。
所述步骤(4)中二沉池的表面负荷为0.4-0.8m3/(m2·h),停留时间=4-6小时;二沉池 沉淀的污泥回流至缺氧-好氧池的选择反应区内,控制其回流比为100%-200%。
所述步骤(5)中污泥浓缩池固体负荷不大于80kg/(m2·d),停留时间为14-20小时。
通过采用前述技术方案,本发明具有以下积极有益效果:
(1)本发明通过在调节池内长时间的曝气混合,能够充分均衡进入后续处理单元的水质 和水量,通过混凝沉淀去除废水中颗粒和胶体性状的COD和油脂,有效降低生化系统的处理 负荷,改善污泥的沉降性能。
(2)本发明采用缺氧/好氧生化处理工艺,根据进水水质特点,通过控制缺氧-好氧池的 溶解氧、污泥和混合液回流比等参数,优化硝化反硝化环境,使缺氧/好氧反应池内同时实现 脱氮工艺中的传统硝化反硝化、短程硝化反硝化和同步硝化反硝化,在不外加碳源和碱度的 前提下,仍能显著提高脱氮效率。采用本发明处理制革综合废水,生化出水中的COD≤200mg/L、 氨氮≤10mg/L、总氮≤40mg/L。
(3)本发明能够通过向缺氧/好氧池旁的污泥活化池内投加脱脂酶,降低活性污泥中的 油脂含量,抑制污泥上浮;通过投加硅藻土提高活性污泥的凝聚性,改善污泥的沉降性能; 通过投加硝化菌,快速提升系统的硝化效率。
(4)本发明采用较高的污泥回流比,能够有效防止或减缓因沉淀池内废水反硝化导致的 污泥上浮现象,防止污泥流失,确保上清液出水水质。